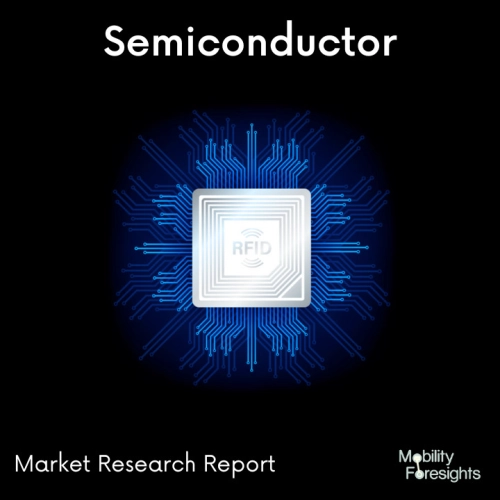
- Get in Touch with Us
Last Updated: Apr 25, 2025 | Study Period: 2023-2030
Maskless lithography is a revolutionary new type of lithography system that executes exposure and patterning processes without the need for a photomask. This technology enables very high resolution, high throughput and low cost production of integrated circuits and other micro-patterned components.
The basic concept behind maskless lithography is to use a digital light source to expose the desired pattern onto a substrate. The digital light source can be a laser, an array of LEDs, or an array of digital mirrors. The light source is used to project a digital pattern onto the substrate, which is then exposed using photoresist.
The advantages of using maskless lithography over traditional photomask-based lithography are many. For one, since no physical mask is required, patterning costs are significantly reduced.
Additionally, since the digital light source can be used to quickly switch between patterns, it is possible to quickly create complex patterns with high resolution and accuracy. Finally, since the digital light source can be used to expose multiple layers simultaneously, the throughput of the process is greatly increased.
The main disadvantage of maskless lithography is that the process is more complex and requires more equipment than traditional photomask-based lithography. However, with the right combination of digital light source, optics and photoresist, the advantages can outweigh the disadvantages and make maskless lithography a viable option for fabricating high-quality micro-patterned components.
The Global Maskless Lithography System market accounted for $XX Billion in 2022 and is anticipated to reach $XX Billion by 2030, registering a CAGR of XX% from 2023 to 2030.
Microlight3D, a specialized maker of high-resolution micro-scale 2D and 3D printing systems for scientific and industrial uses, introduces Smart Print-UV (SP-UV), a revolutionary UV light-powered maskless lithography technology.
With its new 385 nm LED source, SP-UV may now be used with the most popular photoresists, such as SU-8, which is essential for applications involving microfluidics.
More options are now available to developers for photoresist materials used in semiconductor fabrication. SP-UV's optical projection technology is a major benefit. This blends writing accuracy with speed and provides users with four alternative writing resolutions. Microlight3D's "quick release" objective system allows resolution changes to be made in as little as two seconds.
By improving the system's compatibility with a greater variety of photoresist materials, Microlight3D's SP-UV is expanding the possibilities of maskless lithography while meeting the objectives of developers seeking affordability and versatility.
They are facilitating the fabrication of large-scale structures with micrometric precision for researchers working in optoelectronics, MEMS, spintronics, and lab-on-a-chip more quickly and easily. Since the SP-UV system is well integrated to enhance the user experience, they anticipate that it will lead to new market prospects in microfluidics and small series production across several industries.
EV Group's New Maskless Exposure Technology Revolutionizes Lithography. When compared to current high-volume manufacturing lithography techniques, EVG's revolutionary MLE technology offers unparalleled flexibility, scalability, and cost-of-ownership advantages.
The innovative next-generation lithography technology known as MLE (Maskless Exposure) was unveiled by EV Group (EVG), a top provider of wafer bonding and lithography equipment for the MEMS, nanotechnology, and semiconductor markets.
MLE was created to meet the back-end lithography requirements of advanced packaging, MEMS, biomedical, and high-density printed circuit board applications. MLE is the first highly scalable maskless lithography technology for high-volume manufacturing in the world.
It eliminates the significant overhead costs associated with photomasks, such as mask management and maintenance infrastructure, while combining high-resolution patterning with high throughput and yield. MLE also offers unparalleled versatility, enabling incredibly quick development cycles for new products.
Sl no | Topic |
1 | Market Segmentation |
2 | Scope of the report |
3 | Abbreviations |
4 | Research Methodology |
5 | Executive Summary |
6 | Introdauction |
7 | Insights from Industry stakeholders |
8 | Cost breakdown of Product by sub-components and average profit margin |
9 | Disruptive innovation in theIndustry |
10 | Technology trends in the Industry |
11 | Consumer trends in the industry |
12 | Recent Production Milestones |
13 | Component Manufacturing in US, EU and China |
14 | COVID-19 impact on overall market |
15 | COVID-19 impact on Production of components |
16 | COVID-19 impact on Point of sale |
17 | Market Segmentation, Dynamics and Forecast by Geography, 2023-2030 |
18 | Market Segmentation, Dynamics and Forecast by Product Type, 2023-2030 |
19 | Market Segmentation, Dynamics and Forecast by Application, 2023-2030 |
20 | Market Segmentation, Dynamics and Forecast by End use, 2023-2030 |
21 | Product installation rate by OEM, 2023 |
22 | Incline/Decline in Average B-2-B selling price in past 5 years |
23 | Competition from substitute products |
24 | Gross margin and average profitability of suppliers |
25 | New product development in past 12 months |
26 | M&A in past 12 months |
27 | Growth strategy of leading players |
28 | Market share of vendors, 2023 |
29 | Company Profiles |
30 | Unmet needs and opportunity for new suppliers |
31 | Conclusion |
32 | Appendix |