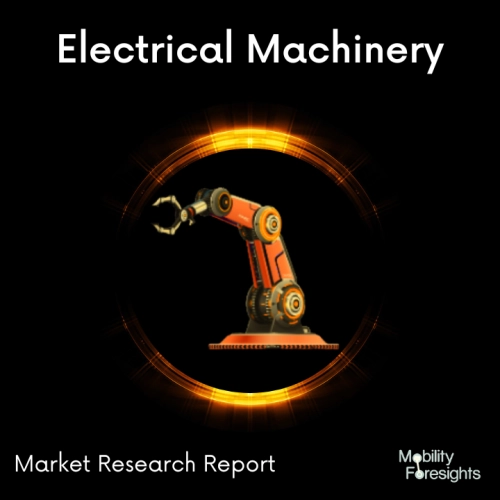
- Get in Touch with Us
Last Updated: Apr 25, 2025 | Study Period: 2023-2030
Cutting tools are instruments used to chip away material from a workpiece. Drilling, milling, turning, and grinding are just a few of the manufacturing and machining operations they are utilised in. The effectiveness and calibre of the machining process depend greatly on the choice of cutting tools.
Having a blade at the end of the shank, a cutting tool is a particular kind of cutting tool. The blade is made of ceramics, high-speed tool steel, cemented carbide, diamond/CBN, cermet, and cemented carbide.You may get the material's desired form and size by removing the excess material.
In general, there are two ways to cut: rolling, in which the workpiece is restrained while the tools rotate, and turning, in which the workpiece is turned instead.
Single-edge cutting tools are constructed from a range of hardened metal alloys that are ground to a certain shape in order to execute a specific component of the turning process, culminating in a final machined product.
Single-edge cutting tools are mostly employed in lathe turning operations, and their size and alloy composition vary depending on the size and kind of material being turned.
The Nigeria Cutting tools market accounted for $XX Billion in 2022 and is anticipated to reach $XX Billion by 2030, registering a CAGR of XX% from 2023 to 2030.
The Launch of Newly Developed Cutting Tools to Achieve High Efficiency Machining AC5005S New coated grade for turning of difficult-to-cut materials.To reduce lead times and the cost of producing machine parts, there is a growing need to increase the manufacturing efficiency and extend the tool life of cutting tools.
This section introduces three new cutting tool products that meet these needs and achieve high efficiency manufacturing.
This insert grade is perfect for machining difficult-to-cut materials such as Ni (nickel) base alloys, Co (cobalt) base alloys, and Ti (titanium) alloys, which are often used in the aerospace and medical sectors because to their excellent heat and corrosion resistance.
Tool change frequency and tool usage are decreased, resulting in lower tool costs, thanks to 1.5 times more efficiency in machining difficult-to-cut materials than ordinary grades.
Sl no | Topic |
1 | Market Segmentation |
2 | Scope of the report |
3 | Abbreviations |
4 | Research Methodology |
5 | Executive Summary |
6 | Introduction |
7 | Insights from Industry stakeholders |
8 | Cost breakdown of Product by sub-components and average profit margin |
9 | Disruptive innovation in the Industry |
10 | Technology trends in the Industry |
11 | Consumer trends in the industry |
12 | Recent Production Milestones |
13 | Component Manufacturing in US, EU and China |
14 | COVID-19 impact on overall market |
15 | COVID-19 impact on Production of components |
16 | COVID-19 impact on Point of sale |
17 | Market Segmentation, Dynamics and Forecast by Geography, 2023-2030 |
18 | Market Segmentation, Dynamics and Forecast by Product Type, 2023-2030 |
19 | Market Segmentation, Dynamics and Forecast by Application, 2023-2030 |
20 | Market Segmentation, Dynamics and Forecast by End use, 2023-2030 |
21 | Product installation rate by OEM, 2023 |
22 | Incline/Decline in Average B-2-B selling price in past 5 years |
23 | Competition from substitute products |
24 | Gross margin and average profitability of suppliers |
25 | New product development in past 12 months |
26 | M&A in past 12 months |
27 | Growth strategy of leading players |
28 | Market share of vendors, 2023 |
29 | Company Profiles |
30 | Unmet needs and opportunity for new suppliers |
31 | Conclusion |
32 | Appendix |