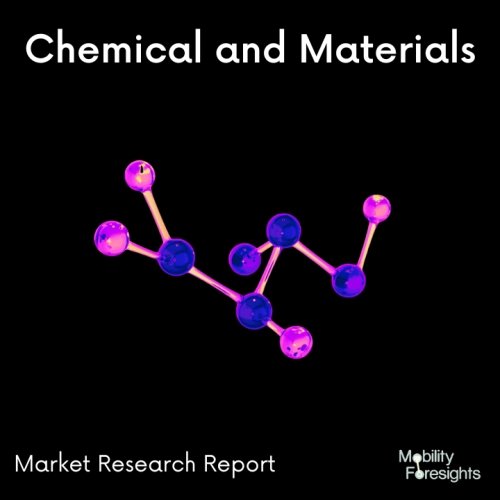
- Get in Touch with Us
Last Updated: Apr 25, 2025 | Study Period: 2024-2030
Low-friction plastics are self-lubricating materials with exceptional slide qualities, which produce flawless gliding performance. Here is how such materials can be essential components of tough application areas including conveyor systems, bearings, and industrial machinery.
Polytetrafluoroethylene, also known as PTFE, is frequently used in sliding applications because of its low coefficient of friction. In addition to PTFE, the traditional bearing and wear materials made of polyimide, PEEK, PPS, Nylon, Acetal, and polyester are also renowned for their good sliding friction capabilities.
The Global Low Friction Plastic market accounted for $XX Billion in 2023 and is anticipated to reach $XX Billion by 2030, registering a CAGR of XX% from 2024 to 2030.
Low friction plastic was introduced by CELANESE. These specialized plastics with low wear and friction are designed for sliding and moving parts used in anything from conveyors to automobiles to orthopedic implants. In order for OEMs to meet consumer demand and maintain their competitiveness, it is more difficult to create smaller, tougher, higher performing goods quickly and cost effectively.
To meet the most demanding tribological requirements of our customers, Celanese has created the broadest, most technologically sophisticated engineering polymer platform.
This platform keeps improving in terms of strength, durability, and wear. Because there are so many factors outside of the system that can affect tribological behavior, Celanese experts consult with producers to identify the most appropriate advanced engineering polymers for each application.
As a result of the exacting requirements used in the development of Celanese polymers, moving parts produce minimal to no noise, minimum friction, and can tolerate high temperatures, chemical contact, and speeds.
Additionally, by using these polymers, producers can do away with oil, grease, or other lubrication additives, which removes dust and filth and enhances mechanical performance and service life.
The most cutting-edge engineering polymers are included in the Celanese tribology product line to satisfy rising trends in a variety of industry categories, such as stronger, more adaptable conveyor systems for manufacturers and lighter, more durable bearings and bushings for consumer goods.
Sl no | Topic |
1 | Market Segmentation |
2 | Scope of the report |
3 | Abbreviations |
4 | Research Methodology |
5 | Executive Summary |
6 | Introduction |
7 | Insights from Industry stakeholders |
8 | Cost breakdown of Product by sub-components and average profit margin |
9 | Disruptive innovation in the Industry |
10 | Technology trends in the Industry |
11 | Consumer trends in the industry |
12 | Recent Production Milestones |
13 | Component Manufacturing in US, EU and China |
14 | COVID-19 impact on overall market |
15 | COVID-19 impact on Production of components |
16 | COVID-19 impact on Point of sale |
17 | Market Segmentation, Dynamics and Forecast by Geography, 2024-2030 |
18 | Market Segmentation, Dynamics and Forecast by Product Type, 2024-2030 |
19 | Market Segmentation, Dynamics and Forecast by Application, 2024-2030 |
20 | Market Segmentation, Dynamics and Forecast by End use, 2024-2030 |
21 | Product installation rate by OEM, 2023 |
22 | Incline/Decline in Average B-2-B selling price in past 5 years |
23 | Competition from substitute products |
24 | Gross margin and average profitability of suppliers |
25 | New product development in past 12 months |
26 | M&A in past 12 months |
27 | Growth strategy of leading players |
28 | Market share of vendors, 2023 |
29 | Company Profiles |
30 | Unmet needs and opportunity for new suppliers |
31 | Conclusion |
32 | Appendix |