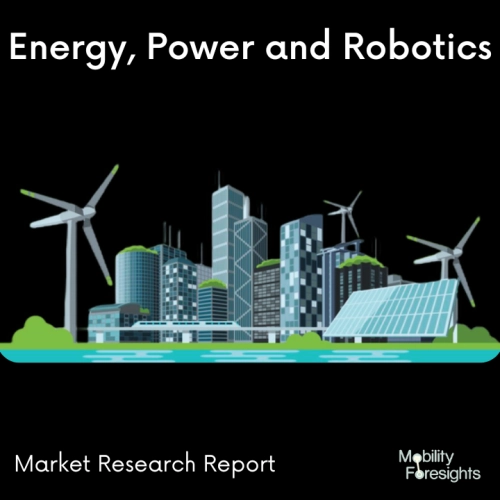
- Get in Touch with Us
Last Updated: Apr 25, 2025 | Study Period: 2024-2030
Nuclear Reactor Pressure vessel inspections can refer to an inspection of the vessel's condition externally, internally, or both. In these inspections, inspectors may: Collect visual data regarding the condition of the vessel, including the condition of insulation, welds, joints, or structural connections.
Reactor pressure vessels are thick steel containers that hold nuclear fuel when the reactors operate. The vessels provide one of several barriers that keep radioactive material out of the environment.
There is a legal requirement for thorough examination of pressure vessels and receivers that contain steam, compressed air and refrigerants. Any pressure vessel containing compressed gas over two fifty bar / litres capacity requires inspection.
The extent of the test or examination should be that necessary to determine that the pressure vessel's condition is satisfactory and that the pressure vessel is fit for the service in- tended.
The Global Nuclear Reactor Pressure Vessel Inspection System market accounted for $XX Billion in 2023 and is anticipated to reach $XX Billion by 2030, registering a CAGR of XX% from 2024 to 2030.
Southwest research institute NUCLEAR REACTOR PRESSURE VESSEL INSPECTION SYSTEMSwRI has developed nuclear reactor pressure vessel materials and welding processes for over thirty years. They have also conducted nuclear power plant inspections around the world.
This expertise led SwRI to develop a system for periodic in-service inspections of pressurized water reactor (PWR) vessels used in nuclear power production. Also known as reactor pressure vessels (RPV), these structures are welded with heavy-duty metal to contain nuclear reactor coolant and a reactor core under high pressures.
Mechanical inspection system is aimed at minimizing human exposure to radiation. It provides ultrasonic inspection of welds in pressure vessels and related piping with the following: Mechanized scanner ; Ultrasonic transducers ; Attachments to fit the various geometries of the vessel and nozzles ; Enhanced data acquisition system (EDAS) and analysis equipment.
Sl no | Topic |
1 | Market Segmentation |
2 | Scope of the report |
3 | Abbreviations |
4 | Research Methodology |
5 | Executive Summary |
6 | Introduction |
7 | Insights from Industry stakeholders |
8 | Cost breakdown of Product by sub-components and average profit margin |
9 | Disruptive innovation in the Industry |
10 | Technology trends in the Industry |
11 | Consumer trends in the industry |
12 | Recent Production Milestones |
13 | Component Manufacturing in US, EU and China |
14 | COVID-19 impact on overall market |
15 | COVID-19 impact on Production of components |
16 | COVID-19 impact on Point of sale |
17 | Market Segmentation, Dynamics and Forecast by Geography, 2024-2030 |
18 | Market Segmentation, Dynamics and Forecast by Product Type, 2024-2030 |
19 | Market Segmentation, Dynamics and Forecast by Application, 2024-2030 |
20 | Market Segmentation, Dynamics and Forecast by End use, 2024-2030 |
21 | Product installation rate by OEM, 2023 |
22 | Incline/Decline in Average B-2-B selling price in past 5 years |
23 | Competition from substitute products |
24 | Gross margin and average profitability of suppliers |
25 | New product development in past 12 months |
26 | M&A in past 12 months |
27 | Growth strategy of leading players |
28 | Market share of vendors, 2023 |
29 | Company Profiles |
30 | Unmet needs and opportunity for new suppliers |
31 | Conclusion |
32 | Appendix |