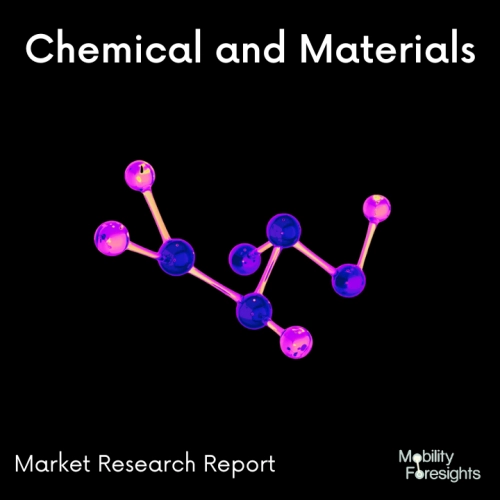
- Get in Touch with Us
Last Updated: Apr 25, 2025 | Study Period: 2023-2030
The most well-known of these is alloy C-276 (N10276), which has a strong resistance to corrosion. In terms of resistance to reducing acids like hydrochloric and sulfuric, they excel. In order to increase the corrosion resistance to more oxidising or more reducing circumstances, a variety of variants based on this composition have adjusted the Cr and Mo levels and, in some cases, added Cu or W.
For usage in high pressure and temperature applications, chrome-molybdenum alloy steel, often known as chrome moly, is employed. Because of its tensile strength, high temperature resistance, and corrosion resistance, it is utilised in the oil and gas, energy, construction, and automotive industries.
The Global Nickel Chromium Molybdenum Alloy Market accounted for $XX Billion in 2022 and is anticipated to reach $XX Billion by 2030, registering a CAGR of XX% from 2023 to 2030.
The alloy Inconel 62-5, which is composed of nickel, chromium, and molybdenum, has a limited resistance to reducing acids but exhibits good resistance to nitric and phosphoric acids as well as a number of chloride salts. Pitting, chloride stress corrosion cracking, and corrosion fatigue are all greatly reduced.
It can be used in the as-welded form since it also resists sensitization and intergranular corrosion. Pitting corrosion resistance, high corrosion-fatigue strength, high tensile strength, and resistance to chloride ion stress corrosion cracking are all characteristics of Inconel 625 that make it appropriate.
This nickel-chromium-molybdenum alloy with low molybdenum is typically used for steam line components, propeller blades, submarine fittings and wire for mooring cables in marine environments.
Comparing Hastelloy C22 to other NiCrMo alloys, it offers good overall corrosion resistance and adaptability. The creation of improved alloys like Hastelloy C22 was made possible by a better knowledge of the function that chromium, molybdenum, and tungsten play in providing corrosion resistance to nickel base alloys.
Hastelloy C22, which contains almost equal amounts of nickel, chromium, molybdenum, tungsten, and iron, has the lowest corrosion rate of the majority of nickel base alloys now in use in both oxidising and reducing environments.
It also has the strongest resistance to pitting and crevice corrosion. Hastelloy C22 is reported to have greater thermal stability than Hastelloy C276 which has a higher molybdenum and tungsten percentage.
Sl no | Topic |
1 | Market Segmentation |
2 | Scope of the report |
3 | Abbreviations |
4 | Research Methodology |
5 | Executive Summary |
6 | Introduction |
7 | Insights from Industry stakeholders |
8 | Cost breakdown of Product by sub-components and average profit margin |
9 | Disruptive innovation in the Industry |
10 | Technology trends in the Industry |
11 | Consumer trends in the industry |
12 | Recent Production Milestones |
13 | Component Manufacturing in US, EU and China |
14 | COVID-19 impact on overall market |
15 | COVID-19 impact on Production of components |
16 | COVID-19 impact on Point of sale |
17 | Market Segmentation, Dynamics and Forecast by Geography, 2023-2030 |
18 | Market Segmentation, Dynamics and Forecast by Product Type, 2023-2030 |
19 | Market Segmentation, Dynamics and Forecast by Application, 2023-2030 |
20 | Market Segmentation, Dynamics and Forecast by End use, 2023-2030 |
21 | Product installation rate by OEM, 2023 |
22 | Incline/Decline in Average B-2-B selling price in past 5 years |
23 | Competition from substitute products |
24 | Gross margin and average profitability of suppliers |
25 | New product development in past 12 months |
26 | M&A in past 12 months |
27 | Growth strategy of leading players |
28 | Market share of vendors, 2023 |
29 | Company Profiles |
30 | Unmet needs and opportunity for new suppliers |
31 | Conclusion |
32 | Appendix |