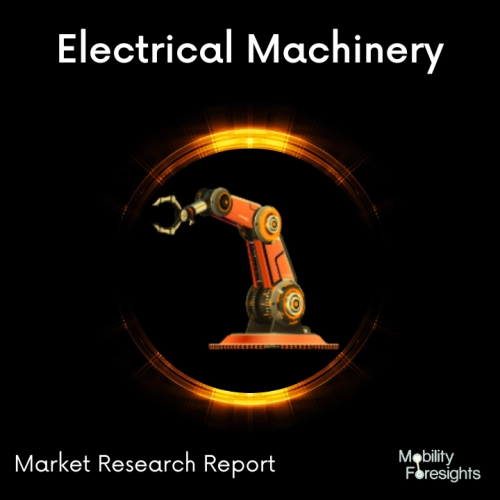
- Get in Touch with Us
Last Updated: Apr 25, 2025 | Study Period: 2024-2030
A BLDC motor controller determines the location of the rotor either sensorlessly or utilising sensors (such as a Hall-effect sensor). The sensors take rotor position measurements and transmit this information.
Direct-current electricity powers a brushless direct current motor (BLDC). Instead of the electromagnets used in induction motors, permanent magnets are employed in BLDC motors. Precision devices frequently employ brushless DC motors. The hard drives found in PCs, DVD players, other PC drives, and Blu-Ray recorders are some prominent examples.
The ability to rotate the disc is crucial for these devices. The spindles that revolve the discs are powered by brushless DC motors. Motion control, linear actuators, servo motors, actuators for industrial robots, extruder drive motors, and feed drives for CNC machine tools are some of the applications for brushless DC motors in industrial engineering.
The Global Multi-Axis BLDC motor controller market accounted for $XX Billion in 2023 and is anticipated to reach $XX Billion by 2030, registering a CAGR of XX% from 2024 to 2030.
Introducing the New Delta Line Multi-Axis BLDC Motor Controller Family: The Phoenix Drive.Phoenix Drive is a new multi-axis brushless DC motor controller by Delta Line that comes in a compact, space-saving design. The sophisticated EtherCAT Phoenix Drive, a compact and useful solution, controls up to 3 motors and is ideal for applications with severe space restrictions.
The next generation of highly integrated motor control systems is represented by the Delta Line Phoenix Drive product line. The Phoenix Drive minimises communication traffic, shrinks controller size, and lowers system costs by executing all real-time crucial operations inside the drive. A cost-effective integrated motion controller, the Phoenix Drive also offers axis synchronisation.
The Phoenix Drive employs the B100 and B500 variants of the EtherCAT high-speed communication protocol. System safeguards include overcurrent, over and undervoltage, overheating, phase-to-phase shorts, and ground shorts are present in both designs. Both 5V encoders and hall effect sensors are used in these drives to operate BLDC motors. STO (Safe Torque Off) and braking output of 1.3 A are features of the B500 Controller.
Electric cars, electric wheelchairs, logistics services and more, Delta Line is a reliable partner. Delta Line has maintained its position as a market leader in mobile motion control applications with the introduction of its highly integrated, small multi-axis Phoenix BLDC Motor Controller family.
1 | Market Segmentation |
2 | Scope of the report |
3 | Abbreviations |
4 | Research Methodology |
5 | Executive Summary |
6 | Introduction |
7 | Insights from Industry stakeholders |
8 | Cost breakdown of Product by sub-components and average profit margin |
9 | Disruptive innovation in the Industry |
10 | Technology trends in the Industry |
11 | Consumer trends in the industry |
12 | Recent Production Milestones |
13 | Component Manufacturing in US, EU and China |
14 | COVID-19 impact on overall market |
15 | COVID-19 impact on Production of components |
16 | COVID-19 impact on Point of sale |
17 | Market Segmentation, Dynamics and Forecast by Geography, 2024-2030 |
18 | Market Segmentation, Dynamics and Forecast by Product Type, 2024-2030 |
19 | Market Segmentation, Dynamics and Forecast by Application, 2024-2030 |
20 | Market Segmentation, Dynamics and Forecast by End use, 2024-2030 |
21 | Product installation rate by OEM, 2023 |
22 | Incline/Decline in Average B-2-B selling price in past 5 years |
23 | Competition from substitute products |
24 | Gross margin and average profitability of suppliers |
25 | New product development in past 12 months |
26 | M&A in past 12 months |
27 | Growth strategy of leading players |
28 | Market share of vendors, 2023 |
29 | Company Profiles |
30 | Unmet needs and opportunity for new suppliers |
31 | Conclusion |
32 | Appendix |