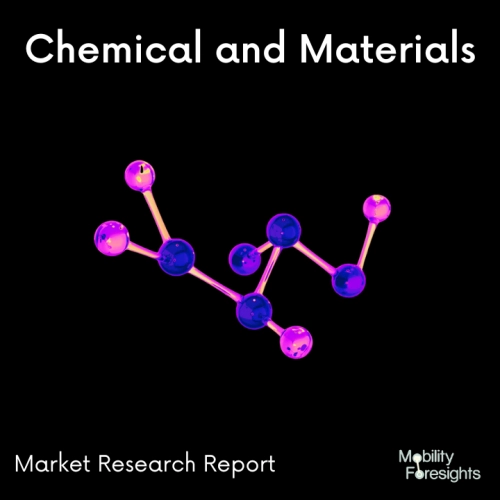
- Get in Touch with Us
Last Updated: Apr 25, 2025 | Study Period: 2024-2030
Molybdenum copper alloy is an alloy composed of molybdenum and copper. The components of these alloys can range from 0.2-50% molybdenum and 99.8-50% copper.
Molybdenum copper alloy is known for its high electrical and thermal conductivity, excellent strength and hardness, good corrosion resistance, and good wear resistance. It also has good machinability, which makes it an ideal material for a wide variety of applications.
Molybdenum copper alloy has been used in many industries, such as aerospace, automotive, electrical/electronic, and medical.
In aerospace, molybdenum copper alloy is used to make aircraft components, such as engine pistons, turbine blades, and other mechanical parts.
In the automotive industry, it is used to make engine components, exhaust systems, brakes, and other automotive parts. In the electrical/electronic industry, molybdenum copper alloy is used to make electrical connectors, switches, and other electrical components.
In the medical field, it is used to make medical components, such as orthopedic implants, surgical instruments, and other medical equipment.
Overall, molybdenum copper alloy is a versatile material with many advantages. It is strong and durable, has excellent thermal and electrical conductivity, and is resistant to corrosion and wear. It is also relatively easy to machine and can be used in a variety of industries.
The Global Molybdenum Copper Alloy Market accounted for $XX Billion in 2023 and is anticipated to reach $XX Billion by 2030, registering a CAGR of XX% from 2024 to 2030.
Researchers at Oak Ridge National Laboratory (ORNL) have created a brand-new molybdenum (Mo) formulation that is specially designed to work with 3D printers that use electron beam melting, or EBM.
Through the use of titanium carbide (TiC) powders and molybdenum, the ORNL team has created a material known as "Mighty Mo," which is able to overcome the alloy's typical brittleness and oxygen reactivity.
The metal matrix composite produced by EBM 3D printing is dense, resistant to cracking, and able to withstand high temperatures, which may make it perfect for use in demanding aerospace applications.
Molybdenum is a refractory metal having a number of qualities that make it a desirable choice for use in extremely temperature-sensitive environments. In addition to having a low thermal expansion coefficient, heat conductivity, and corrosion resistance, the alloy has a high melting point.
Furthermore, molybdenum is highly susceptible to oxygen and nitrogen contamination during processing, which can separate its grain boundaries and lead to partial cracking. To better manage the metal's recrystallization and grain size, scientists have combined it with other materials in the scant study that has already been done in this field, but the results have been mixed results.
Sl no | Topic |
1 | Market Segmentation |
2 | Scope of the report |
3 | Abbreviations |
4 | Research Methodology |
5 | Executive Summary |
6 | Introduction |
7 | Insights from Industry stakeholders |
8 | Cost breakdown of Product by sub-components and average profit margin |
9 | Disruptive innovation in the Industry |
10 | Technology trends in the Industry |
11 | Consumer trends in the industry |
12 | Recent Production Milestones |
13 | Component Manufacturing in US, EU and China |
14 | COVID-19 impact on overall market |
15 | COVID-19 impact on Production of components |
16 | COVID-19 impact on Point of sale |
17 | Market Segmentation, Dynamics and Forecast by Geography, 2024-2030 |
18 | Market Segmentation, Dynamics and Forecast by Product Type, 2024-2030 |
19 | Market Segmentation, Dynamics and Forecast by Application, 2024-2030 |
20 | Market Segmentation, Dynamics and Forecast by End use, 2024-2030 |
21 | Product installation rate by OEM, 2023 |
22 | Incline/Decline in Average B-2-B selling price in past 5 years |
23 | Competition from substitute products |
24 | Gross margin and average profitability of suppliers |
25 | New product development in past 12 months |
26 | M&A in past 12 months |
27 | Growth strategy of leading players |
28 | Market share of vendors, 2023 |
29 | Company Profiles |
30 | Unmet needs and opportunity for new suppliers |
31 | Conclusion |
32 | Appendix |