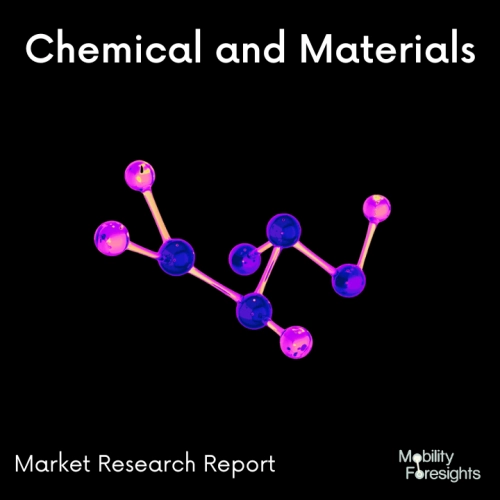
- Get in Touch with Us
Last Updated: Apr 25, 2025 | Study Period: 2024-2030
The self-fluxing alloy powders are used most frequently in nickel-based alloys. It has outstanding all-around performance, low stress abrasive wear resistance, heat resistance, corrosion resistance, oxidation resistance, and good impact toughness.
Strong wetting capacity for a variety of substrates and WC particles, low melting point, wide solid-liquid temperature range, and simple operation. It has good self-fluxing, wettability and spray welding qualities.
High hardness, corrosion resistance, wear resistance, heat resistance, and difficulty in cutting are all qualities of the spray welding layer. It is best to grind wet.
It can be used for welding with an oxygen-acetylene flame or plasma spray, and it's frequently used to maintain and repair sliding wear-resistant elements like rolling mill conveyor rollers, cams, plungers, and wire drawing drums that are resistant to corrosion and wear.
TheGlobal Nickel based alloy powder marketaccounted for $XX Billion in 2023 and is anticipated to reach $XX Billion by 2030, registering a CAGR of XX% from 2024 to 2030.
The manufacture of high-quality nickel and cobalt metal from lateritic ore is a field in which Sherritt International is widely regarded as a global leader. The welding and galvanising industries both use nickel powders because of their high density and wide range of particle sizes.
This nickel powder works well in the fine chemical, plating, and battery industries. It is also produced with the chemical dissolving business in mind. There are several different particle size distributions of nickel powder available.
Sl no | Topic |
1 | Market Segmentation |
2 | Scope of the report |
3 | Abbreviations |
4 | Research Methodology |
5 | Executive Summary |
6 | Introduction |
7 | Insights from Industry stakeholders |
8 | Cost breakdown of Product by sub-components and average profit margin |
9 | Disruptive innovation in the Industry |
10 | Technology trends in the Industry |
11 | Consumer trends in the industry |
12 | Recent Production Milestones |
13 | Component Manufacturing in US, EU and China |
14 | COVID-19 impact on overall market |
15 | COVID-19 impact on Production of components |
16 | COVID-19 impact on Point of sale |
17 | Market Segmentation, Dynamics and Forecast by Geography, 2024-2030 |
18 | Market Segmentation, Dynamics and Forecast by Product Type, 2024-2030 |
19 | Market Segmentation, Dynamics and Forecast by Application, 2024-2030 |
20 | Market Segmentation, Dynamics and Forecast by End use, 2024-2030 |
21 | Product installation rate by OEM, 2023 |
22 | Incline/Decline in Average B-2-B selling price in past 5 years |
23 | Competition from substitute products |
24 | Gross margin and average profitability of suppliers |
25 | New product development in past 12 months |
26 | M&A in past 12 months |
27 | Growth strategy of leading players |
28 | Market share of vendors, 2023 |
29 | Company Profiles |
30 | Unmet needs and opportunity for new suppliers |
31 | Conclusion |
32 | Appendix |