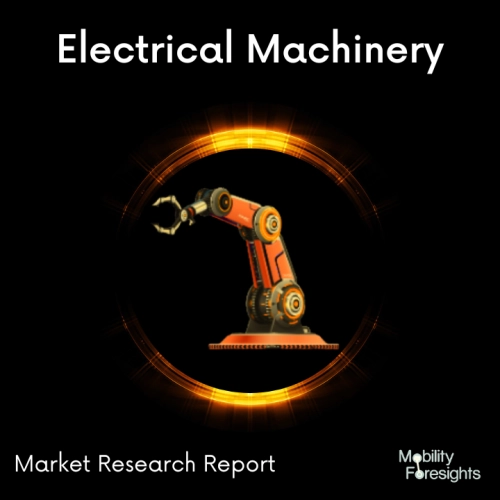
- Get in Touch with Us
Last Updated: Apr 26, 2025 | Study Period: 2024-2030
To generate torque, microstep drivers supply electricity to the proper step motor winding. Using pulse-width modulated voltage to direct current to the motor windings, microstepping is made possible.
The motor windings receive two voltage sine waves that are 90 degrees out of phase from the driver. Current in one winding increases while decreasing in the other winding.
They accurately distribute the current throughout the motor phases, allowing the step motor to be positioned at smaller steps between full steps.
They have less torque but offer a higher resolution. A step can be greatly reduced in size by microstepping; typically, there are between 16 and 64 microsteps in a full step.
This is accomplished by introducing unique algorithms to modify the electrical impulse's strength. Increased accuracy is not the benefit of microstepping; in fact, microstepping frequently results in decreased accuracy. Stepper motor applications can now move more evenly and smoothly thanks to microstepping.
Microstepping eliminates resonance issues, offers softer actuation, and lowers mechanical noise.As previously stated, microstepping has no effect on a stepper motor's accuracy.This is because the design of stepper motors will result in intrinsic inaccuracy.
Microstepping does not improve accuracy in this way. In fact, accuracy may start to decline as microsteps get smaller. The decrease in incremental torque as you increase the number of microsteps is another drawback of microstepping.
Magnetic backlash will occur if there is any load torque, shifting the rotor from its intended position until enough torque is produced. Microstepping has both advantages and drawbacks.
You need to consider these advantages and disadvantages in light of your own unique application requirements in order to decide if it's the appropriate choice for you. Although it might not be effective in every situation, microstepping has several advantages in the correct circumstances.
The Global Microstep Driver market accounted for $XX Billion in 2023 and is anticipated to reach $XX Billion by 2030, registering a CAGR of XX% from 2024 to 2030.
A constant-current 2-phase stepping motor driver for automotive applications called "TB9120AFTG" has been released by Toshiba Electronic Devices & Storage Corporation.
Without the use of a complicated functional MCU or specialised software, the new IC generates a sine-wave current using only a straightforward clock input interface.
As a replacement for the TB9120FTG, Toshiba created the TB9120AFTG, which featured the company's first automotive stepping motor driver and offered enhanced noise resistance. The DMOS FETs used in TB9120AFTG have a low on-resistance and can handle a maximum current of 1.5A.
The controller that creates micro-stepping sine waves and the DMOS FETs are both housed in a compact QFN-style device. The new IC conforms to AEC-Q100, a recognised standard for electronic components for automotive applications, and offers an operating temperature range of -40 to 125°C.
It is appropriate for a variety of general automobile stepping motor applications, including stepping motor expansion valves and heads-up display projection position adjustment.
Sl no | Topic |
1 | Market Segmentation |
2 | Scope of the report |
3 | Abbreviations |
4 | Research Methodology |
5 | Executive Summary |
6 | Introduction |
7 | Insights from Industry stakeholders |
8 | Cost breakdown of Product by sub-components and average profit margin |
9 | Disruptive innovation in the Industry |
10 | Technology trends in the Industry |
11 | Consumer trends in the industry |
12 | Recent Production Milestones |
13 | Component Manufacturing in US, EU and China |
14 | COVID-19 impact on overall market |
15 | COVID-19 impact on Production of components |
16 | COVID-19 impact on Point of sale |
17 | Market Segmentation, Dynamics and Forecast by Geography, 2024-2030 |
18 | Market Segmentation, Dynamics and Forecast by Product Type, 2024-2030 |
19 | Market Segmentation, Dynamics and Forecast by Application, 2024-2030 |
20 | Market Segmentation, Dynamics and Forecast by End use, 2024-2030 |
21 | Product installation rate by OEM, 2023 |
22 | Incline/Decline in Average B-2-B selling price in past 5 years |
23 | Competition from substitute products |
24 | Gross margin and average profitability of suppliers |
25 | New product development in past 12 months |
26 | M&A in past 12 months |
27 | Growth strategy of leading players |
28 | Market share of vendors, 2023 |
29 | Company Profiles |
30 | Unmet needs and opportunity for new suppliers |
31 | Conclusion |
32 | Appendix |