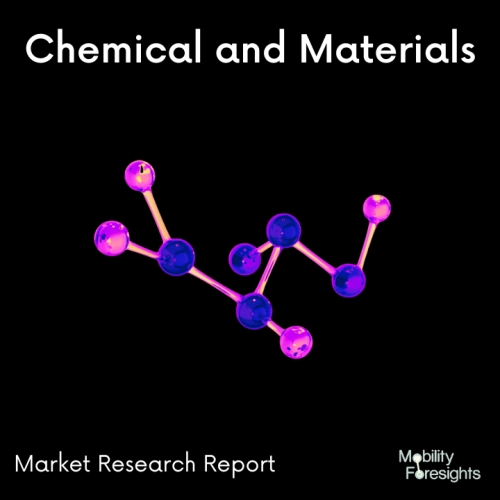
- Get in Touch with Us
Last Updated: Apr 25, 2025 | Study Period: 2023-2030
The method of simultaneously moulding two or more different materials into a single plastic item is known as multi-material injection moulding (MMM).
Similar to standard injection moulding, multi-material injection moulding employs materials that are at or near their melting point in order for the semi-liquid substance to fill holes and cavities within a pre-machined mould and subsequently take on the appropriate shape of designed tooling.
In general, MMM has advantages over other production methods such as, but are not limited to, producing parts with elastic moduli that vary depending on where they are on the part, producing parts with a single structure made of various local materials, and producing a single part with multiple independent polymer colours.
The Global Multi-material Injection Molding Market accounted for $XX Billion in 2022 and is anticipated to reach $XX Billion by 2030, registering a CAGR of XX% from 2023 to 2030.
The X-Type parallel quartet injection moulding machine from FCS Group has four injection units positioned in parallel for a lower footprint. New Multicomponent Injection Molding Machine Line Launched The X-type parallel quartet injection moulding machine has been introduced by Taiwan's FCS Group as a novel multi-component press technology.
The initial product, the GW-1600R, is a two-platen multi-component offering and is a part of FCS's expansive 2K machine range. One machine has already been supplied to a Chinese automotive light provider.
According to FCS, multi-material machines are increasingly in demand from headlamp providers as the functionality of headlights is being enhanced in size, precision, and stability and as 50% of the headlamps now supplied for cars use a halogen and LED combination.
The X-type parallel quartet multi-component injection machine was introduced by FCS in response to this rising demand. The X-type quartet-injection solution is more concentrated and has a smaller footprint than the prior L-type quartet-injection solution.
Its four injection units can be used with a variety of moulds, allowing it to make two-, three-, and four-component products with great flexibility.
On the fixed mould side of the machine, the four injection units are positioned parallel. Their compact design and adaptable architecture enable the press to be rearranged for shaping a variety of items. Depending on the needs of the mould, the injection units can be chosen.
Without moving or modifying the injection units, two, three, and four component items can be formed. The device has a highly accurate servo rotary table that can be turned to fit various angles and tasks.
It also has rapid operation and precise placement. According to FCS, it will continue to expand the line's tonnages in the future.
Sl no | Topic |
1 | Market Segmentation |
2 | Scope of the report |
3 | Abbreviations |
4 | Research Methodology |
5 | Executive Summary |
6 | Introduction |
7 | Insights from Industry stakeholders |
8 | Cost breakdown of Product by sub-components and average profit margin |
9 | Disruptive innovation in the Industry |
10 | Technology trends in the Industry |
11 | Consumer trends in the industry |
12 | Recent Production Milestones |
13 | Component Manufacturing in US, EU and China |
14 | COVID-19 impact on overall market |
15 | COVID-19 impact on Production of components |
16 | COVID-19 impact on Point of sale |
17 | Market Segmentation, Dynamics and Forecast by Geography, 2023-2030 |
18 | Market Segmentation, Dynamics and Forecast by Product Type, 2023-2030 |
19 | Market Segmentation, Dynamics and Forecast by Application, 2023-2030 |
20 | Market Segmentation, Dynamics and Forecast by End use, 2023-2030 |
21 | Product installation rate by OEM, 2023 |
22 | Incline/Decline in Average B-2-B selling price in past 5 years |
23 | Competition from substitute products |
24 | Gross margin and average profitability of suppliers |
25 | New product development in past 12 months |
26 | M&A in past 12 months |
27 | Growth strategy of leading players |
28 | Market share of vendors, 2023 |
29 | Company Profiles |
30 | Unmet needs and opportunity for new suppliers |
31 | Conclusion |
32 | Appendix |