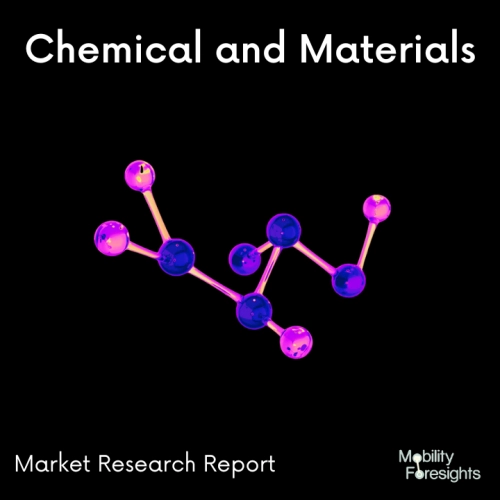
- Get in Touch with Us
Last Updated: Apr 25, 2025 | Study Period: 2023-2030
Many vacuum manufacturing processes require a highly efficient separation of solids, liquids and vapors. This is not only to keep the systems functioning properly, but also to capture valuable process outputs and minimize waste.
This can be accomplished using specialty filtration and separation products/systems that separate product from an air/gas stream under vacuum conditions.
Oil mist can escape from oil lubricated vacuum pumps operating on the manufacturing floor. Even with an internal separator provided by the vacuum pump OEM, and under certain conditions, an oil-sealed vacuum pump may release excess oil mist discharge through the exhaust port.
This mist can cause unpleasant odors and discharged oils can create slippery surfaces causing unnecessary health hazards.
In addition to creating an uncomfortable and unsafe working environment, excessive oil mist emissions can affect the purity of the facility itself and cause contamination of raw materials and the output products.
In this scenario, a Filtering oil mist eliminator or an adsorbent activated carbon filter can be used to capture this pollution from the exhaust ports keeping the work environment safe and clean.
These specialty systems are used to separate specific vapors, fluids, or solids from the air stream carried over from the manufacturing process.
The Mexico Industrial Filters Market accounted for $XX Billion in 2022 and is anticipated to reach $XX Billion by 2030, registering a CAGR of XX% from 2023 to 2030.
Pure Aqua Industrial Multi Media Filter 350 GPM - Industrial multi-media filters are designed to eliminate suspended particles from water and mainly deal with feed water that has a turbidity of up to 20 NTU. During the filtration process, tiny particles proceed down to smaller and finer media levels.
The cracks within these media entrap particles down to 10 microns. The larger particulates that were blocked are caught on top of the filtration bed.
Multi-media filters are sometimes backwashed when an increase in pressure differential to approximately 10-12 PSI is discovered or when a timer starts.
During the backwash, water is directed upward through the filter at approximately 12-15 gpm/ft² for close to ten minutes, raising the media. This also purifies and divides the dirt particles which are thrown into the backwash water to the drain.
Sl no | Topic |
1 | Market Segmentation |
2 | Scope of the report |
3 | Abbreviations |
4 | Research Methodology |
5 | Executive Summary |
6 | Introduction |
7 | Insights from Industry stakeholders |
8 | Cost breakdown of Product by sub-components and average profit margin |
9 | Disruptive innovation in the Industry |
10 | Technology trends in the Industry |
11 | Consumer trends in the industry |
12 | Recent Production Milestones |
13 | Component Manufacturing in US, EU and China |
14 | COVID-19 impact on overall market |
15 | COVID-19 impact on Production of components |
16 | COVID-19 impact on Point of sale |
17 | Market Segmentation, Dynamics and Forecast by Geography, 2023-2030 |
18 | Market Segmentation, Dynamics and Forecast by Product Type, 2023-2030 |
19 | Market Segmentation, Dynamics and Forecast by Application, 2023-2030 |
20 | Market Segmentation, Dynamics and Forecast by End use, 2023-2030 |
21 | Product installation rate by OEM, 2023 |
22 | Incline/Decline in Average B-2-B selling price in past 5 years |
23 | Competition from substitute products |
24 | Gross margin and average profitability of suppliers |
25 | New product development in past 12 months |
26 | M&A in past 12 months |
27 | Growth strategy of leading players |
28 | Market share of vendors, 2023 |
29 | Company Profiles |
30 | Unmet needs and opportunity for new suppliers |
31 | Conclusion |
32 | Appendix |