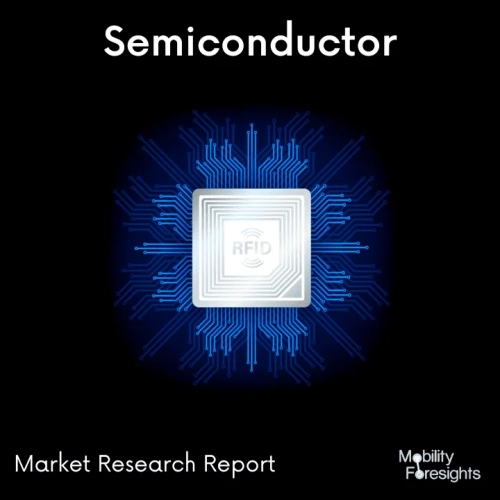
- Get in Touch with Us
Last Updated: Apr 25, 2025 | Study Period:
Small parts called magnetoresistive sensors are used to detect an applied magnetic field.
The sensor can function across a sizable air gap because no electrical contact is necessary.
Magnetoresistive sensors are made to be compact and power-efficient in order to enable embedding.
An applied magnetic field can alter an electrical conductor's resistance, which is how the magnetoresistive effect works.
When in close proximity to a magnetic field, magneto resistive materials undergo size and form changes. By observing these variations, a magneto resistive position sensor can determine the object's location.
A position magnet must first be attached to the object to be measured in order to accomplish this. A magneto resistive wire carrying an electric current generates a second magnetic field that interacts with the magnetic field cast by this magnet.
The magneto resistive position sensor at the end of the wire picks up a sound pulse that is produced by the interaction of the two magnetic fields. The location of the object and its attached position magnet is determined by the interval between the current and the pulse.
The Global Magnetoresistive Position Sensor market accounted for $XX Billion in 2021 and is anticipated to reach $XX Billion by 2030, registering a CAGR of XX% from 2022 to 2030.
The Magnetoresistive (MR) Sensor ICs from Honeywell's Nanopower Series are ultra-sensitive components created to support a variety of applications with huge air gaps, weak magnetic fields, and low power needs.
The North or South poles applied in a direction parallel to the sensor cause the sensor ICs to respond.
They simplify installation and might save system costs because the magnet polarity does not need to be known. They have a push-pull output that does not require a pull-up resistor and a very low average current usage.
To increase energy efficiency, the sensor ICs can function with a supply voltage as low as 1.65 V.
Sl no | Topic |
1 | Market Segmentation |
2 | Scope of the report |
3 | Abbreviations |
4 | Research Methodology |
5 | Executive Summary |
6 | Introduction |
7 | Insights from Industry stakeholders |
8 | Cost breakdown of Product by sub-components and average profit margin |
9 | Disruptive innovation in the Industry |
10 | Technology trends in the Industry |
11 | Consumer trends in the industry |
12 | Recent Production Milestones |
13 | Component Manufacturing in US, EU and China |
14 | COVID-19 impact on overall market |
15 | COVID-19 impact on Production of components |
16 | COVID-19 impact on Point of sale |
17 | Market Segmentation, Dynamics and Forecast by Geography, 2022-2030 |
18 | Market Segmentation, Dynamics and Forecast by Product Type, 2022-2030 |
19 | Market Segmentation, Dynamics and Forecast by Application, 2022-2030 |
20 | Market Segmentation, Dynamics and Forecast by End use, 2022-2030 |
21 | Product installation rate by OEM, 2022 |
22 | Incline/Decline in Average B-2-B selling price in past 5 years |
23 | Competition from substitute products |
24 | Gross margin and average profitability of suppliers |
25 | New product development in past 12 months |
26 | M&A in past 12 months |
27 | Growth strategy of leading players |
28 | Market share of vendors, 2022 |
29 | Company Profiles |
30 | Unmet needs and opportunity for new suppliers |
31 | Conclusion |
32 | Appendix |