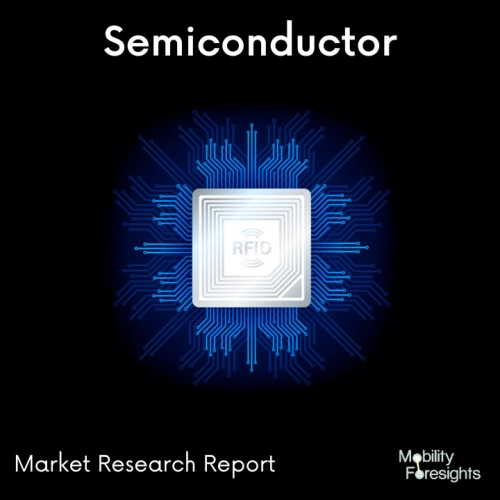
- Get in Touch with Us
Last Updated: Apr 25, 2025 | Study Period: 2023-2030
However, because of the simplicity with which digital signals can be generated and transferred, technology is moving more towards the digital side. A sensor is used to transform physical qualities from one field to another in order to bridge the gap between these two domains.
Almost everyone today has a set of microphones, speakers, and cameras, thanks to the recent emergence of work-from-home culture. While their functions differ, these gadgets are nothing more than sensors that have become an integral part of our lives and have had a tremendous influence on us.
Sensors, also known as transducers, enable them to interact with the environment around via an electrical or mechanical instrument. The technology measures or detects some environmental property or changes to that property over time.
Sensor technology has advanced rapidly since the late 1800s, when one of the earliest temperature sensors based on a copper resistor was produced. Nowadays, if I look around, 'll notice vario types of sensors everywhere. Smartphones, computers, automobiles, microwave ovens â name it, and it most likely contains at least one sensor.
Sensors are classified into two groups based on the sort of characteristic they record. Exteroceptive sensors collect data about the world outside the system in which they are present. Extero means from the outside, and popular examples include cameras, LiDAR, radar, and ultrasonic/sonar sensors. In contrast, a sensor is proprioceptive if it collects data about the system itself.
Proprios refers to internal or personal, and popular examples are GPS, inertial measurement units (IMU), and position sensors. Sensors are also classified as digital or analogue depending on the sort of output they offer.
Sensors may be utilized in almost every situation. According to The Electrochemical Society, sensors can improve the world through diagnostics in medical applications; improved performance of energy sources such as fuel cells, batteries, and solar power; improved health, safety, and security for people; sensors for exploring space and the known universe; and improved environmental monitoring. Let's have a look at some of the applications where sensors come in handy.
Sensing technologies have become an integral aspect of the production process as the Fourth Industrial Revolution (Industry 4.0) continues. Sensors allow enterprises to monitor, regulate, and automate processes while also increasing safety.
Sensors provide several benefits in production, including increased operational efficiency, better asset management, and more responsive product development.These are some of the most often encountered in the industrial business.
A temperature sensor is an important component because it monitors temperature changes and helps to monitor and manage heat flow in the process. These sensors assist by providing freeze protection in water lines by continually tracking the heat provided to the pipes or by restricting the heat created in loaded electrical equipment, which may be dangerous if not monitored, both for the device and humans.
These are some of the most often encountered in the industrial business. A temperature sensor is an important component because it monitors temperature changes and helps to monitor and manage heat flow in the process.
These sensors assist by providing freeze protection in water lines by continually tracking the heat provided to the pipes or by restricting the heat created in loaded electrical equipment, which may be dangerous if not monitored, both for the device and humans.
An inertial measurement unit (IMU) is an electronic device that uses a combination of accelerometers, gyroscopes, and magnetometers to detect and report a body's particular force, angular rate, and occasionally direction.
IMUs are referred to as IMMUs when a magnetometer is integrated. IMUs are commonly employed to control contemporary vehicles such as motorbikes, missiles, airplanes (an attitude and heading reference system), including unmanned aerial vehicles (UAVs), and spacecraft such as satellites and landers.
