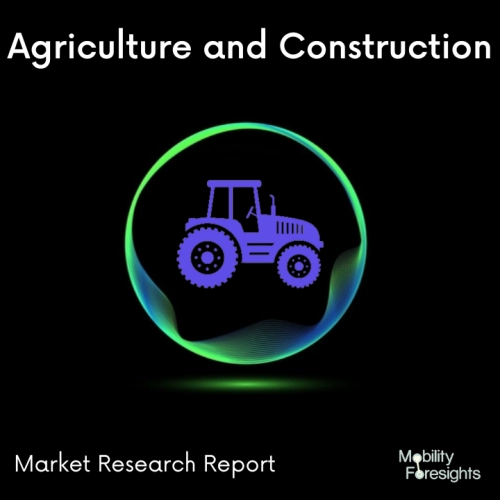
- Get in Touch with Us
Last Updated: Apr 25, 2025 | Study Period: 2023-2030
Because of the hazards posed by the presence of flammable gas and dust in the working environment, a particular class of explosives for use in coal mines has been developed.
In general, these are detonating explosives to which cooling salts (for example, sodium chloride) or a cooling agent(ammonium nitrate) have been added with the goal of reducing either the amount or the temperature of the flame produced by the explosive upon detonation.
These methods have provided a greater margin of safety in the presence of firedamp.
One significant disadvantage has been that the explosive's effectiveness has naturally diminished, making detonation less assured; that is, the explosive's efficiency has dropped.
The likelihood of misfires has risen.
As a result, a boundary is established beyond which it is not recommended to proceed.
Some analysts believe that this limit has already been reached.
Blasting is the most cost-effective approach to shatter rock so that earth-moving equipment can extract it.
This, in turn, lowers the costs of construction materials such as gravel and concrete, coal-fired energy, and a variety of other goods generated from limestone, coal, and other minerals.
People who live near quarries and coal mines frequently express worry about the dynamiting that occurs there.
In reality, dynamite, a nitroglycerin-based explosive, is no longer often used in Ohio's quarries and surface coal mines.
ANFO, emulsions, and ANFO/emulsion mixtures are the most often utilized explosives.
ANFO is a compound composed of ammonium nitrate (AN) and fuel oil (FO).
The AN is a prill (small, bead-like particle) that absorbs the fuel oil. An emulsion is simply a waterproof ANFO.
Both are significantly less dangerous than explosives and crush more rock for the same price.
Blast Holes are typically bored vertically in a grid arrangement.
Blasthole diameters in quarries typically vary from two to seven inches and five to nine inches in surface coal mines, with depths ranging from 10 to 70 feet.
Fracturing of rock happens no more than 20 to 30 feet from any blasthole after detonation, depending mostly on hole diameter and the densities of the rock and explosive.
One prevalent misperception is that fracturing occurs well beyond the mine property, even kilometers away from the explosion site.
If this were true, blastholes might be set much more widely apart than the currently utilized spacing of six to 18 feet in quarries and 12 to 25 feet in surface coal mines, making blasting much more cost effective because less drilling and explosives would be required.
Another prevalent myth about blasting is that major fracture happens long below the blasthole's bottom.
In reality, the majority of the gas pressure forces generated by the explosive's explosion radiate outward along the length of the cylindrical blasthole.
Gas-pressure forces below the hole vary depending on the diameter, kind of explosive, and composition of the rock.
The blasthole's bottom is fairly small, and rock fracture is often restricted to a few feet.
In most surface coal mines, a three to five-foot buffer between the bottom of the blast holes and the top of the coal seam is sufficient to keep the coal (which is fragile to begin with) from being fractured and polluted by the rock debris directly above it.
Failure to protect the coal from fracturing can considerably raise the cost of cleaning the coal and diminish the mine operator's revenues.
When a blast detonates, part of the explosive energy that is not used to shatter rock goes through the earth as wave motion, comparable to the ripple formed in a pond when a stone hits the water.
This wave motion, or ground vibration, moves at rates ranging from 5,000 to 20,000 feet per second, depending on the density and thickness of the rock and soil.
Its energy decays fast with distance from the blast and is typically unnoticeable by humans beyond a few thousand feet.
Because explosives are costly and vibration represents lost energy, it is advantageous for the blaster to utilize as much of the energy as possible in fragmentation, hence minimizing vibration.
Blasting seismographs are used to measure earthquakes.
Blasting seismographs are used to calculate particle velocity, which is the rate at which each particle in the ground oscillates as the wave motion passes.
This is analogous to monitoring the speed of a fishing bobber in a pond as it goes up and down when a ripple passes beneath it.
Particle velocity is measured in inches per second, although beyond a few hundred feet from a blast, the actual movement of the earth, or displacement, is usually only a fraction of an inch, roughly the thickness of a piece of paper or less.
As a result, it is critical to realize that a particle velocity value in inches per second corresponds to the speed at which the ground moves.
The Global Mining Explosives Market accounted for $XX Billion in 2022 and is anticipated to reach $XX Billion by 2030, registering a CAGR of XX% from 2023 to 2030.
BME is a prominent manufacturer and supplier of bulk emulsions, on-site bulk emulsion facilities, packaged explosives, and initiating systems to the mining, quarrying, and construction sectors.
Products and services include fly rock management, muck pile profiling, and fragmentation analysis, as well as blast consultancy, auditing, monitoring, and software.
BME has leveraged significant investment in the production base as a part of the JSE-listed Omnia Group.
Clients can expect flawless service thanks to the production infrastructure and supply network that have been built over the last three decades.
In addition, enforce a best practice workplace that prioritizes the health and safety of all stakeholders.
Sl no | Topic |
1 | Market Segmentation |
2 | Scope of the report |
3 | Abbreviations |
4 | Research Methodology |
5 | Executive Summary |
6 | Introduction |
7 | Insights from Industry stakeholders |
8 | Cost breakdown of Product by sub-components and average profit margin |
9 | Disruptive innovation in the Industry |
10 | Technology trends in the Industry |
11 | Consumer trends in the industry |
12 | Recent Production Milestones |
13 | Component Manufacturing in US, EU and China |
14 | COVID-19 impact on overall market |
15 | COVID-19 impact on Production of components |
16 | COVID-19 impact on Point of sale |
17 | Market Segmentation, Dynamics and Forecast by Geography, 2023-2030 |
18 | Market Segmentation, Dynamics and Forecast by Product Type, 2023-2030 |
19 | Market Segmentation, Dynamics and Forecast by Application, 2023-2030 |
20 | Market Segmentation, Dynamics and Forecast by End use, 2023-2030 |
21 | Product installation rate by OEM, 2023 |
22 | Incline/Decline in Average B-2-B selling price in past 5 years |
23 | Competition from substitute products |
24 | Gross margin and average profitability of suppliers |
25 | New product development in past 12 months |
26 | M&A in past 12 months |
27 | Growth strategy of leading players |
28 | Market share of vendors, 2023 |
29 | Company Profiles |
30 | Unmet needs and opportunity for new suppliers |
31 | Conclusion |
32 | Appendix |