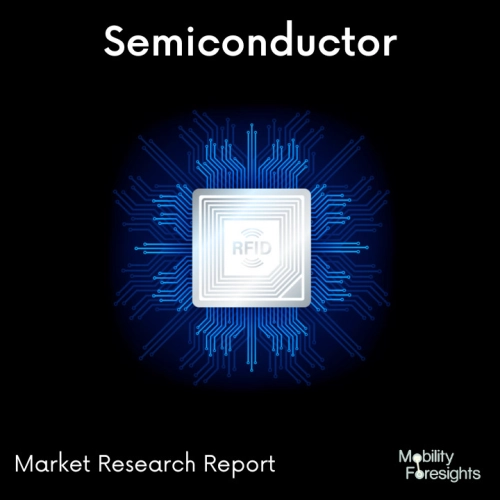
- Get in Touch with Us
Last Updated: Apr 25, 2025 | Study Period: 2023-2030
Physical vapour deposition (PVD) is a technique used to create a thin, incredibly adherent pure metal or alloy layer that can be put on electrically conductive materials.
Using a cathodic arc source and a high vacuum, the procedure is carried out in the vacuum chamber. PVD, or physical vapour deposition, is a common method for creating thin films and surface coatings.
In order to provide coatings with superior qualities, PVD has been widely employed in the industrial setting and has also been coupled with other techniques.
This technology is becoming increasingly effective for creating layers with desired microstructure and features as a result of recent advancements in nanoscience.
The BOEL techniques used in semiconductor production are typically used for MRAM fabrication. The patterning and the dual damascene processes are the two main categories into which the BOWEL process phases are divided.
The necessary wiring system is established in the process flow via patterning. Typically, there are three main components to the dual damascene procedure.
Etching and through dielectric deposition are used to form a diffusion barrier in the first phase, referred to as metallization.
The capping layer and low k-dielectrics, which have lesser dielectric constants than silicon dioxide, are the other two crucial components of the dual damascene method.
Using a physical vapour deposition process, tantalum and tantalum nitrides are used to create the seed and capping layers, respectively.
The Global MRAM Physical Vapour Deposition system market accountedfor $XX Billion in 2021 and is anticipated to reach $XX Billion by 2030, registering a CAGR of XX% from 2022 to 2030.
The first production-ready Integrated Materials Solution for high-volume manufacturing (HVM) of magnetic random-access memory (MRAM) devices is the Applied Endura Clover MRAM PVD system.
MRAM holds the most promise as a replacement for flash memory because its resistance-based operation is more scalable and offers the essential qualities of memory semiconductors: non volatility, random access, and strong endurance.
Flash memory is facing scaling limitations related to its charge-based operation. The Clover system can produce the entire MRAM stack, which can have more than 30 layers and can be up to seven deposition chambers configured with pre-clean, anneal, and cooling chambers as well as on-board metrology. Most of these layers are only a few Angstroms thick and can be produced without a vacuum break.
The vacuum environment maintains the films' quality (which will inevitably deteriorate to some extent if removed from a system during processing), producing high-quality interfaces between layers, lowering the possibility of defects, and improving the accuracy of the metrology that confirms the deposition thickness precision and uniformity necessary for ultimate device performance.
The chamber at the centre of the Endura Clover system may deposit up to five different materials with exceptional regularity. Many of these materials haven't been applied to CMOS technology before.
A spinning shield above the wafer exposes only one target material to plasma bombardment at a time to guarantee that each film is flawless. For the layers to interface effectively and reliably, this is necessary.
Magnesium oxide (MgO), a performance-critical tunnel barrier layer, is deposited in a separate chamber with specialised technology that enables one-step deposition of the material.
By boosting tunnel magnetoresistance, this strengthens the consistency and integrity of the film, reduces defectivity, and enhances the memory read signal (TMR).
The film is further strengthened by further annealing and cryogenic chilling, which also enhance the TMR, reduce resistance to enable low power consumption, and produce excellent thermal stability for improved data retention.
The Endura Clover system includes on-board metrology to measure and monitor the thickness of important layers while the stack is being built because the thickness precision and uniformity requirements for the intricate MRAM stacks are highly strict.
Sl no | Topic |
1 | Market Segmentation |
2 | Scope of the report |
3 | Abbreviations |
4 | Research Methodology |
5 | Executive Summary |
6 | Introduction |
7 | Insights from Industry stakeholders |
8 | Cost breakdown of Product by sub-components and average profit margin |
9 | Disruptive innovation in the Industry |
10 | Technology trends in the Industry |
11 | Consumer trends in the industry |
12 | Recent Production Milestones |
13 | Component Manufacturing in US, EU and China |
14 | COVID-19 impact on overall market |
15 | COVID-19 impact on Production of components |
16 | COVID-19 impact on Point of sale |
17 | Market Segmentation, Dynamics and Forecast by Geography, 2023-2030 |
18 | Market Segmentation, Dynamics and Forecast by Product Type, 2023-2030 |
19 | Market Segmentation, Dynamics and Forecast by Application, 2023-2030 |
20 | Market Segmentation, Dynamics and Forecast by End use, 2023-2030 |
21 | Product installation rate by OEM, 2023 |
22 | Incline/Decline in Average B-2-B selling price in past 5 years |
23 | Competition from substitute products |
24 | Gross margin and average profitability of suppliers |
25 | New product development in past 12 months |
26 | M&A in past 12 months |
27 | Growth strategy of leading players |
28 | Market share of vendors, 2023 |
29 | Company Profiles |
30 | Unmet needs and opportunity for new suppliers |
31 | Conclusion |
32 | Appendix |