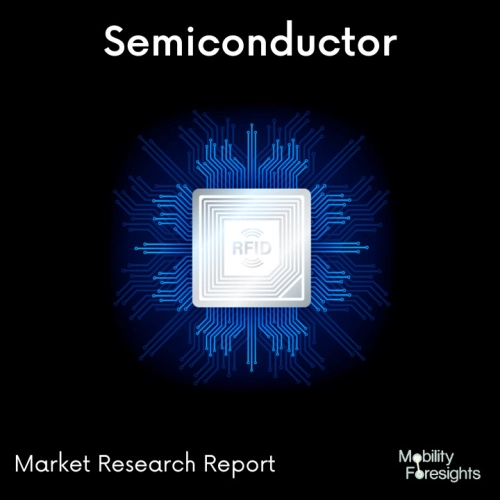
- Get in Touch with Us
Last Updated: Apr 26, 2025 | Study Period: 2024-2030
Microcontact printing (μCP) is a simple and cost-effective technique for patterning surfaces with precise control over the geometry, size, and alignment of features. This technique is used to fabricate nanoscale features, typically in the range of 10-100 microns, by transferring an elastomeric stamp onto a substrate.
The stamp is typically composed of polydimethylsiloxane (PDMS) and coated with an adhesive material that can be patterned with a variety of features. The features on the stamp can be patterned with a variety of techniques, such as photolithography, laser ablation, or direct printing.
Once the stamp is patterned, it is then pressed onto the substrate and the adhesive material is transferred onto the substrate, resulting in a patterned surface.
This technique is advantageous because it is relatively easy to fabricate and can be used to pattern a variety of materials, including metals, polymers, and composites. Additionally, μCP is an effective method for creating micron-scale features that are highly precise, repeatable, and uniform.
Thus, this technique is often used for creating microelectronic components, such as transistors and capacitors, as well as for surface patterning applications such as cell culturing and biosensing.
The Global Microcontact printing Market accounted for $XX Billion in 2023 and is anticipated to reach $XX Billion by 2030, registering a CAGR of XX% from 2024 to 2030.
For the purpose of designing surfaces using microcontact printing in conjunction with selective surface dewetting, a general microstructuring technique was created.
Microcontact printing was used to print self-assembled monolayers, such as octadecyl trichlorosilane, on silicon or glass substrates. While the uncoated areas continued to be hydrophilic, the areas coated with octadecyl trichlorosilane became hydrophobic.
These functionalized substrates enable polymers or resists to selectively wet or wetter surfaces. The hydrophilic areas of the substrate were specifically coated with resists, such as poly(methyl methacrylate), while the hydrophobic areas of the substrate were left uncoated.
This method enables resist patterning on surfaces without the need for photolithography. In this work, metallic microstructures including source-drain electrodes for organic field-effect transistors and micro-coils for radio-frequency identification tags were lifted off using the resist.
The biological performance of biomedical devices is mostly determined by their surface qualities, indicating the critical need for surface modification. With tailored inks, micro-contact printing (μCP), a versatile surface modification technology, may manipulate surface chemical and biological cues in addition to producing specific topographical features. In order to give the implant advanced functions, a variety of surface modification techniques have been developed.
In recent decades, significant progress has been made in improving the precision, controllability, and application of these techniques in the biomedical field. Among the often-used techniques are photolithography, direct laser writing, femtosecond laser writing, nanoimprint lithography, and micro-contact printing (μCP).
The most widely used surface technique for creating surface patterns is photolithography, which makes use of a substance that may polymerize when exposed to light.
Sl no | Topic |
1 | Market Segmentation |
2 | Scope of the report |
3 | Abbreviations |
4 | Research Methodology |
5 | Executive Summary |
6 | Introdauction |
7 | Insights from Industry stakeholders |
8 | Cost breakdown of Product by sub-components and average profit margin |
9 | Disruptive innovation in theIndustry |
10 | Technology trends in the Industry |
11 | Consumer trends in the industry |
12 | Recent Production Milestones |
13 | Component Manufacturing in US, EU and China |
14 | COVID-19 impact on overall market |
15 | COVID-19 impact on Production of components |
16 | COVID-19 impact on Point of sale |
17 | Market Segmentation, Dynamics and Forecast by Geography, 2024-2030 |
18 | Market Segmentation, Dynamics and Forecast by Product Type, 2024-2030 |
19 | Market Segmentation, Dynamics and Forecast by Application, 2024-2030 |
20 | Market Segmentation, Dynamics and Forecast by End use, 2024-2030 |
21 | Product installation rate by OEM, 2023 |
22 | Incline/Decline in Average B-2-B selling price in past 5 years |
23 | Competition from substitute products |
24 | Gross margin and average profitability of suppliers |
25 | New product development in past 12 months |
26 | M&A in past 12 months |
27 | Growth strategy of leading players |
28 | Market share of vendors, 2023 |
29 | Company Profiles |
30 | Unmet needs and opportunity for new suppliers |
31 | Conclusion |
32 | Appendix |