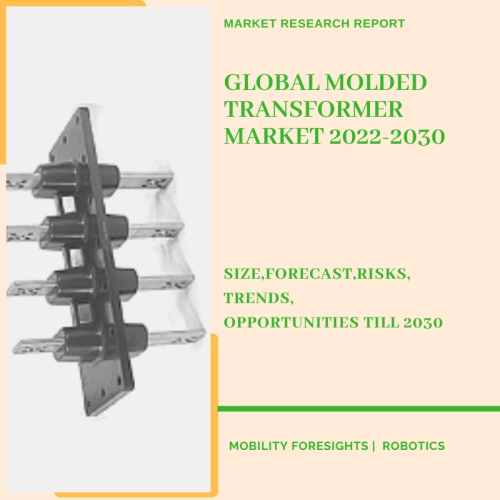
- Get in Touch with Us
Last Updated: Apr 25, 2025 | Study Period: 2022-2030
The transformer molding process is as follows: The "assembled" transformer is sandwiched between two injection moulds, with the transformer core acting as a third mould piece, to partially encase the transformer.
A "assembled" transformer in this context is one that has finished windings and the necessary magnetic core material assembled into the tapering aperture.
Electrical terminal connectors are included in the core with finished windings. These components also have a dual purpose. The unitary bobbin's slots have been designed to physically hold the terminal connectors in place.
To electrically tie the windings to the connectors, the terminal connectors can be soldered or other conventionally coupled to the windings.
Each terminal connector has a unique sealing design that stops plastic from flashing out of the mould during the injection process.
The Global molded transformer market accounted for $XX Billion in 2021 and is anticipated to reach $XX Billion by 2030, registering a CAGR of XX% from 2022 to 2030.
The world's first molded big power transformer was created and installed by Cooperative Energy and GE Research at the utility's main substation in Columbia, Mississippi. The substation is a component of a service network that supplies electricity to homes and businesses in Mississippi.
The transformer, which has a 165kV, 60/80/100 MVA rating and was created as part of an ongoing project funded by the Office of Electricity at the U.S. Department of Energy (DOE), and has started a six-month field validation period to evaluate its performance and determine how this new technology might change grid management in the future.
Eaton recently announced the availability of its Breaker Integrated Transformer (BIT), a dry-type low-voltage distribution transformer that incorporates a conventionally separate moulded case circuit breaker (MCCB) inside the same shell.
Eaton's BIT decreases arc-flash risk while reducing physical footprint and overall cost for electrical distribution installations. It arrives factory constructed and completely tested.
The milestone of creating its 100,000th "MOLTRA" moulded transformer was reached by Fuji Electric. The presence of Siemens was crucial in the creation of the moulded transformer by Fuji Electric. The technology for resin-coil moulding is at the core of MOLTRA.
Transformers for static converters, distribution transformers, and power transformers can all be made with Fuji Cast-Resin Transformer (such as VSD : variable-speed drive )
Sl no | Topic |
1 | Market Segmentation |
2 | Scope of the report |
3 | Abbreviations |
4 | Research Methodology |
5 | Executive Summary |
6 | Introduction |
7 | Insights from Industry stakeholders |
8 | Cost breakdown of Product by sub-components and average profit margin |
9 | Disruptive innovation in the Industry |
10 | Technology trends in the Industry |
11 | Consumer trends in the industry |
12 | Recent Production Milestones |
13 | Component Manufacturing in US, EU and China |
14 | COVID-19 impact on overall market |
15 | COVID-19 impact on Production of components |
16 | COVID-19 impact on Point of sale |
17 | Market Segmentation, Dynamics and Forecast by Geography, 2022-2030 |
18 | Market Segmentation, Dynamics and Forecast by Product Type, 2022-2030 |
19 | Market Segmentation, Dynamics and Forecast by Application, 2022-2030 |
20 | Market Segmentation, Dynamics and Forecast by End use, 2022-2030 |
21 | Product installation rate by OEM, 2022 |
22 | Incline/Decline in Average B-2-B selling price in past 5 years |
23 | Competition from substitute products |
24 | Gross margin and average profitability of suppliers |
25 | New product development in past 12 months |
26 | M&A in past 12 months |
27 | Growth strategy of leading players |
28 | Market share of vendors, 2022 |
29 | Company Profiles |
30 | Unmet needs and opportunity for new suppliers |
31 | Conclusion |
32 | Appendix |