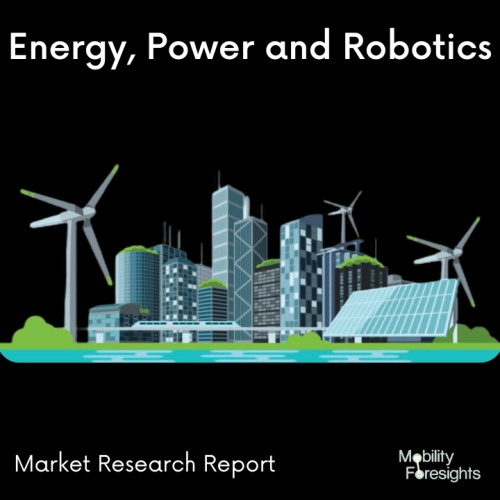
- Get in Touch with Us
Last Updated: Apr 25, 2025 | Study Period: 2023-2030
Cutting automotive headliner materials, removing flash from plastic mouldings, and polishing moulds and stamping dies are all tasks carried out by robots. Utilising robotic automation solutions for material removal can help you boost output, lessen team stress and injuries, and boost long-term ROI.
The robotic trimming system follows a path that produces more uniformity than even the most competent operator, resulting in less variation in the quality of components produced by various dies.Robotic material removal need not entail holding the object.
Robots include articulated robots, humanoids, cobots, autonomous mobile robots (AMRs), automated guided vehicles (AGVs), and hybrids. In numerous industries, robots are utilised to increase productivity, quicken procedures, increase safety, and improve customer experiences.
The Global Material Removal Robots market accounted for $XX Billion in 2022 and is anticipated to reach $XX Billion by 2030, registering a CAGR of XX% from 2023 to 2030.
Robots used for material removal travel the globe and make conclusions very instantly. They are able to absorb information about their surroundings with the aid of technologies like sensors and cameras.
Whether they are moving to escape an approaching employee, picking the ideal parcel, or choosing the best surface to disinfect, onboard processing equipment enables them to assess it and make an intelligent decision.
They are mobile solutions that work with little assistance from people. Applications for automated material removal include cutting, polishing, trimming, and deburring, to name a few.
The motion and positioning requirements, tool wear inaccuracy, and force control make these procedures difficult. In order to address many of the problems with material removal applications, Kawasaki has created software choices.
To apply the proper amount of force between the workpiece and the material removal equipment, Kawasaki offers feedback control. In order to address a range of motion limitations during the material removal process, motion cooperation between multi-axis positioners and the robot is also provided.
If you need specialised material removal solutions, Kawasaki can deliver them. Standard choices for interacting with the material removal machinery are available on the robot controller
Sl no | Topic |
1 | Market Segmentation |
2 | Scope of the report |
3 | Abbreviations |
4 | Research Methodology |
5 | Executive Summary |
6 | Introduction |
7 | Insights from Industry stakeholders |
8 | Cost breakdown of Product by sub-components and average profit margin |
9 | Disruptive innovation in the Industry |
10 | Technology trends in the Industry |
11 | Consumer trends in the industry |
12 | Recent Production Milestones |
13 | Component Manufacturing in US, EU and China |
14 | COVID-19 impact on overall market |
15 | COVID-19 impact on Production of components |
16 | COVID-19 impact on Point of sale |
17 | Market Segmentation, Dynamics and Forecast by Geography, 2023-2030 |
18 | Market Segmentation, Dynamics and Forecast by Product Type, 2023-2030 |
19 | Market Segmentation, Dynamics and Forecast by Application, 2023-2030 |
20 | Market Segmentation, Dynamics and Forecast by End use, 2023-2030 |
21 | Product installation rate by OEM, 2023 |
22 | Incline/Decline in Average B-2-B selling price in past 5 years |
23 | Competition from substitute products |
24 | Gross margin and average profitability of suppliers |
25 | New product development in past 12 months |
26 | M&A in past 12 months |
27 | Growth strategy of leading players |
28 | Market share of vendors, 2023 |
29 | Company Profiles |
30 | Unmet needs and opportunity for new suppliers |
31 | Conclusion |
32 | Appendix |