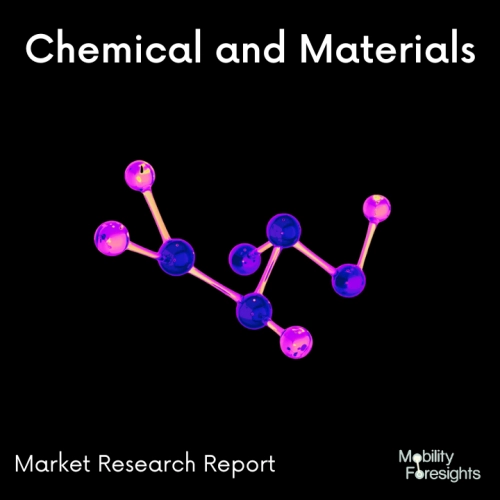
- Get in Touch with Us
Last Updated: Apr 27, 2025 | Study Period: 2024-2030
Meltblown filter media is a type of nonwoven fabric created using a specialized melt-blown process. Melt-blown filter media is made from bi-component thermoplastic polymer materials that are heated and extruded through a die array.
During the extrusion process, the hot thermoplastic is extruded through the holes of the die array and blown into a thermal exchange chamber.
The molten thermoplastic is then captured, cooled, solidified, and then stretched into a continuous, ultra-fine, filtration fiber structure.
As a filter media, melt-blown fabrics are exceptionally effective at trapping particles, dirt, and other contaminants.
Due to their microscopic-level fibers, the resulting fabric has an open structure with a large surface area, allowing it to capture more particles while allowing only the cleanest air to pass through. This makes melt-blown filter media ideal for air filtration applications.
The fabrics can be used as pre-filters in ventilation systems, air conditioners, and blower filters. They are also widely used in face masks and respirators to help filter out very fine dust and contaminants.
Melt-blown fabrics are also much more cost-effective than many other types of filtration media due to their simple production process.
The fabric is created on large rolls that can be customized to specific sizes and shapes. This allows melt-blown filter media to be used in a wide range of filtration applications.
Due to its high efficiency and low-cost production, melt-blown filter media has become one of the most widely used filtration materials on the market. It is found in a variety of industries such as HVAC systems, automotive products, food production, and medical, pharmaceutical, and engineering laboratories.
The Global Meltblown filter media market accounted for $XX Billion in 2023 and is anticipated to reach $XX Billion by 2030, registering a CAGR of XX% from 2024 to 2030.
The second generation of E-CTFE filtration media is available from US meltblown roll products company Monadnock Non-Wovens. The life and performance of liquid filtration systems are greatly increased by the product called HTAC, which is designed and produced by MNW.
High-temperature and chemical resistance E-CTFE meltblown copolymer, HTAC, is homogenous. With its resistance to oxidising agents, acids, caustic media, and many solvents at high temperatures, it is a better material solution for liquid filtration than PVDF and PTFE due to its tolerance to pH 1â14.
Manufacturing of semiconductors, pharmaceuticals, and chloro-alkalis are three industries that use HTAC.High permeation resistance and safety at elevated temperatures are provided by this inventive medium creation.
HTAC is manufactured using only 100% sustainable wind energy (Green-e certified RECs), just like all other MNW products. They are glad to provide HTAC for important production procedures. Meltblown roll goods of various weights, both calendared and uncalendered, are offered for HTAC E-CTFE medium. For use as a duct or pipe wrap veil, apertured versions are also offered.
With its exceptional dirt holding capacity, minimal pressure drop, and high filtering effectiveness, LyPore MB, Alkegen's new meltblown liquid filtration media series, is engineered to satisfy even the most demanding application needs.
It is designed to meet the most challenging liquid filtering problems and is offered in single layer or composite form, as well as polypropylene and PBT.Ion exchange resins and activated carbon are only two of the many functional adsorbents that may be layered and produced with remarkable consistency using Alkegen's innovative LydAir GP molecular filtering media.
A combined medium for particle and molecular filtration can also be created by laminating particulate filter media in a line.Under the direction of the Alkegen filtration product development team, these three HEF mediaâone for air, one for liquid, and one for molecular applicationsârepresent the first wave of cutting-edge materials created and made available. With these launches, Unifrax's dependable, quick innovation skills are combined with Lydall's well-known filtration and production experience.
Sl no | Topic |
1 | Market Segmentation |
2 | Scope of the report |
3 | Abbreviations |
4 | Research Methodology |
5 | Executive Summary |
6 | Introduction |
7 | Insights from Industry stakeholders |
8 | Cost breakdown of Product by sub-components and average profit margin |
9 | Disruptive innovation in the Industry |
10 | Technology trends in the Industry |
11 | Consumer trends in the industry |
12 | Recent Production Milestones |
13 | Component Manufacturing in US, EU and China |
14 | COVID-19 impact on overall market |
15 | COVID-19 impact on Production of components |
16 | COVID-19 impact on Point of sale |
17 | Market Segmentation, Dynamics and Forecast by Geography, 2024-2030 |
18 | Market Segmentation, Dynamics and Forecast by Product Type, 2024-2030 |
19 | Market Segmentation, Dynamics and Forecast by Application, 2024-2030 |
20 | Market Segmentation, Dynamics and Forecast by End use, 2024-2030 |
21 | Product installation rate by OEM, 2023 |
22 | Incline/Decline in Average B-2-B selling price in past 5 years |
23 | Competition from substitute products |
24 | Gross margin and average profitability of suppliers |
25 | New product development in past 12 months |
26 | M&A in past 12 months |
27 | Growth strategy of leading players |
28 | Market share of vendors, 2023 |
29 | Company Profiles |
30 | Unmet needs and opportunity for new suppliers |
31 | Conclusion |
32 | Appendix |