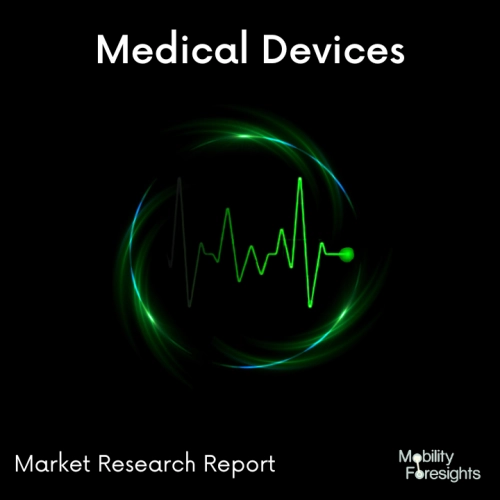
- Get in Touch with Us
Last Updated: Apr 25, 2025 | Study Period: 2022-2030
Microfiltration Media assists in preventing equipment contamination while it is being used. The protective membrane acts as a barrier to aerosolized liquids and particles while allowing gas to pass through with little pressure decrease because of its microporous nature. Microfiltration is used to purge materials of microorganisms such as bacteria, viruses, and pigments as well as other contaminants in the submicron range of particle size.
The global medical device microfiltration media market accounted for $XX Billion in 2021 and is anticipated to reach $XX Billion by 2030, registering a CAGR of XX% from 2022 to 2030.
Hollingsworth & Vose Company and Superior Felt & Filtration are working together to deliver Trupor membrane media to international markets in the sub-micron liquid filtration industry. Trupor is a microfiltration media made of Nylon 0.45 and 0.65 that performs as well as or better than microporous cast membranes.
Compared to other existing membranes, Trupor distinguishes out against typical submicron membranes by providing higher flow and lower pressures.
Better flow rates and quicker, more accurate data modeling of filtration performance are made possible by Trupor's best in class pore size homogeneity. The most recent development in sub-micron filtration is called Trupor.
Trupor is applicable in a variety of cross-platform industries and fields, such as biological fluids, process water, biopharmaceuticals, electronics, clarification, fermentation, semiconductor, food and beverage, potable water, solvent clarification, API chemical, and reagent grade chemical applications.
A surge in research into wearable devices that are capable of continuous and real-time monitoring has resulted from the growing demand for chronic disease prevention and treatment. By combining membrane separation and biosensing, wearable devices can also be used for both drug release and detection.
Transdermal delivery patches are being developed for controllable drug delivery by integrating strain sensors for force detection, microneedles for effective transdermal delivery, and drug reservoirs. For use in "lab-on-a-chip" devices, thin, porous membranes are also being integrated into microfluidic devices.
The modular Sefar Puretex system lets you change the pore size (with a narrow distribution) by changing the spinning parameter, changing the surface, using different fabrication technologies, and choosing different polymers for the membrane and protection layers.Sefar's solution is characterized by excellent permeability properties in terms of material performance.
The composite membrane is strong and flexible because of the unique layering system. During manufacturing, assembly, and use, it is highly resistant to mechanical stress. Depending on the requirements of an application, good wettability and hydrophilicity are additional advantages.
Sefar's patented technology is characterized by a high membrane surface-to-volume ratio, making its production methods unique. In liquid filtration and venting applications, fibers with a few nanometers of diameter produce billions of uniform pores that enable unrivaled flow rates. Additionally, the membrane is embedded in technical fabrics for stability and protection.
Sefar is taking a close look at some of the issues that need to be addressed in light of the numerous new applications of medical membranes that are being discussed at the moment. It is difficult to guarantee membrane biocompatibility. The introduction of active substances, particularly for the coating process, needs to be thoroughly clarified due to the constant changes in standards.
The Sefar development team sees enormous potential for the medical market by generating functionality, and Sefar has its own plans to expand its current range of medical membranes. They want to see expansion in both existing markets and new areas. This includes, for instance, coming up with solutions for the market for cell expansion.
Sefar is adding additional pore sizes and polymers to its Espin (electrospinning) membrane composite portfolios. In order to meet the growing demands of the market as well as environmental laws and regulations, they are constantly testing new coatings and production methods.
Sl no | Topic |
1 | Market Segmentation |
2 | Scope of the report |
3 | Abbreviations |
4 | Research Methodology |
5 | Executive Summary |
6 | Introduction |
7 | Insights from Industry stakeholders |
8 | Cost breakdown of Product by sub-components and average profit margin |
9 | Disruptive innovation in the Industry |
10 | Technology trends in the Industry |
11 | Consumer trends in the industry |
12 | Recent Production Milestones |
13 | Component Manufacturing in US, EU and China |
14 | COVID-19 impact on overall market |
15 | COVID-19 impact on Production of components |
16 | COVID-19 impact on Point of sale |
17 | Market Segmentation, Dynamics and Forecast by Geography, 2022-2030 |
18 | Market Segmentation, Dynamics and Forecast by Product Type, 2022-2030 |
19 | Market Segmentation, Dynamics and Forecast by Application, 2022-2030 |
20 | Market Segmentation, Dynamics and Forecast by End use, 2022-2030 |
21 | Product installation rate by OEM, 2022 |
22 | Incline/Decline in Average B-2-B selling price in past 5 years |
23 | Competition from substitute products |
24 | Gross margin and average profitability of suppliers |
25 | New product development in past 12 months |
26 | M&A in past 12 months |
27 | Growth strategy of leading players |
28 | Market share of vendors, 2022 |
29 | Company Profiles |
30 | Unmet needs and opportunity for new suppliers |
31 | Conclusion |
32 | Appendix |