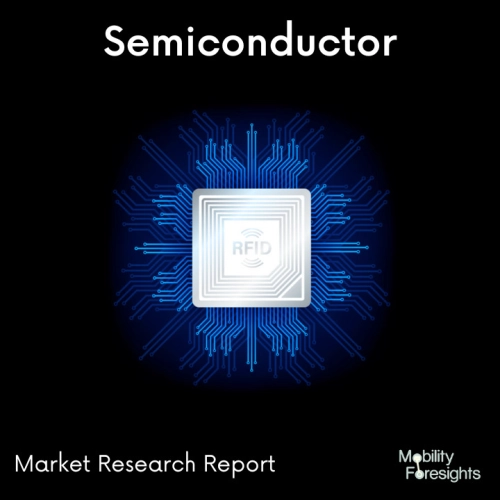
- Get in Touch with Us
Last Updated: Apr 25, 2025 | Study Period: 2024-2030
A device known as an LVDT (linear variable differential transformer) detects displacement caused by mechanical linear movement and transforms it into electrical signals. This method's contact displacement sensors read changes in the target's form by translating them into electrical impulses. An LVDT is a type of electromechanical device that transforms mechanical motion or vibrationsâmore especially, rectilinear motionâinto a changeable electrical current, voltage, or electric signals, as well as the opposite.
Automated control systems and measuring technologies both use actuating mechanisms as mechanical motion sensors. Electromechanical transducers can be categorized based on their output signal kinds or conversion principles. For simple signal conditioning, a linear transducer delivers voltage output quantity related to the parameters being measured, such as force. Devices that use LVDT sensors are susceptible to electromagnetic interference.
The elimination of large errors can be enhanced by using shorter connection cables to reduce electrical resistance. Three to four connecting cables are needed for the power supply and output signal transmission of a linear displacement transducer. Physically, an LVDT is made of a hollow metallic cylinder along which a shaft with a lower diameter freely swings back and forth. When the device is in operation, the shaft, or pushrod, ends in a magnetically conducting core that must be inside the cylinder, or coil assembly.
S No | Product Name | Development |
1 | NewTek LVDT Displacement Sensors | LVDT Displacement NewTek The seismic vibrator trucks have sensors installed to give feedback on the location of the baseplate that strikes the ground and emits the vibrations required for seismic surveys. Controlling the vibrations released into the earth that can change in frequency to detect different ground features requires knowledge of the base plate's position. |
2 | LS-LVDT | Ideal for linear control and precise measurement applications is the LS-LVDT. These sensors have the best stroke-to-length ratios and the longest available stroke. A smooth static and dynamic response is provided by precision-machined components. Optimize for a high bandwidth/response rate or resolution with no temperature drift by combining with a MicroStrain signal conditioner. |
It is also confirmed by position feedback whether the baseplate is in the deployed or storage position.On the vibroseis trucks, NewTek Economical Model R-812 Series LVDTs perform consistently. These AC-operated sensors are designed without sensitive electronic components that are frequently impacted by stress and vibration.With electronics situated in safe locations but remotely located, the sensor can operate in dangerous conditions.
Alloys that are resistant to corrosion offer structural stability and permit submersion of the device.For linear control and precise measurement applications, the small LS-LVDT offers quick response and durable packaging. Sub-micron precision, linear analog output, flat dynamic response to kHz levels, and extremely low temperature coefficients are just a few of the cutting-edge characteristics offered by configuration options.
The core of the free sliding transducer is robust, lightweight, and corrosion-proof. To achieve a snug sliding fit inside the open bore of the stainless steel lined LS-LVDT body, cores are precision ground.The LS-LVDT can achieve incredibly high repeatability thanks to this precision. The detecting head is water-resistant and may be fully submerged. Sensonics extensive selection of standard LVDT displacement transducers may not always satisfy the demands of particular applications, in which case highly effective bespoke design service is suitable.
Sensonics has the technological know-how to provide a cost-effective solution, whether it is for a new application, replacing an outdated product, or because your current provider is unable to satisfy your needs.LVDTs can be applied in a wide variety of situations. Examples include the measurement of the casing and cylinder expansion on steam turbines, valve position monitoring, crack monitoring on important buildings, tunnels, and bridges, and actuator controls that provide feedback on the position of the actuator either alongside or for high-pressure designs for OEM internal mounting.
Additionally, custom designs for more specialized uses include submersible, underwater, and radiation-proof. An LVDT works on the electromechanical premise that it generates an electrical signal whose amplitude is inversely proportional to the displacement of the transducer core.On a cylindrical former, three coilsâa primary coil, two secondary coilsâare arranged symmetrically. The electrical circuit is set up with the secondary coils in series opposition, and a magnetic core inside the coil assembly provides a channel for the magnetic flux connecting the coils.
