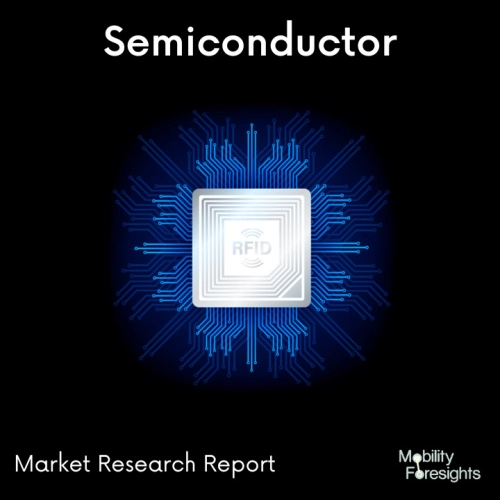
- Get in Touch with Us
Last Updated: Apr 25, 2025 | Study Period: 2023-2030
A multi-chamber sputtering system is a type of physical vapour deposition (PVD) device used to deposit thin films of materials onto a substrate in materials science and engineering.
The system is generally composed of many vacuum chambers linked by a load-lock system, allowing for the deposition of various layers of materials with varying characteristics.
Sputtering involves blasting a target material with high-energy ions, which causes atoms to be expelled off the target material's surface. These atoms then pass through a vacuum and deposit onto the substrate, resulting in the formation of a thin layer.
A multi-chamber sputtering system generally houses the target material in one chamber and the substrate in another. The load-lock mechanism enables the transfer.
A multi-chamber sputtering system's capacity to deposit many layers of materials with various characteristics onto a substrate is one of its primary benefits.
This is critical for the development of complicated materials with specialised features, such as electrical devices, optical coatings, and protective coatings. A multi-layer coating, for example, can be put over a glass substrate to give anti-reflective and scratch-resistant qualities.
Multi-chamber sputtering systems are powerful instruments for thin film deposition with fine control over composition, thickness, and shape. They are widely employed in R&D as well as the manufacturing of innovative materials for a variety of applications.
The Global Multi-Chamber Sputtering System Market accounted for $XX Billion in 2022 and is anticipated to reach $XX Billion by 2030, registering a CAGR of XX% from 2023 to 2030.
ENTRON-EX enables the combination of several cutting-edge techniques such as PVD, CVD, and ALD, as well as the realisation of a simple and resilient In-Situ process.
ENTRON-EX is the newest line-up intended to obtain high productivity from the existing ENTRON-W300/W200 series.
Up to 8 process chambers (PVD, ALD, CVD, etc.) and 2 cool chambers.
Mechanical throughput is 100wph or more when utilising the original new transfer robot from ULVAC.
The ENTRON-EX S-type (single core type) is suited for the mini-fab concept, while the ENTRON-EX T-type (tandem type) is suitable for mass production; both are adaptable to the demands of the client.
The ED-PMS system monitors and manages machine conditions, and the MESEC-BIT no-contact film thickness measuring equipment.
Sl no | Topic |
1 | Market Segmentation |
2 | Scope of the report |
3 | Abbreviations |
4 | Research Methodology |
5 | Executive Summary |
6 | Introdauction |
7 | Insights from Industry stakeholders |
8 | Cost breakdown of Product by sub-components and average profit margin |
9 | Disruptive innovation in theIndustry |
10 | Technology trends in the Industry |
11 | Consumer trends in the industry |
12 | Recent Production Milestones |
13 | Component Manufacturing in US, EU and China |
14 | COVID-19 impact on overall market |
15 | COVID-19 impact on Production of components |
16 | COVID-19 impact on Point of sale |
17 | Market Segmentation, Dynamics and Forecast by Geography, 2023-2030 |
18 | Market Segmentation, Dynamics and Forecast by Product Type, 2023-2030 |
19 | Market Segmentation, Dynamics and Forecast by Application, 2023-2030 |
20 | Market Segmentation, Dynamics and Forecast by End use, 2023-2030 |
21 | Product installation rate by OEM, 2023 |
22 | Incline/Decline in Average B-2-B selling price in past 5 years |
23 | Competition from substitute products |
24 | Gross margin and average profitability of suppliers |
25 | New product development in past 12 months |
26 | M&A in past 12 months |
27 | Growth strategy of leading players |
28 | Market share of vendors, 2023 |
29 | Company Profiles |
30 | Unmet needs and opportunity for new suppliers |
31 | Conclusion |
32 | Appendix |