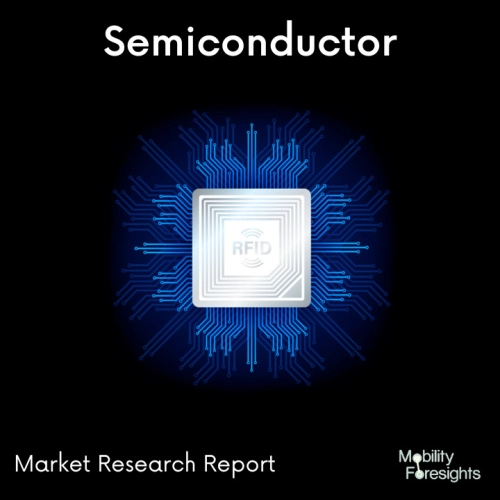
- Get in Touch with Us
Last Updated: Apr 26, 2025 | Study Period: 2023-2030
Test wafers are frequently employed for machine demonstration, process development, and material screening. Test wafers can be produced at a reduced cost and with additional features that are advantageous for the specific application, in contrast to product wafers, which are expensive and difficult to get.
A wafer probe is a system used in the design and production of semiconductors for electrical testing of wafers.Wafer sorting is a straightforward electrical test done on a silicon die while it is still in wafer form. The fundamental goal of wafer sorting is to locate malfunctioning dies and prevent their assembly into packages.
One is the wafer test, which occurs during the wafer process and involves evaluating the electrical properties of chips before slicing a wafer into several semiconductor bits. The other comes after the chopped chips have been packaged during the assembling and testing process.
Standard fault detection and classification (FDC) methods collect features helpful for fault identification from time-indexed measurements of the equipment acquired by in situ sensors and input the extracted data into a classifier to detect wafer flaws, according to an abstract.
Wafer fabrication equipment produces tiny, multi-layer circuits on rounded silicon wafers primarily by physical and chemical methods. Although a variety of tools are employed to carry out these microscopic procedures, the majority of these goods may be divided into a number of basic categories.
The Global Multi-Cell Wafer Testing System market accounted for $XX Billion in 2022 and is anticipated to reach $XX Billion by 2030, registering a CAGR of XX% from 2023 to 2030.
Aehr Test Systems, a global provider of semiconductor production test and reliability qualification equipment, today announced it has received a follow-on production order for an additional FOX-XP multi-wafer test and burn-in system equipped with Aehr's fully integrated and automated WaferPak Aligner from its second major silicon carbide semiconductor customer.
This customer has told us how important automation is to them across their wafer fabrication, assembly, and test, and that our fully integrated FOX-XP with automated Wafer Pak alignment and handling is key to meeting their high volume production needs that are crucial to their scalability, as well as the quality and reliability goals of the customers and markets they serve.
This customer has also praised the cost-effectiveness and scalability of our system. This business will be our lead customer for high volume using our new fully automated WaferPak Aligner integrated with the new FOX-XP wafer level test and burn-in system, and we couldn't be happier about it.
Sl no | Topic |
1 | Market Segmentation |
2 | Scope of the report |
3 | Abbreviations |
4 | Research Methodology |
5 | Executive Summary |
6 | Introduction |
7 | Insights from Industry stakeholders |
8 | Cost breakdown of Product by sub-components and average profit margin |
9 | Disruptive innovation in the Industry |
10 | Technology trends in the Industry |
11 | Consumer trends in the industry |
12 | Recent Production Milestones |
13 | Component Manufacturing in US, EU and China |
14 | COVID-19 impact on overall market |
15 | COVID-19 impact on Production of components |
16 | COVID-19 impact on Point of sale |
17 | Market Segmentation, Dynamics and Forecast by Geography, 2023-2030 |
18 | Market Segmentation, Dynamics and Forecast by Product Type, 2023-2030 |
19 | Market Segmentation, Dynamics and Forecast by Application, 2023-2030 |
20 | Market Segmentation, Dynamics and Forecast by End use, 2023-2030 |
21 | Product installation rate by OEM, 2023 |
22 | Incline/Decline in Average B-2-B selling price in past 5 years |
23 | Competition from substitute products |
24 | Gross margin and average profitability of suppliers |
25 | New product development in past 12 months |
26 | M&A in past 12 months |
27 | Growth strategy of leading players |
28 | Market share of vendors, 2023 |
29 | Company Profiles |
30 | Unmet needs and opportunity for new suppliers |
31 | Conclusion |
32 | Appendix |