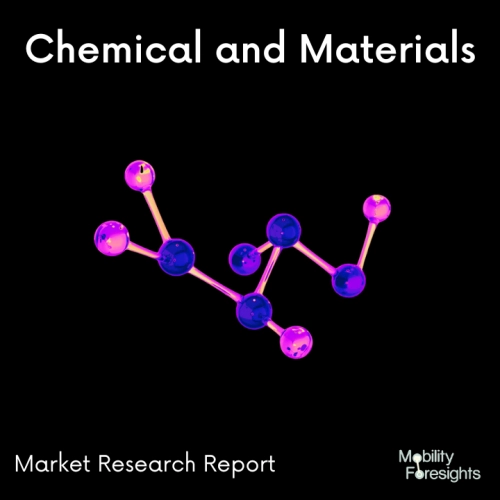
- Get in Touch with Us
Last Updated: Apr 25, 2025 | Study Period: 2024-2030
Master Alloys are frequently employed in the metallurgy of non-ferrous metals as a deoxidants, degasifiers, desulphurizing agent, or in other capacities as additives in the production of other alloys. Depending on the application, a Master Alloy may be referred to as a hardener, grain refiner, or modifier.
Selective composition adjustment is one of numerous justifications for introducing a Master Alloy to a melt. They are used to alter the molten metal's chemical composition so that it can obtain the desired chemical specification. Specific performance needs are a second significant use..
Modifiable characteristics include castability and surface. In order to alter a metal's characteristics, master alloys can alter the microstructure of the metal during casting and solidification. Castability, surface polish, electrical conductivity, mechanical strength, and ductility are among the properties that can be changed.
Due to certain elements' poor yield or large losses when melted in pure form, using a Master Alloy rather than a pure metal may be more cost-effective. Technical difficulties or the needed furnace temperature being too high for basic casting operations equipment may also hinder the pure metals from dissolving fully.
By dissolving more quickly at lower temperatures while conserving critical time and energy, our Master Alloys offer the solution.
The Global master alloy market accounted for $XX Billion in 2023 and is anticipated to reach $XX Billion by 2030, registering a CAGR of XX% from 2024 to 2030.
Belmont Aluminum Master Alloys are alloying components made from aluminium that are mixed in high concentrations with one or more other elements. With the help of our alloys, casting businesses and ingot producers may avoid any alloying issues they could run into while working with molten metals.
A practical and affordable technique to add hardener elements to aluminium to obtain desired qualities is through master alloys made of aluminium that contain the hardener elements in high concentrations.
These master alloys easily dissolve at lower liquid aluminium temperatures, reducing hydrogen solubility and dross formation. Lower furnace temperatures also result in less energy being used and a longer lifespan for the furnace.
RUSAL starts production of master alloys for high-tech alloys.At the Aluminium Smelter in Krasnoyarsk, the new production is started. funding for the project. Over 5,000 tonnes of melted master alloys may be produced at the plant each year.
The smelters of RUSAL are the majority of the new production's consumers. The largest Russian metal manufacturers are external clientele. The main user of master alloys in Russia is RUSAL.
A master alloy is an alloy of two or more components intended for mixing with liquid metal to add high-melting elements. In order to produce alloys with the appropriate qualities, master alloys must have a precise chemical composition.
Aluminium-scandium master alloy, for instance, is used to create alloys for shipbuilding. For use in the electrical sector, with zirconium. Strontium master alloys are used to modify casting alloys.
RUSAL Engineering and Technology Centre employees have been working on the master alloy manufacturing project. The project began with the development of a technique for producing aluminium-scandium master alloys, the most technologically challenging of melted master alloys.
A one-of-a-kind, unrivalled technology was created, and Russian and international patents were gained. RUSAL began commercial batch manufacturing of aluminium-scandium master alloys and now leads the industry in both production and sales of this kind of master alloy.
The following stage of development was the development of technology for producing different types of master alloys. Master alloys containing strontium, manganese, titanium, nickel, iron, cobalt, and rare earth elements are among them.
Sl no | Topic |
1 | Market Segmentation |
2 | Scope of the report |
3 | Abbreviations |
4 | Research Methodology |
5 | Executive Summary |
6 | Introduction |
7 | Insights from Industry stakeholders |
8 | Cost breakdown of Product by sub-components and average profit margin |
9 | Disruptive innovation in the Industry |
10 | Technology trends in the Industry |
11 | Consumer trends in the industry |
12 | Recent Production Milestones |
13 | Component Manufacturing in US, EU and China |
14 | COVID-19 impact on overall market |
15 | COVID-19 impact on Production of components |
16 | COVID-19 impact on Point of sale |
17 | Market Segmentation, Dynamics and Forecast by Geography, 2024-2030 |
18 | Market Segmentation, Dynamics and Forecast by Product Type, 2024-2030 |
19 | Market Segmentation, Dynamics and Forecast by Application, 2024-2030 |
20 | Market Segmentation, Dynamics and Forecast by End use, 2024-2030 |
21 | Product installation rate by OEM, 2023 |
22 | Incline/Decline in Average B-2-B selling price in past 5 years |
23 | Competition from substitute products |
24 | Gross margin and average profitability of suppliers |
25 | New product development in past 12 months |
26 | M&A in past 12 months |
27 | Growth strategy of leading players |
28 | Market share of vendors, 2023 |
29 | Company Profiles |
30 | Unmet needs and opportunity for new suppliers |
31 | Conclusion |
32 | Appendix |