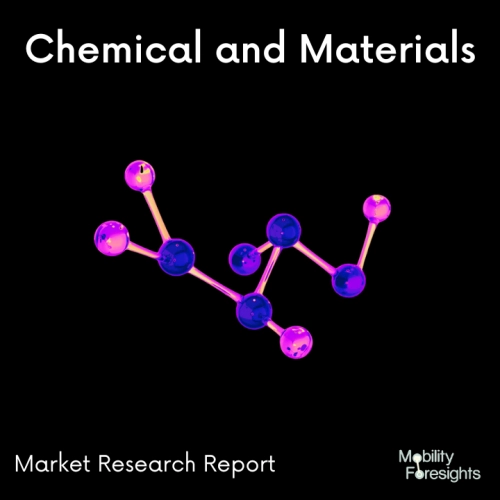
- Get in Touch with Us
Last Updated: Apr 25, 2025 | Study Period: 2024-2030
An electrical tool called a motor starter is used to start and stop a motor securely. The motor starter switches the power ON/OFF similarly to a relay, however unlike a relay, it also offers low voltage and overcurrent protection. An induction motor must be started with a motor starter.
Its low rotor impedance is the cause. The induction motor's slip, or the difference in speed between the rotor and stator, determines the rotor impedance. The slip has an inverse relationship with the impedance.
When an induction motor is at rest, when its slip is at its largest, its impedance is at its lowest, and as a result, it draws a large quantity of current known as inrush current. The air gap between the rotor and stator becomes magnetised due to the strong inrush current, creating an EMF in the rotor winding.
This EMF generates a magnetic field to produce torque in the rotor by producing an electrical current in the rotor winding. The slip of the motor reduces and the current consumed by the motor is reduced as the rotor speed rises. Therefore, such a high current can burn or destroy the motor windings, which would render the machine worthless, and it can create a significant drop in supply line voltage, which can harm other appliances connected to the same line.
Use a starter that limits the initial current for a brief period during beginning in order to protect the motor from such a large quantity of currents. Once the motor reaches a specified speed, the normal power supply to the motor is restarted.
Motors can be turned ON and OFF using the start and stop push buttons attached to the starter and motor. By pressing the stop button, which de-energizes the coil, the contactor coils can be turned off.
In this manner, the motor is switched off as a result of the contactor contacts returning to their natural position due to the spring arrangement. The motor won't start automatically in the event of a power outage or manual switch-off operation; instead, we must manually start the motor by pressing the "start push button."
The operation of a DOL motor starter for ON/OFF operation is shown in the following diagram.
The Global Motor Starter materials market accountedfor $XX Billion in 2023 and is anticipated to reach $XX Billion by 2030, registering a CAGR of XX% from 2024 to 2030.
In so-called full voltage, across-the-line applications, manual motor starters are utilised with small to medium-sized single- and three-phase motors.
A manual motor starter, which consists of an on/off switch and an overload relay, typically does not allow for the disengagement of motor power in the event of a power outage, which might be advantageous for tiny pumps, fans, etc. because they will restart running upon power restoration.
Conveyors, etc., where there is risk from an automatic restart to both equipment and humans, use manual motor starters with under-voltage protection as a way of de-energizing the starter circuit following a power outage. On machine tools, woodworking equipment, etc. where safety regulations require the motor to drop out after a power outage, manual motor starters with under voltage protection are utilised.
Unlike manual starters, which mechanically latch on/off switches, magnetic motor starters use electromagnets to close and retain contactors. They serve as reduced voltage starters for single- and three-phase motors as well as across-the-line applications.
In order to function again when a power outage or low voltage condition causes the contactor to drop off, magnetic motor starters that utilise momentary-contact pilot devices (switches, relays, etc.) must be restarted. If a remote pump is being used, for example, magnetic motor starters can also be linked to restart motors automatically. Magnetic motor starters come in both normal sizes and NEMA and IEC designs.
Sl no | Topic |
1 | Market Segmentation |
2 | Scope of the report |
3 | Abbreviations |
4 | Research Methodology |
5 | Executive Summary |
6 | Introduction |
7 | Insights from Industry stakeholders |
8 | Cost breakdown of Product by sub-components and average profit margin |
9 | Disruptive innovation in the Industry |
10 | Technology trends in the Industry |
11 | Consumer trends in the industry |
12 | Recent Production Milestones |
13 | Component Manufacturing in US, EU and China |
14 | COVID-19 impact on overall market |
15 | COVID-19 impact on Production of components |
16 | COVID-19 impact on Point of sale |
17 | Market Segmentation, Dynamics and Forecast by Geography, 2024-2030 |
18 | Market Segmentation, Dynamics and Forecast by Product Type, 2024-2030 |
19 | Market Segmentation, Dynamics and Forecast by Application, 2024-2030 |
20 | Market Segmentation, Dynamics and Forecast by End use, 2024-2030 |
21 | Product installation rate by OEM, 2023 |
22 | Incline/Decline in Average B-2-B selling price in past 5 years |
23 | Competition from substitute products |
24 | Gross margin and average profitability of suppliers |
25 | New product development in past 12 months |
26 | M&A in past 12 months |
27 | Growth strategy of leading players |
28 | Market share of vendors, 2023 |
29 | Company Profiles |
30 | Unmet needs and opportunity for new suppliers |
31 | Conclusion |
32 | Appendix |