Recent advancements enable the manufacture of IMU-enabled GPS systems. When GPS signals are absent, such as in tunnels, within buildings, or when there is electrical interference, an IMU allows a GPS receiver to function.
An inertial measuring device detects linear acceleration using one or more sensors.A magnetometer, which is widely used as a heading reference, is also included in some. For each of the three primary axes: pitch, roll, and yaw, typical setups include one accelerometer, gyro, and magnetometer.
Inertial Navigation Systems (INS) frequently use IMU readings to determine attitude, angular rates, linear velocity, and location relative to a global reference frame. Many commercial and military vehicles, including crewed airplanes, missiles, ships, submarines, and satellites, rely on IMU-equipped INS for navigation and control.
IMUs are also critical components in the navigation and control of unmanned systems like UAVs, UGVs, and UUVs. Attitude and Heading Reference Systems are simpler variants of INSs that use IMUs to compute vehicle attitude.
In land vehicles, an IMU can be integrated into GPS-based automotive navigation systems or vehicle tracking systems, providing the system with dead reckoning capability and the ability to collect as much accurate data about the vehicle's current speed, turn rate, heading, inclination, and acceleration as possible, in conjunction with the vehicle's wheel speed sensor output and, if available, reverse gear signal, for purposes such as better traffic collision analysis.
In addition to navigation, IMUs are used as orientation sensors in numerous consumer items. As orientation sensors, IMUs are found in almost all smartphones and tablets.
IMUs may be used in fitness trackers and other wearables to quantify motion, such as jogging. IMUs may also evaluate an individual's developmental level while in motion by identifying specificity.
The Global Programmable Inertial Measurement Unit (IMU) Market accounted for $XX Billion in 2022 and is anticipated to reach $XX Billion by 2030, registering a CAGR of XX% from 2023 to 2030.
The IMU330RA high performance inertial measurement unit (IMU) has been made generally available by ANTENNA.The new IMU330RA from VIENNA is an easy-to-integrate, high-performance 6-DOF inertial sensor housed in an IP69K-rated ruggedized, sealed over-molded plastic container.
The IMU330RA includes redundant 3-Axis Accelerometer and 3-Axis Rate Gyroscope sensors for high accuracy and dependability.The module supports both 1000Base-T1 Automotive Ethernet and CAN-FD interfaces and offers an update rate of up to 1000 Hz with low latency.
The IMU330RA is an automotive grade, ASIL B certified device that serves as the foundation for ASIL D customer positioning system integration.
Sl no | Topic |
1 | Market Segmentation |
2 | Scope of the report |
3 | Abbreviations |
4 | Research Methodology |
5 | Executive Summary |
6 | Introduction |
7 | Insights from Industry stakeholders |
8 | Cost breakdown of Product by sub-components and average profit margin |
9 | Disruptive innovation in the Industry |
10 | Technology trends in the Industry |
11 | Consumer trends in the industry |
12 | Recent Production Milestones |
13 | Component Manufacturing in US, EU and China |
14 | COVID-19 impact on overall market |
15 | COVID-19 impact on Production of components |
16 | COVID-19 impact on Point of sale |
17 | Market Segmentation, Dynamics and Forecast by Geography, 2023-2030 |
18 | Market Segmentation, Dynamics and Forecast by Product Type, 2023-2030 |
19 | Market Segmentation, Dynamics and Forecast by Application, 2023-2030 |
20 | Market Segmentation, Dynamics and Forecast by End use, 2023-2030 |
21 | Product installation rate by OEM, 2023 |
22 | Incline/Decline in Average B-2-B selling price in past 5 years |
23 | Competition from substitute products |
24 | Gross margin and average profitability of suppliers |
25 | New product development in past 12 months |
26 | M&A in past 12 months |
27 | Growth strategy of leading players |
28 | Market share of vendors, 2023 |
29 | Company Profiles |
30 | Unmet needs and opportunity for new suppliers |
31 | Conclusion |
32 | Appendix |