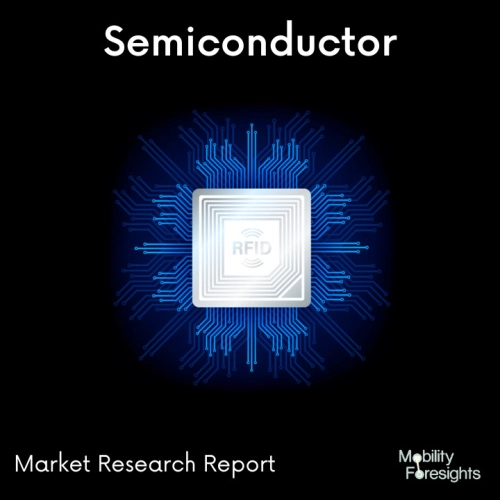
- Get in Touch with Us
Last Updated: Apr 25, 2025 | Study Period: 2023-2030
The method of wet chemically etching semiconductors (mostly silicon) with the aid of a metal catalyst is known as metal assisted chemical etching system , or MACE. The metal catalyst is typically placed on the surface of a semiconductor in the form of a thin layer or nanoparticles.
The metal-coated semiconductor is then dipped into an etching solution that also contains an oxidizing agent and hydrofluoric acid. The reduction of the oxidizing agent and, consequently, the dissolution of silicon are catalyzed by the metal on the surface.
The majority of the research is spatially limited, meaning that the occurrence of an accelerated dissolving rate only occurs in close proximity to a metal particle at the surface. This eventually results in the development of straight pores.
Because Metal-assisted chemical etching systems enable totally anisotropic etching of silicon substrates, which is not achievable with conventional wet chemical etching processes (see figure to the right), it is the subject of extensive research.
Before being submerged in an etching solution, the silicon substrate is often covered with a protective layer, such as photoresist. Isotropic etching occurs because the etching fluid often attacks the substrate in any direction.
However, it is frequently necessary for the sidewalls of the etched trenches to be steep in semiconductor engineering. Reactive ion etching and other technologies that operate in the gas phase are frequently used to achieve this. Compared to straightforward wet etching, these techniques demand expensive equipment. Metal-assisted chemical etching systems in theory permits the construction of steep trenches.
The Global Metal-assisted chemical etching system Market accounted for $XX Billion in 2022 and is anticipated to reach $XX Billion by 2030, registering a CAGR of XX% from 2023 to 2030.
Metal-assisted chemical etching systems (MacEtch), which defies the isotropic nature of conventional chemical etching, enables spatially tailored anisotropic etching by utilizing patterned metal catalyst sheets to locally increase the etch rate of certain semiconductors.
With this simple method, largely in solution, significant progress has been made toward the creation of nanostructures with extraordinary aspect ratios. The path to manufacturing scalability is still tough, nevertheless, due to the challenges of uniformly controlling etch rates across a large area and etch morphology (such as porosity and aggregation).
Here, we present the first VP-MacEtch technique that allows for independent control of the etchant flow rates, injection and pulse times, and chamber pressure. In order to provide photo-enhanced VP-MacEtch, a further degree of freedom, light irradiation, is integrated. With each other, different silicon nanostructures are displayed.
Sl no | Topic |
1 | Market Segmentation |
2 | Scope of the report |
3 | Abbreviations |
4 | Research Methodology |
5 | Executive Summary |
6 | Introduction |
7 | Insights from Industry stakeholders |
8 | Cost breakdown of Product by sub-components and average profit margin |
9 | Disruptive innovation in the Industry |
10 | Technology trends in the Industry |
11 | Consumer trends in the industry |
12 | Recent Production Milestones |
13 | Component Manufacturing in US, EU and China |
14 | COVID-19 impact on overall market |
15 | COVID-19 impact on Production of components |
16 | COVID-19 impact on Point of sale |
17 | Market Segmentation, Dynamics and Forecast by Geography, 2023-2030 |
18 | Market Segmentation, Dynamics and Forecast by Product Type, 2023-2030 |
19 | Market Segmentation, Dynamics and Forecast by Application, 2023-2030 |
20 | Market Segmentation, Dynamics and Forecast by End use, 2023-2030 |
21 | Product installation rate by OEM, 2023 |
22 | Incline/Decline in Average B-2-B selling price in past 5 years |
23 | Competition from substitute products |
24 | Gross margin and average profitability of suppliers |
25 | New product development in past 12 months |
26 | M&A in past 12 months |
27 | Growth strategy of leading players |
28 | Market share of vendors, 2023 |
29 | Company Profiles |
30 | Unmet needs and opportunity for new suppliers |
31 | Conclusion |
32 | Appendix |