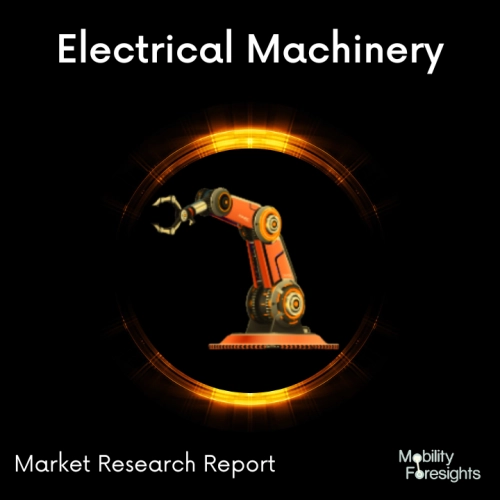
- Get in Touch with Us
Last Updated: Apr 25, 2025 | Study Period: 2024-2030
Low Inertia (MPL) Servo Motors are high-output brushless motors that employ cutting-edge design elements to minimise motor size while considerably increasing torque.
These small brushless servo motors are made to be compact and to withstand the rigors of high-performance motion systems. A hefty, swiftly moving object will resist changing its velocity if it has a lot of inertia.
It is fairly simple to alter an object's motion if it has minimal inertia, such as a feather resting on a table. One of the most crucial aspects of servo system sizing is inertia, or more precisely, inertia ratio. It can be used to gauge how effectively the motor can control the load's acceleration and deceleration.
The Global Low inertia Servo Motor market accounted for $XX Billion in 2023 and is anticipated to reach $XX Billion by 2030, registering a CAGR of XX% from 2024 to 2030.
With the introduction of a servo drive and motor package, motion expert TRIO Motion Technology, a part of the E stun Group, has increased the selection of motion controllers available.
With a comprehensive plug-and-play solution, OEMs may now take advantage of TRIO's specialized motion control performance, allowing for quicker machine development and maximum cost effectiveness.
The Motion Perfect 5 application is used to program me the DX4 servo drive, which is compatible with TRIO's slice I/O and controller systems. This quickens the development and commissioning of applications for OEMs in sectors like packaging, medicine, metal, CNC, robotics, and 3C electronics.
With the matching MXL low inertia and MXM medium inertia servo motors, the new DX4 servo drive extends control performance to the motor shaft, enabling quick and precise placement.
The drive includes functional safety dual STO, Ether CAT update speeds down to 125 s, and 350% overload for high dynamic applications (SIL3, PLe). The motors provide absolute multi-turn 23-bit capability for better placement.
The DX4 servo drive runs at 200V AC and has a power range of 50W to 3kW in a very small package. With a narrow frontal area and no stacking gap, it has one of the smallest footprints accessible.
Additional control functionality is kept within the Motion Coordinator and I/O slices, which further reduces dimensions. According to TRIO's design philosophy of "what you need and nothing more," scalable functionality has also been created to be cost-effective and the OEM only pays for the capabilities they require.
Due to the DX4 servo drive's lack of a need for additional onboard functionality, costs are drastically reduced. For systems with many axes, savings are even more pronounced.
Sl no | Topic |
1 | Market Segmentation |
2 | Scope of the report |
3 | Abbreviations |
4 | Research Methodology |
5 | Executive Summary |
6 | Introduction |
7 | Insights from Industry stakeholders |
8 | Cost breakdown of Product by sub-components and average profit margin |
9 | Disruptive innovation in the Industry |
10 | Technology trends in the Industry |
11 | Consumer trends in the industry |
12 | Recent Production Milestones |
13 | Component Manufacturing in US, EU and China |
14 | COVID-19 impact on overall market |
15 | COVID-19 impact on Production of components |
16 | COVID-19 impact on Point of sale |
17 | Market Segmentation, Dynamics and Forecast by Geography, 2024-2030 |
18 | Market Segmentation, Dynamics and Forecast by Product Type, 2024-2030 |
19 | Market Segmentation, Dynamics and Forecast by Application, 2024-2030 |
20 | Market Segmentation, Dynamics and Forecast by End use, 2024-2030 |
21 | Product installation rate by OEM, 2023 |
22 | Incline/Decline in Average B-2-B selling price in past 5 years |
23 | Competition from substitute products |
24 | Gross margin and average profitability of suppliers |
25 | New product development in past 12 months |
26 | M&A in past 12 months |
27 | Growth strategy of leading players |
28 | Market share of vendors, 2023 |
29 | Company Profiles |
30 | Unmet needs and opportunity for new suppliers |
31 | Conclusion |
32 | Appendix |