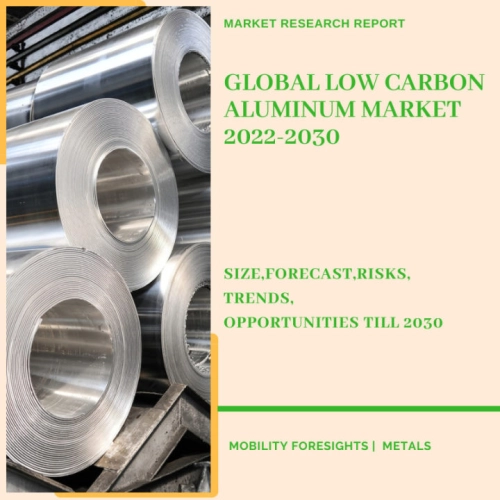
- Get in Touch with Us
Last Updated: Apr 25, 2025 | Study Period: 2022-2030
The distinctive qualities of aluminium, a vital building material, include its lightweight, simplicity of extrusion into any shape, and superior durability. These qualities, along with an increase in building and remodelling across the globe, help to fuel aluminum's rising demand.
Primary aluminium, or aluminium created by smelting bauxite or nepheline ore, is a raw material that uses a lot of electricity. Four to five percent of the world's electricity consumption is met by its generation. Aluminium with a low carbon content is a crucial component of more environmentally friendly building and remodelling. Low-carbon aluminium is defined as primary aluminium produced entirely with renewable energy.
Aluminium has a considerable potential to lower product emissions because it is a highly circular and entirely recyclable material. However, fewer than 30% of the world's demand can now be met by recycling.
The Global low carbon aluminum market accounted for $XX Billion in 2021 and is anticipated to reach $XX Billion by 2030, registering a CAGR of XX% from 2022 to 2030.
The largest aluminium producer in India, Vedanta Aluminium, took a step toward its goal of becoming carbon-neutral by launching a low-carbon brand.
Vedanta Aluminium announced two product lines under the Restora brand: Restora (low carbon aluminium) and Restora Ultra (ultra-low carbon aluminium). The company claimed to be the first significant non-ferrous metals producer in India to produce low carbon goods (primary aluminium) for customers around the world.
Customers who care about the environment have expressed interest in the first production volume of Restora and Restora Ultra aluminium, which is 100 kilo tonnes. Restora has a GHG emission intensity that is "well" below 4 tonnes of CO2 equivalent per tonne of aluminium manufactured, which is the global threshold for aluminium to be considered as low carbon aluminium.
A low-carbon recycling and rolling factory will cost $2.5 billion to erect in Bay Minette, Alabama, according to a statement from Novelis Inc. of Atlanta. The company is currently working on the site and anticipates commissioning to start in the upcoming years.
The Bay Minette, Alabama, factory of Novelis will initially have a 600 kilotonne annual capacity for finished aluminium goods targeted at the beverage container market with flexibility for automotive and speciality production as well.
At its Alma smelter in Lac-Saint-Jean, Quebec, Rio Tinto is spending US$188 million to enhance production capacity for low-carbon, high-value aluminium billets by 202,000 metric tonnes.
The current casting centre at Rio Tinto's Alma factory will be enlarged to make room for new machinery, such as a casting pit and furnaces, enabling a greater proportion of the produced aluminium to be turned into billets with higher value.
Taishet Aluminium Smelter (TaAZ), the most cutting-edge low-carbon aluminium production facility in the world, has opened in Taishet, Siberia. RUSAL, a major global aluminium manufacturer, has committed to decarbonizing its operations and supply networks for consumer goods.
Modern gas cleaning technology, a closed water circulation system, and operating on clean electricity from Siberian hydroelectric power plants make the state-of-the-art smelter one of the cleanest in the world. This combination has minimal environmental impact. The lowest CO2 emissions in the sector will be from the full scope.
Norsk Hydro, a Norwegian aluminium producer, recently announced a new round of investments aimed at addressing the demand for low-carbon aluminium from the European automobile sector. The news coincides with an increased emphasis on sustainability and a desire by businesses like Hydro to fulfil the rising demand for the manufacturing of low-carbon aluminium, which has led to an increase in European scrap prices.
Sl no | Topic |
1 | Market Segmentation |
2 | Scope of the report |
3 | Abbreviations |
4 | Research Methodology |
5 | Executive Summary |
6 | Introduction |
7 | Insights from Industry stakeholders |
8 | Cost breakdown of Product by sub-components and average profit margin |
9 | Disruptive innovation in the Industry |
10 | Technology trends in the Industry |
11 | Consumer trends in the industry |
12 | Recent Production Milestones |
13 | Component Manufacturing in US, EU and China |
14 | COVID-19 impact on overall market |
15 | COVID-19 impact on Production of components |
16 | COVID-19 impact on Point of sale |
17 | Market Segmentation, Dynamics and Forecast by Geography, 2022-2030 |
18 | Market Segmentation, Dynamics and Forecast by Product Type, 2022-2030 |
19 | Market Segmentation, Dynamics and Forecast by Application, 2022-2030 |
20 | Market Segmentation, Dynamics and Forecast by End use, 2022-2030 |
21 | Product installation rate by OEM, 2022 |
22 | Incline/Decline in Average B-2-B selling price in past 5 years |
23 | Competition from substitute products |
24 | Gross margin and average profitability of suppliers |
25 | New product development in past 12 months |
26 | M&A in past 12 months |
27 | Growth strategy of leading players |
28 | Market share of vendors, 2022 |
29 | Company Profiles |
30 | Unmet needs and opportunity for new suppliers |
31 | Conclusion |
32 | Appendix |