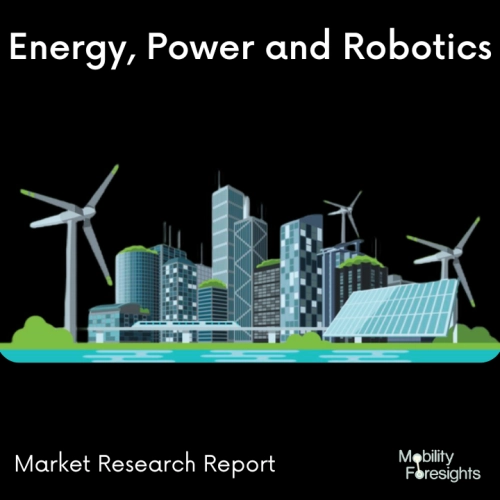
- Get in Touch with Us
Last Updated: Apr 25, 2025 | Study Period: 2023-2030
The robot's basic capacity to move things is used for material handling (MH). Robots may carry products from one place to another with efficiency and accuracy by equipping them with the proper end-of-arm tools.
handling of materials includes moving raw materials from their original location to the place of use in manufacturing, manipulating them as a result in the production process, and moving finished products from factories and distributing them to customers or sales outlets. handling of materials.
Robotic applications that include material transfer call for the robot to transport supplies or components from one place to another. Numerous of these jobs call for robots to pick up components from one conveyor and place them on another.
In the industrial sector robotic material handling and tending systems are prevalent. Robotic arms transferring production parts typically on or off a conveyor belt or to hold a part in place for manufactureâare referred to as material handling.
The Global Material Handling Robotics market accounted for $XX Billion in 2022 and is anticipated to reach $XX Billion by 2030, registering a CAGR of XX% from 2023 to 2030.
ABB has introduced robots that can handle materials more quickly and adaptably during the production of EV batteries. The robot can increase production and performance with increased uptime because to its improved speed and precision and durable architecture.
The two robot families are capable of performing a variety of production tasks, such as assembly, machine tending, and material handling. Additionally, it can carry out EV-specific tasks including picking and inserting battery modules, handling parts, and precise assembly.
It is powered by ABB's OmniCore controller, which enables the robots to move more quickly, increasing production capacity and cutting down on manufacturing times.
LeanID Integrated DressPack from ABB offers extra defence against harm and cable deterioration. In this scenario, the process cables are wound around the robot's wrist and into its upper arm. As a result, concerns about swinging cables are removed, and heat and collisions are protected while downtime and maintenance costs are reduced.
The service life of the robots may be extended by several years as a result. Both robot ranges offer a variety of mounting options, including inclined, floor, inverted, and semi-shelf, for the most production design freedom.
Sl no | Topic |
1 | Market Segmentation |
2 | Scope of the report |
3 | Abbreviations |
4 | Research Methodology |
5 | Executive Summary |
6 | Introduction |
7 | Insights from Industry stakeholders |
8 | Cost breakdown of Product by sub-components and average profit margin |
9 | Disruptive innovation in the Industry |
10 | Technology trends in the Industry |
11 | Consumer trends in the industry |
12 | Recent Production Milestones |
13 | Component Manufacturing in US, EU and China |
14 | COVID-19 impact on overall market |
15 | COVID-19 impact on Production of components |
16 | COVID-19 impact on Point of sale |
17 | Market Segmentation, Dynamics and Forecast by Geography, 2023-2030 |
18 | Market Segmentation, Dynamics and Forecast by Product Type, 2023-2030 |
19 | Market Segmentation, Dynamics and Forecast by Application, 2023-2030 |
20 | Market Segmentation, Dynamics and Forecast by End use, 2023-2030 |
21 | Product installation rate by OEM, 2023 |
22 | Incline/Decline in Average B-2-B selling price in past 5 years |
23 | Competition from substitute products |
24 | Gross margin and average profitability of suppliers |
25 | New product development in past 12 months |
26 | M&A in past 12 months |
27 | Growth strategy of leading players |
28 | Market share of vendors, 2022 |
29 | Company Profiles |
30 | Unmet needs and opportunity for new suppliers |
31 | Conclusion |
32 | Appendix |