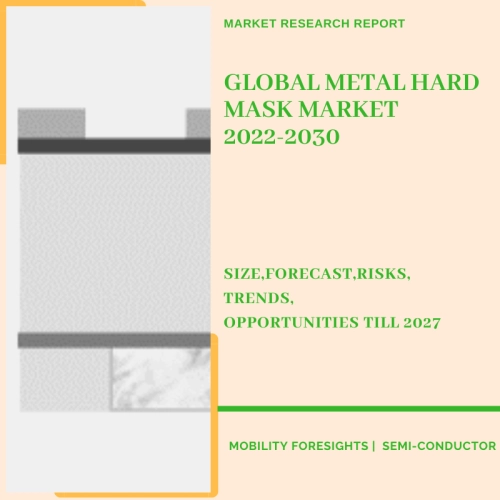
- Get in Touch with Us
Last Updated: Apr 25, 2025 | Study Period: 2022-2030
In semiconductor fabrication, a hard mask is used as an etch mask in place of a polymer or other organic "soft" resist material.
When the substance being etched is an organic polymer, hard masks are required. Since the photoresist being used to define its patterning is likewise an organic polymer, anything used to etch this material will also etch the photoresist.
This occurs, for instance, when low-dielectric insulating layers used in VLSI production are patterned. Oxygen, fluorine, chlorine, and other reactive gases employed in plasma etching have a tendency to easily etch polymers.
Using a hard mask necessitates an additional deposition procedure, which raises the cost. First, a typical photoresist method is used to deposit and etch the hard mask material into the desired design.
The underlying material can then be etched through the hard mask after that. Finally, a second etching procedure is used to remove the hard mask. Metal or dielectric can be used as hard mask materials.
Low-dielectric materials are often etched using silicon-based masks made of silicon dioxide or silicon carbide.
However, an etchant that destroys silicon compounds is necessary for SiOCH (carbon doped hydrogenated silicon oxide), a material used to insulate copper interconnects.
Hard masks made of metal or amorphous carbon are utilised with this material. Tantalum nitride has also been utilised, but titanium nitride is the material most frequently used for hardmasks.
The Global metal hard mask market accounted for $XX Billion in 2021 and is anticipated to reach $XX Billion by 2030, registering a CAGR of XX% from 2022 to 2030.
For BEOL patterning, the TiN Hard Mask (TiN-HM) integration approach has been widely used to prevent ultra low-k (ULK) damage during the plasma-ash process .
New integration strategies must be adopted as the technology node develops to pattern features with a pitch of less than 80 nm using 193 nm immersion lithography.
To achieve Self-Aligned-Via (SAV) integration, which fixes the via-metal short yield and TDDB problems brought on by Litho-Etch-Litho-Etch (LELE) misalignment, thicker TiN-HM is specifically required .
The high aspect ratio of the structures makes the Cu filling procedure considerably more challenging if the thick TiN is not removed.
Additionally, the use of a TiN hard mask may result in the formation of a time-dependent crystal growth (TiCOF) residue between line etching and metal deposition which further impedes copper filling.
One solution to the issue is post-etch treatment after line etching, but N2 plasma is not effective enough to completely suppress the residue , and the CH4 treatment suggested in may be challenging to implement for 14 nm node.
Therefore, an effective wet strip and clean provides a better solution.
Sl no | Topic |
1 | Market Segmentation |
2 | Scope of the report |
3 | Abbreviations |
4 | Research Methodology |
5 | Executive Summary |
6 | Introduction |
7 | Insights from Industry stakeholders |
8 | Cost breakdown of Product by sub-components and average profit margin |
9 | Disruptive innovation in the Industry |
10 | Technology trends in the Industry |
11 | Consumer trends in the industry |
12 | Recent Production Milestones |
13 | Component Manufacturing in US, EU and China |
14 | COVID-19 impact on overall market |
15 | COVID-19 impact on Production of components |
16 | COVID-19 impact on Point of sale |
17 | Market Segmentation, Dynamics and Forecast by Geography, 2022-2030 |
18 | Market Segmentation, Dynamics and Forecast by Product Type, 2022-2030 |
19 | Market Segmentation, Dynamics and Forecast by Application, 2022-2030 |
20 | Market Segmentation, Dynamics and Forecast by End use, 2022-2030 |
21 | Product installation rate by OEM, 2022 |
22 | Incline/Decline in Average B-2-B selling price in past 5 years |
23 | Competition from substitute products |
24 | Gross margin and average profitability of suppliers |
25 | New product development in past 12 months |
26 | M&A in past 12 months |
27 | Growth strategy of leading players |
28 | Market share of vendors, 2022 |
29 | Company Profiles |
30 | Unmet needs and opportunity for new suppliers |
31 | Conclusion |
32 | Appendix |