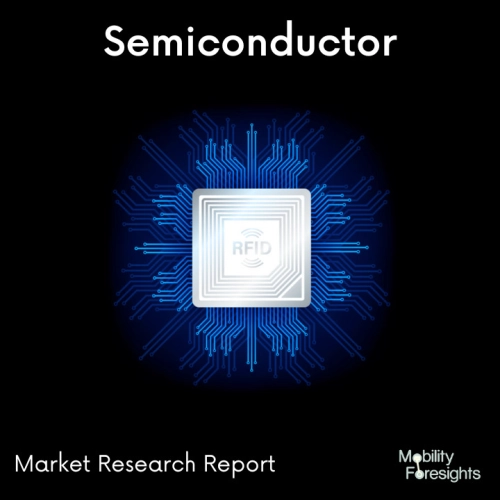
- Get in Touch with Us
Last Updated: Apr 25, 2025 | Study Period: 2024-2030
Chemical vapour deposition technology known as low pressure chemical vapour deposition (LPCVD) uses heat to start a precursor gas reaction on a solid substrate.
The solid phase material is created by this surface reaction. Low pressure (LP) is utilised to reduce any unintended gas phase reactions and improve substrate uniformity.
A quartz tube reactor with a cold or hot wall can be used for the LPCVD process. High throughput is possible with batch processing in hot walled furnaces.
Additionally, they offer good temperature uniformity, producing uniform films as a result. The fact that deposition also happens on the furnace walls, which necessitates greater maintenance for cleaning or eventual tube replacement to prevent flaking of the deposited material and consequent particle pollution, is a drawback of hot wall systems.
LPCVD can be used to deposit polysilicon, silicon nitride, silicon oxynitride, and silicon dioxide. For structures that need electrical isolation, most LPCVD coatings can provide sidewall protection since they are fairly conformal.
The temperature, the kind of LPCVD deposition being used, and, in the case of a trench feature, the aspect ratio of the feature, all affect how much sidewall coverage is applied.
The conformity is often better the higher the process temperature. Despite the films' reasonable conformity, keyhole creation during filling trenches can still be a problem since top and sidewall deposition rates differ.
There are three ways to deposit silicon oxide, and each has unique features. As long as the aspect ratio is not too large, high temperature oxide, which is deposited at and is fairly conformal, is appropriate for sidewall coating and some trench infill applications.
In order to deposit thin films from gas-phase precursors at subatmospheric pressures, LPCVD is a thermal technique. Usually, the process parameters are chosen so that the temperature-dependent rate of the surface reaction serves as a growth rate limiter.
With such fine temperature control, perfect wafer-to-wafer, run-to-run, and between-wafer uniformities can be achieved.
The nitride films required to construct high-Q nitride resonators have been prepared using TYTAN nitride LPCVD equipment.
With the use of a TYTAN nitride system, Q values of a few million have been discovered. It has been demonstrated that TYTAN nitride LPCVD tubes can produce top-quality, hydrogen bond-free nitride layers up to a few um in thickness.
The tool can be used continuously for several weeks because of Tystar systems' distinctive design and engineering.
The Global Low Pressure Chemical Vapour Deposition (LPCVD) System market accountedfor $XX Billion in 2023 and is anticipated to reach $XX Billion by 2030, registering a CAGR of XX% from 2024 to 2030.
The SiNergy(TM) Centura(R), a novel single-wafer LPCVD method for producing crucial silicon nitride (SiN) film layers in transistor architectures of micron and below devices, has been announced by Applied Materials, Inc.
SiNergy offers considerable benefits in technology, productivity, and cost of ownership (COO) over furnaces for a wide range of process applications, meeting the strict requirements of the most cutting-edge, cost-sensitive, volume production environments.
When compared to furnaces, the SyNergy technology enables chipmakers to reduce a wafer's temperature exposure by more than an order of magnitude, enabling applications such as shallow trench isolation layers, sensitive sidewall spacers, and etch stops.
SiNergy's single-wafer LPCVD process is completed in minutes as opposed to the hours needed for batch furnaces, offering noticeably better control over dopant diffusion, which is essential for preserving electrical performance.
SiNergy makes use of Applied Materials' Remote Plasma Clean technology, which further decreases particulates, increases throughput, increases the lifespan of hardware and consumables, and produces almost no greenhouse emissions.
A dual-zone ceramic resistive heater is used in the system's xZ chamber, which offers remarkable temperature uniformity and productivity over a wide range of temperatures and pressures.
By adjusting the deposition rate while maintaining a constant overall process time, high system throughputs can be attained. Up to four process chambers can be accommodated on the SiNergy Centura platform.
Sl no | Topic |
1 | Market Segmentation |
2 | Scope of the report |
3 | Abbreviations |
4 | Research Methodology |
5 | Executive Summary |
6 | Introduction |
7 | Insights from Industry stakeholders |
8 | Cost breakdown of Product by sub-components and average profit margin |
9 | Disruptive innovation in the Industry |
10 | Technology trends in the Industry |
11 | Consumer trends in the industry |
12 | Recent Production Milestones |
13 | Component Manufacturing in US, EU and China |
14 | COVID-19 impact on overall market |
15 | COVID-19 impact on Production of components |
16 | COVID-19 impact on Point of sale |
17 | Market Segmentation, Dynamics and Forecast by Geography, 2024-2030 |
18 | Market Segmentation, Dynamics and Forecast by Product Type, 2024-2030 |
19 | Market Segmentation, Dynamics and Forecast by Application, 2024-2030 |
20 | Market Segmentation, Dynamics and Forecast by End use, 2024-2030 |
21 | Product installation rate by OEM, 2023 |
22 | Incline/Decline in Average B-2-B selling price in past 5 years |
23 | Competition from substitute products |
24 | Gross margin and average profitability of suppliers |
25 | New product development in past 12 months |
26 | M&A in past 12 months |
27 | Growth strategy of leading players |
28 | Market share of vendors, 2023 |
29 | Company Profiles |
30 | Unmet needs and opportunity for new suppliers |
31 | Conclusion |
32 | Appendix |