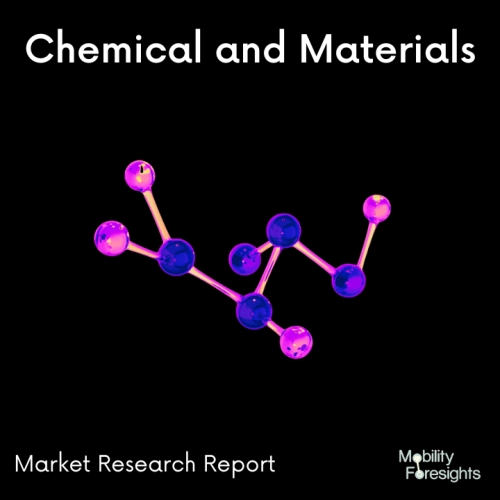
- Get in Touch with Us
Last Updated: Apr 25, 2025 | Study Period: 2024-2030
For many medical and pharmaceutical equipment, medical tubing is a crucial component. The tube controls the flow of liquid in medical devices such IVs, catheters, pumps, respirators, anaesthesia, and laboratory equipment for biopharmaceuticals.
Medical tubing comes in a variety of sizes, compositions, and performance requirements. Depending on the performance characteristics, such as hardness, flexibility, abrasion resistance, and durability, tubing can be manufactured of plastic, rubber, or metal.
If the tubing material is unsuitable, a patient may not get the right dose or dosage because drugs passing through the tubes could be chemically changed or attached to the tubing wall. To make sure that the tubing flows well and does not leak, it must be tested.
Numerous plastic materials, including polyvinyl chloride (PVC), polyethylene, thermoplastic elastomers (TPE), nylon, and silicone, can be used to create medical tubing.
The extrusion process involves a number of phases. The major component is a polymer resin, which is fed into a hopper positioned on the extruder's barrel in the form of nurdles, pellets, granules, flakes, or powder.
The resin enters the barrel through the feed throat of the hopper and is moved toward the die by a screw in the barrel. The resin is gradually heated to a melting point as it moves down the barrel while being propelled along by the screw.
Extrusion employs sophisticated machinery to regulate the process's temperature, speed, force, tension, and duration.
Medical tubing is used for anaesthesia and breathing devices, catheters, peristaltic pumps, and bio-pharmaceutical laboratory equipment, in addition to fluid management and drainage.
The categorization of Medical Tubing for use in medical applications sets it apart from other forms of tubing. Standards or certifications that specify material and specification requirements for tubes often grant this classification.
These specifications were put in place to guarantee the dependability and safety of the equipment used to care for patients and make medications.
The US FDA carefully checks the product's safety and efficacy during the manufacturing process of medical devices, therefore the manufacturer cannot avoid following regulatory procedures. Manufacturers of medical devices must put in place the right quality system.
Depending on the use, medical tubing may need a wide range of features. Most notable is opacity, which describes how transparent the tube is. To monitor fluid flow and account for potential air bubbles in the system, clear tubing is crucial for tubes that manage fluid supply.
Other characteristics include spark or static resistance, serializability, and coiling capability for storage or transportation.
The Global Medical tubing materials market accountedfor $XX Billion in 2023 and is anticipated to reach $XX Billion by 2030, registering a CAGR of XX% from 2024 to 2030.
HelixFlex, a brand-new product from Freudenberg Medical, was introduced on Wednesday at the CPhI and PMEC India.
According to the manufacturer, the product is a high-purity thermoplastic elastomer TPE tube intended for use in fluid transfer applications for biopharmaceuticals.
Georg Graf, Regional Representative for India and Head of Freudenberg Regional Corporate Center India, stated to Financial Express.com at the product launch that this is an expansion of Freudenberg's product line, adding to its already extensive line of silicone tubing and components for bioprocessing, pharmaceutical and vaccine manufacturing, filling and sampling, peristaltic pumping, lab, and medical device applications.
The business claims that because TPE tubing can be welded to existing tube lines and heat-sealed, it is perfect for pharmaceutical bioprocessing applications because it makes fluid conveyance in biopharmaceutical processes simple, quick, and safe.
Freudenberg's TPE tubing is available with a variety of sterilising methods, including autoclave, gamma radiation, x-ray, and e-beam. TPE tubing, according to the manufacturer of medical and pharmaceutical devices, is recyclable and more environmentally friendly than silicone.
Although silicone has long been the material of choice for biopharma applications, due to a recent shortage of the material, Freudenberg wanted to provide its international customers with another single-use tubing option, according to David Schwass, Director Sales & Marketing Biopharm at Freudenberg Medical, at the launch.
Sl no | Topic |
1 | Market Segmentation |
2 | Scope of the report |
3 | Abbreviations |
4 | Research Methodology |
5 | Executive Summary |
6 | Introduction |
7 | Insights from Industry stakeholders |
8 | Cost breakdown of Product by sub-components and average profit margin |
9 | Disruptive innovation in the Industry |
10 | Technology trends in the Industry |
11 | Consumer trends in the industry |
12 | Recent Production Milestones |
13 | Component Manufacturing in US, EU and China |
14 | COVID-19 impact on overall market |
15 | COVID-19 impact on Production of components |
16 | COVID-19 impact on Point of sale |
17 | Market Segmentation, Dynamics and Forecast by Geography, 2024-2030 |
18 | Market Segmentation, Dynamics and Forecast by Product Type, 2024-2030 |
19 | Market Segmentation, Dynamics and Forecast by Application, 2024-2030 |
20 | Market Segmentation, Dynamics and Forecast by End use, 2024-2030 |
21 | Product installation rate by OEM, 2023 |
22 | Incline/Decline in Average B-2-B selling price in past 5 years |
23 | Competition from substitute products |
24 | Gross margin and average profitability of suppliers |
25 | New product development in past 12 months |
26 | M&A in past 12 months |
27 | Growth strategy of leading players |
28 | Market share of vendors, 2023 |
29 | Company Profiles |
30 | Unmet needs and opportunity for new suppliers |
31 | Conclusion |
32 | Appendix |