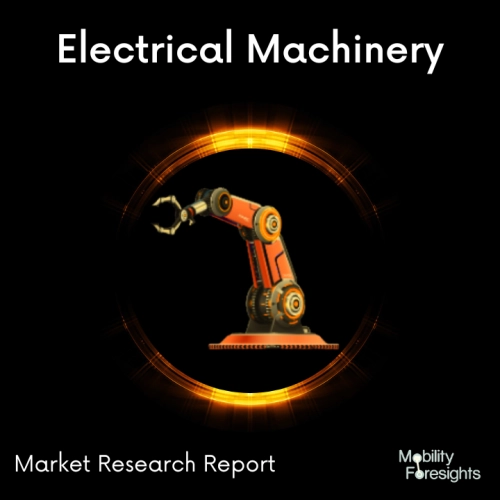
- Get in Touch with Us
Last Updated: Apr 25, 2025 | Study Period: 2023-2030
Crankshaft or camshaft grinding, as well as grinding cam parts of various diameters, are typical applications. All non-rotationally symmetric geometries can be ground on each machine, both for internal and external machining.
Grinding machines can be used for both mass production and prototype work.The work head has two clamping fixtures and is double.
It can rotate 180 degrees to a clearly defined end position. A fully automated technique is used to move the workpiece from its original loading position to the grinding location.
In order to decrease downtime, the second workpiece simultaneously moves from the grinding position to the discharge position.
The workpiece is held between two grinding wheels while they rotate in the same direction at various speeds during centerless grinding.
In order to apply downward force to the workpiece, one grinding wheel spins around a fixed axis. Typically, this wheel grinds the workpiece by moving at a faster linear speed than the workpiece at the point of contact.
The other movable wheel, which traps the workpiece with either a rough or rubber-bonded abrasive, is positioned to exert lateral pressure to it.
The Global non-cylindrical grinding machine market accounted for $XX Billion in 2022 and is anticipated to reach $XX Billion by 2030, registering a CAGR of XX% from 2023 to 2030.
Modern technology and unique design principles are the foundations of JUNKER non-cylindrical grinding machines. The adaptable and effective machine designs enable the most productive and high-quality machining in the shortest amount of time.
Innovative measurement systems are used by each machine before, during, and after the grinding operation. To ensure that it only creates high-quality parts, the machine, in particular, incorporates data from in-process measurements into the grinding process in real time.
Any difference in the measured data, no matter how slight, can be quickly examined and fixed. Even while operating continuously, grinding machines consistently produce the best workpiece quality due to their great static and thermal stability.
For consistently providing flawless grinding results, integrated cooling systems and flexible clamping, driving, and support choices offer the essential fundamental conditions.
Operation and maintenance are equally straightforward as flexible connection to automation systems or simple integration in industrial lines.
Sl no | Topic |
1 | Market Segmentation |
2 | Scope of the report |
3 | Abbreviations |
4 | Research Methodology |
5 | Executive Summary |
6 | Introduction |
7 | Insights from Industry stakeholders |
8 | Cost breakdown of Product by sub-components and average profit margin |
9 | Disruptive innovation in the Industry |
10 | Technology trends in the Industry |
11 | Consumer trends in the industry |
12 | Recent Production Milestones |
13 | Component Manufacturing in US, EU and China |
14 | COVID-19 impact on overall market |
15 | COVID-19 impact on Production of components |
16 | COVID-19 impact on Point of sale |
17 | Market Segmentation, Dynamics and Forecast by Geography, 2023-2030 |
18 | Market Segmentation, Dynamics and Forecast by Product Type, 2023-2030 |
19 | Market Segmentation, Dynamics and Forecast by Application, 2023-2030 |
20 | Market Segmentation, Dynamics and Forecast by End use, 2023-2030 |
21 | Product installation rate by OEM, 2023 |
22 | Incline/Decline in Average B-2-B selling price in past 5 years |
23 | Competition from substitute products |
24 | Gross margin and average profitability of suppliers |
25 | New product development in past 12 months |
26 | M&A in past 12 months |
27 | Growth strategy of leading players |
28 | Market share of vendors, 2023 |
29 | Company Profiles |
30 | Unmet needs and opportunity for new suppliers |
31 | Conclusion |
32 | Appendix |