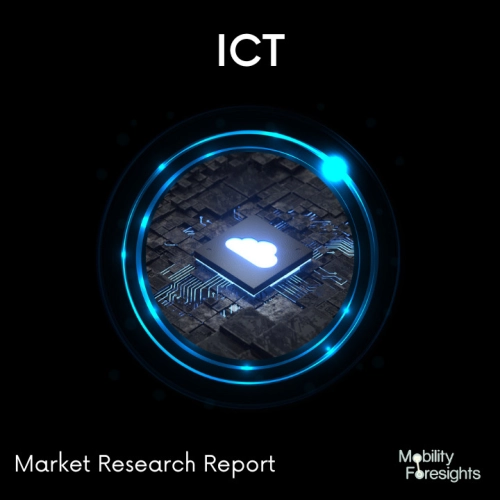
- Get in Touch with Us
Last Updated: Apr 25, 2025 | Study Period: 2024-2030
Non-destructive testing (NDT) is a testing and analysis technique used by industry to evaluate the properties of a material, component, structure or system for characteristic differences or welding defects and discontinuities without causing damage to the original part.
Non-destructive testing (NDT) camera is used to detect, inspect, and measure flaws, bond integrity, and other material conditions without permanently altering or destroying the examined part or product. NDT equipment includes a wide variety of instruments and systems.
Non-destructive testing (NDT)camera is a camera and analysis technique used by industry to evaluate the properties of a material, component, structure or system for characteristic differences or welding defects and discontinuities without causing damage to the original part.
NDT also known as non-destructive examination (NDE), non-destructive inspection (NDI) and non-destructive evaluation (NDE). This testing method uses an electric current or magnetic field which is passed through a conductive part.
There are three types of electromagnetic testing, includingeddy current testing,alternating current field measurement (ACFM)and remote field testing (RFT).
Eddy current testing uses an alternating current coil to induce an electromagnetic field into the test piece,alternating current field measurementand remote field testing both use a probe to introduce a magnetic field, with RFT generally used to test pipes.
The Global Non-destructive testing camera market accounted for $XX Billion in 2023 and is anticipated to reach $XX Billion by 2030, registering a CAGR of XX% from 2024 to 2030.
FLIR Non-destructive testing camer - FLIR cameras with Lock-In, Transient, and Pulse capability can perform advanced inspections such as Non-Destructive Testing (NDT) or stress mapping, resolving temperature differences as low as 1 mK.
NDT is widely used to evaluate the properties of a material, component, or system without causing damage. IR cameras can detect internal defects through target excitation and the observation of thermal differences on a target's surface.
Thermal imaging is a valuable tool for detecting defects and points of failure in composites, solar cells, bridges, and electronics. It is also a great tool for thermal mapping of stress when performing materials testing.
Sl no | Topic |
1 | Market Segmentation |
2 | Scope of the report |
3 | Abbreviations |
4 | Research Methodology |
5 | Executive Summary |
6 | Introduction |
7 | Insights from Industry stakeholders |
8 | Cost breakdown of Product by sub-components and average profit margin |
9 | Disruptive innovation in the Industry |
10 | Technology trends in the Industry |
11 | Consumer trends in the industry |
12 | Recent Production Milestones |
13 | Component Manufacturing in US, EU and China |
14 | COVID-19 impact on overall market |
15 | COVID-19 impact on Production of components |
16 | COVID-19 impact on Point of sale |
17 | Market Segmentation, Dynamics and Forecast by Geography, 2024-2030 |
18 | Market Segmentation, Dynamics and Forecast by Product Type, 2024-2030 |
19 | Market Segmentation, Dynamics and Forecast by Application, 2024-2030 |
20 | Market Segmentation, Dynamics and Forecast by End use, 2024-2030 |
21 | Product installation rate by OEM, 2023 |
22 | Incline/Decline in Average B-2-B selling price in past 5 years |
23 | Competition from substitute products |
24 | Gross margin and average profitability of suppliers |
25 | New product development in past 12 months |
26 | M&A in past 12 months |
27 | Growth strategy of leading players |
28 | Market share of vendors, 2023 |
29 | Company Profiles |
30 | Unmet needs and opportunity for new suppliers |
31 | Conclusion |
32 | Appendix |