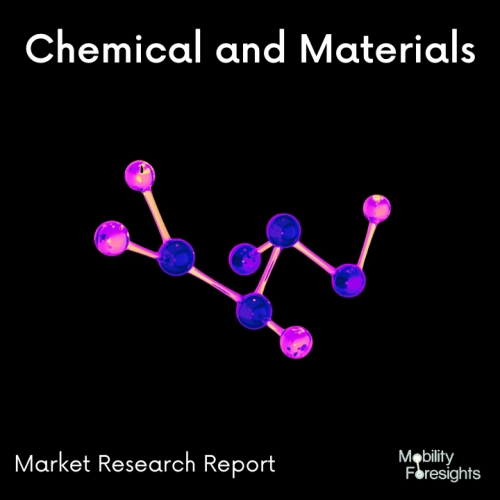
- Get in Touch with Us
Last Updated: Apr 25, 2025 | Study Period: 2024-2030
Epoxy resins and coal tar make up coal tar epoxy. It is a kind of polymer that is applied to surfaces to coat them and shield them from corrosive conditions.
In harsh environments like industrial and offshore activities, where chemicals, seawater, and other elements might cause corrosion, it is usually utilised on metal and concrete. Due to its potent moisture-blocking abilities, coal tar epoxy can provide corrosion prevention.
Because of its affordability and simplicity of usage, this kind of epoxy is frequently utilised, but the same may be true of other resin substrates. Many of the other substrates don't have the same risks to the environment and human health that coal tar does.
The presence of coal tar pitch and its polycyclic aromatic hydrocarbons in coal tar epoxy makes it dangerous (PAH). This coal tar byproduct has been handled by numerous protection agencies. Exposure to PAH, a recognised carcinogen, can happen through the air or through skin contact. The production of coal tar pitch also results in the discharge of volatiles that pollute the air.
Additionally, coal tar epoxy poses a serious fire risk. It produces hazardous vapours when a fire is burning and needs particular extinguishing materials.
Global marine coal tar epoxy coating market accounted for $XX Billion in 2023 and is anticipated to reach $XX Billion by 2030, registering a CAGR of XX% from 2024 to 2030.
At Chemco, they have created a protective coating technique that is compatible with the coal-tar epoxies often used in ballast tanks and may be used as a repair or patch repair solution.
Coal-tar epoxies are a particularly challenging region for many businesses to repair or fix. Solvent-based paints cannot be utilised for this type of project because the solvent in these materials will attack the bitumen in the coal-tar epoxy and melt away the coating. Therefore, to perform this kind of repair job, solvent-free chemicals must be utilised.
Any surface preparation technique can be used, based on convenience and client acceptability (water jetting, mechanical preparation or grit blasting). Due to this system's wet & rust-tolerant characteristics, the two coat system could then be applied as soon as the surface preparation was finished.
The adaptability of surface preparation techniques for repair work has the added benefit of negating the necessity for grit blasting. The client would save a lot of money and time by doing away with this labor-intensive and expensive procedure.
Sl no | Topic |
1 | Market Segmentation |
2 | Scope of the report |
3 | Abbreviations |
4 | Research Methodology |
5 | Executive Summary |
6 | Introduction |
7 | Insights from Industry stakeholders |
8 | Cost breakdown of Product by sub-components and average profit margin |
9 | Disruptive innovation in the Industry |
10 | Technology trends in the Industry |
11 | Consumer trends in the industry |
12 | Recent Production Milestones |
13 | Component Manufacturing in US, EU and China |
14 | COVID-19 impact on overall market |
15 | COVID-19 impact on Production of components |
16 | COVID-19 impact on Point of sale |
17 | Market Segmentation, Dynamics and Forecast by Geography, 2024-2030 |
18 | Market Segmentation, Dynamics and Forecast by Product Type, 2024-2030 |
19 | Market Segmentation, Dynamics and Forecast by Application, 2024-2030 |
20 | Market Segmentation, Dynamics and Forecast by End use, 2024-2030 |
21 | Product installation rate by OEM, 2023 |
22 | Incline/Decline in Average B-2-B selling price in past 5 years |
23 | Competition from substitute products |
24 | Gross margin and average profitability of suppliers |
25 | New product development in past 12 months |
26 | M&A in past 12 months |
27 | Growth strategy of leading players |
28 | Market share of vendors, 2023 |
29 | Company Profiles |
30 | Unmet needs and opportunity for new suppliers |
31 | Conclusion |
32 | Appendix |