By keeping track of the performance precision of actuators and cylinders to increase operational efficiencies, LVDTs give position feedback in hydraulic applications.In most hydraulic applications, the function of the cylinder is to move an object, such as a valve, an airplane tail rudder, a boom, or a shovel on an off-road vehicle.The control system in these applications needs a feedback device to inform it of how far the cylinder or actuator moved.
For instance, a pilot would move the joystick to maneuver the aircraft. When the joystick is moved, the plane's control system detects it and signals the tail rudder actuator to move the tail rudder.The plane could turn too much or too little if the system has no way of determining how far the actuator has moved. A robotic arm picking up a piece of glass is another illustration. Based on position feedback from an LVDT, if the control system does not know when to halt the arm, the hydraulic cylinder can force the arm straight through the piece of glass.
The Global LVDT Displacement Sensors Market accounted for $XX Billion in 2023 and is anticipated to reach $XX Billion by 2030, registering a CAGR of XX% from 2024 to 2030.
Micro-Epsilon eddy current sensors are intended for non-contact measurement of displacement, distance, position, oscillation, and vibration. They are especially well-suited for high accuracy in severe industrial conditions (pressure, filth, temperature). Micro-Epsilon capacitive sensors perform high-precision non-contact measurements of displacement, distance, and position of electrically conductive objects. OptoNCDT sensors have established new benchmarks for industrial laser displacement measurement.
Micro-Epsilon laser sensors are among the finest in their class for measuring displacement, distance, and thickness. These laser sensors are employed in measuring and monitoring jobs in industrial automation, electronics manufacturing, robotics, and vehicle building, among other things. The confocal chromatic confocalDT measuring device is used to quickly measure distance and thickness. Different sensor kinds and controller interfaces enable a wide range of applications.
LVDT displacement sensors are used in a wide range of industries, including automotive, aerospace, industrial automation, and medical and healthcare. The increasing demand from these industries is expected to drive the growth of the LVDT displacement sensor market. The increasing demand for high-precision and reliable displacement measurement solutions is another factor driving the growth of the LVDT displacement sensor market. LVDT displacement sensors are known for their high accuracy and reliability, making them ideal for a wide range of applications.
The growing adoption of automation and robotics in various industries is also driving the demand for LVDT displacement sensors. LVDT displacement sensors are used in a variety of automation and robotics applications, such as machine tool control, robot navigation, and process control. Ongoing advancements in sensor technology, including improvements in materials, design, and signal processing capabilities, were enhancing the performance and reliability of LVDT displacement sensors. This, in turn, was expanding their application areas.
There was an increasing emphasis on developing LVDT sensors that are resistant to harsh environmental conditions, such as extreme temperatures, vibrations, and corrosive substances. This was particularly important for applications in sectors like oil and gas, automotive, and marine.
Micro-Epsilon eddy current sensors are intended for non-contact measurement of displacement, distance, position, oscillation, and vibration. They are especially well-suited for high accuracy in severe industrial conditions (pressure, filth, temperature). Micro-Epsilon capacitive sensors perform high-precision non-contact measurements of displacement, distance, and position of electrically conductive objects.
OptoNCDT sensors have established new benchmarks for industrial laser displacement measurement.Micro-Epsilon laser sensors are among the finest in their class for measuring displacement, distance, and thickness. These laser sensors are employed in measuring and monitoring jobs in industrial automation, electronics manufacturing, robotics, and vehicle building, among other things.
The confocal chromatic confocalDT measuring device is used to quickly measure distance and thickness. Different sensor kinds and controller interfaces enable a wide range of applications.
Sl no | Topic |
1 | Market Segmentation |
2 | Research Methodology |
3 | Executive Summary |
4 | Potential Opportunities for Client in LVDT Displacement Sensor Market |
5 | Average B-2-B Price of LVDT Displacement Sensor, By Geography |
6 | Overview of Technology of LVDT Displacement Sensor |
7 | Global LVDT Displacement Sensor Market Manufacturing Footprint - 2023 |
8 | Major Drivers For LVDT Displacement Sensor Market |
New Product Development in LVDT Displacement Sensor Market | |
10 | Automation adoption in industries and its effects on LVDT Displacement Sensor |
11 | New LVDT Displacement Sensor in the market & their Specifications |
12 | Hardware Research Areas for LVDT Displacement Sensor |
13 | Overview of Industry 4.0 and effect on LVDT Displacement Sensor Market |
14 | Market Size, Dynamics, And Forecast By Geography, 2024-2030 |
15 | Market Size, Dynamics, And Forecast By end user, 2024-2030 |
16 | Market Size, Dynamics, And Forecast By Product, 2024-2030 |
17 | Market Size, Dynamics, And Forecast By Type, 2024-2030 |
18 | Competitive Landscape |
19 | Market Share Of Major Players-2023 |
20 | Growth Strategy of Major Player |
21 | Merger & Acquisitions |
22 | Company Profile |
23 | Conclusion |