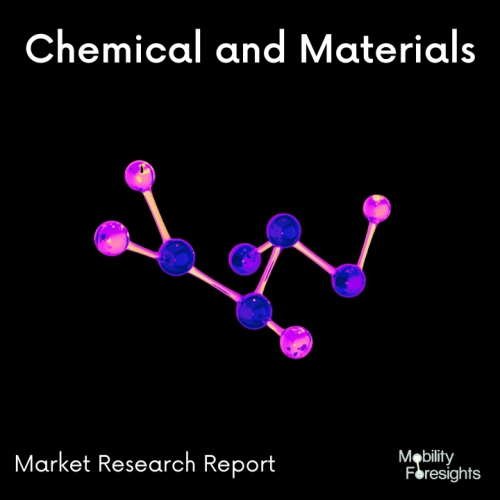
- Get in Touch with Us
Last Updated: Apr 25, 2025 | Study Period: 2024-2030
Metalworking fluids are used in industrial machining and grinding processes to minimize heat and friction while also removing metal particles. There are several formulas available, ranging from straight oils like petroleum oils to water-based fluids like soluble oils and synthetic fluids.
While MWFs contain many different components and additions, there are four fundamental kinds. Oils in their natural state, Also known as cutting or tidy oils, mineral petroleum, animal, marine, vegetable, or synthetic oils are used in this kind. Mineral oils are now either extensively solvent refined or severely hydrotreated.
They are primarily constituted of water and oils, but additional additives such as antioxidants, antifoams, anti-corrosives, biocides, fungicides, and so on are added to extend the efficiency and longevity of MCF.
These fluids aid in temperature management throughout the metal-cutting process by absorbing heat and reducing tool and workpiece damage. Cutting fluids aid to enhance workpiece surface finish by washing away chips and eliminating built-up edges.
The Global metalworking fluids market accounted for $XX Billion in 2023 and is anticipated to reach $XX Billion by 2030, registering a CAGR of XX% from 2024 to 2030.
JTM Products Launches New Line of Synthetic Metalworking Fluids. JTM Products has just introduced a new range of synthetic metalworking fluids designed for machining steel, aluminium, and other difficult-to-machine metals.
SynMAX coolants are intended to outperform semi-synthetic fluids without the need of oil. The fluids use a proprietary BioArmor technology to provide built-in resistance to bacterial growth without the need of bactericides. In addition to having a long sump life, they may avoid sensitive metal discoloration as well as surface and vapour-phase corrosion.
The coolants are well-suited for multi-metal operations since they are designed to cut aluminium as effectively as steel. They are also perfect for improving cycle time and tool life, as well as for accurate tolerance and high finishes.
There are three SynMAX coolants available: 2505 for moderate duty, 2515 for heavy load, and 2525 for severe duty. All comply with the European Union's Registration, Evaluation, Authorization, and Restriction of Chemicals (REACH) law and meet the Boeing BAC 5008 Revision U for steel, aluminium, and titanium.
Without the use of potentially dangerous biocides, the FluidWorker product series employs UV light to stop the growth of germs in metalworking fluids. The newest product in the line, FluidWorker150, has additional capabilities such as automation of routine fluid maintenance through measurement and adjustment of concentration and machine tank level.
Not only will FluidWorker150 eliminate a sizable manual maintenance requirement, but machine operators will also experience less exposure to health risks including biocides and pathogens. Correct concentration results in increased tool life, longer machine uptime, and lower fluid consumption, all of which improve production quality.
Overall, the enhancements lead to significant cost and productivity reductions as well as a more appealing and sustainable manufacturing environment.A new line of non-chlorinated metalworking fluids was just introduced by Petro-Canada Lubricants to help with friction reduction across a variety of processes.
For both general-purpose and specialized applications, such as milling, turning, drilling, tapping, and grinding, the METWORX product line is offered in a number of configurations.
While the SOLCUT HD 2500 CF is a soluble cutting oil for quick heat removal, the NEATCUT HD 32 CF is a medium-viscosity neat cutting fluid. The SYNCUT 150 LD XL and 300 HD XL are low-foam, biostable, semi-synthetic fluids, with the 150 LD XL intended for light to moderate application and the 300 HD XL for moderate to heavy-duty operation.
A brand-new, ground-breaking phosphate ester that offers great performance and superior sustainability in metalworking fluid formulations has been introduced by Clariant, one of the industry's top providers of sustainable chemicals and solutions.
Hostaphat 1738 blends performance under tremendous pressure with a great low foam profile and potent emulsification abilities. The novel ester is a top choice for formulators and production managers since it can easily be included into a number of metal working formulas, including semi-synthetic, synthetic, soluble oil, and straight oil.
Additionally, Hostaphat 1738 has excellent sustainability qualities. Because natural alcohol was employed, it is bio-derived and has much less phosphorus than typical phosphate esters.
Environmentally adapted lubricants, or EALs, include a rising class of approaches called minimum quantity lubrication (MQL) strategies. MQL typically uses modest amounts of oil and compressed air sprays to perform the same functions as a MWF without producing as much watery waste.
Air is a poor coolant, thus modern oil-in-air MQL systems are only appropriate for light machining processes that don't call for a lot of heat dissipation. As a result, research is currently concentrated on creating new strategies that expand the application of MQL to more demanding machining operations.
Since MQL technologies are still in their infancy, adoption is hindered by both technical and financial challenges. They need brand-new delivery mechanisms that are distinct from those for aqueous systems.
Industry has seen the advantages of transitioning from water-based systems to gas-based MQL systems in terms of the environment, health, performance, and economy.This is significant since MWF life cycle costs can account for the costs associated with producing metals.
Low-volume air spray lubricant delivery, often known as near dry machining, lowers purchasing and operating expenses while significantly lowering MWF system energy usage. Since mist and other oily waste associated with flood delivery of water-based MWFs are eliminated, MQL systems are even said to improve safety and operator morale.
MQL has only been widely used to date, but, as a result of the fact that most employees are unsure of how to create and use MQL systems. Additionally, there are also technical concerns on how to use MQL to accomplish adequate cooling in difficult machining procedures involving sophisticated materials.
Sl no | Topic |
1 | Market Segmentation |
2 | Scope of the report |
3 | Abbreviations |
4 | Research Methodology |
5 | Executive Summary |
6 | Introduction |
7 | Insights from Industry stakeholders |
8 | Cost breakdown of Product by sub-components and average profit margin |
9 | Disruptive innovation in the Industry |
10 | Technology trends in the Industry |
11 | Consumer trends in the industry |
12 | Recent Production Milestones |
13 | Component Manufacturing in US, EU and China |
14 | COVID-19 impact on overall market |
15 | COVID-19 impact on Production of components |
16 | COVID-19 impact on Point of sale |
17 | Market Segmentation, Dynamics and Forecast by Geography, 2023-2030 |
18 | Market Segmentation, Dynamics and Forecast by Product Type, 2023-2030 |
19 | Market Segmentation, Dynamics and Forecast by Application, 2023-2030 |
20 | Market Segmentation, Dynamics and Forecast by End use, 2023-2030 |
21 | Product installation rate by OEM, 2023 |
22 | Incline/Decline in Average B-2-B selling price in past 5 years |
23 | Competition from substitute products |
24 | Gross margin and average profitability of suppliers |
25 | New product development in past 12 months |
26 | M&A in past 12 months |
27 | Growth strategy of leading players |
28 | Market share of vendors, 2023 |
29 | Company Profiles |
30 | Unmet needs and opportunity for new suppliers |
31 | Conclusion |
32 | Appendix |