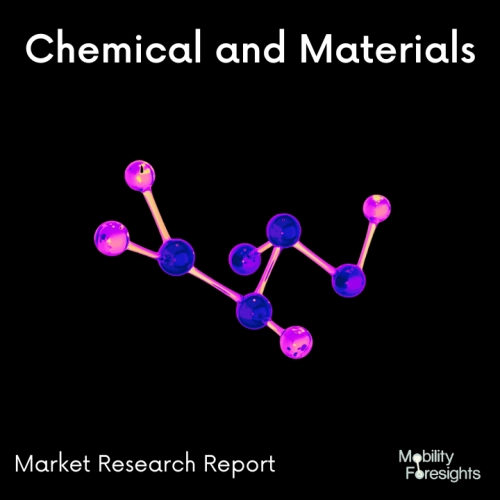
- Get in Touch with Us
Last Updated: Apr 25, 2025 | Study Period: 2024-2030
The global nylon film market is characterized by robust growth driven primarily by the increasing demand for flexible and durable packaging solutions across various industries. Nylon films are widely utilized in applications such as food packaging, pharmaceuticals, agriculture, industrial goods, and consumer products due to their excellent mechanical strength, barrier properties, and versatility. The market is witnessing rapid technological advancements in material science and production processes, leading to the development of thinner, lighter, and more sustainable nylon films with enhanced gas barrier capabilities.
Asia-Pacific dominates the polyamide nylon (OPA) films market, fueled by expanding economies, urbanization, and the rising preference for packaged food products. North America and Europe also contribute significantly to market growth, driven by stringent regulatory standards and increasing adoption of high barrier packaging solutions in pharmaceuticals and electronics. Key challenges include fluctuating raw material costs, competitive market dynamics, and the imperative for manufacturers to align with sustainability goals. Despite these challenges, the global nylon film market presents ample opportunities for investment in innovation, sustainability initiatives, and technological advancements to meet evolving consumer demands and regulatory requirements.
Nylon is a family ofsynthetic polymerswithamidebackbones, usually linkingaliphaticorsemi-aromaticgroups.Nylons are white or colorless and soft; some aresilk-like.They arethermoplastic, which means that they can be melt-processed into fibers,films, and diverse shapes.The properties of nylons are often modified by blending with a wide variety of additives.
Many kinds of nylon are known. One family, designated nylon-XY, is derived fromdiaminesanddicarboxylic acidsof carbon chain lengths X and Y, respectively. An important example is nylon-6,6. Another family, designated nylon-Z, is derived from amino carboxylic acids with carbon chain length Z. An example is nylon-.Nylon polymers have significant commercial applications infabricand fibers (apparel, flooring and rubber reinforcement), in shapes (molded parts for cars, electrical equipment, etc.), and in films (mostly forfood packaging).
Global Nylon Film Market was valued at $XX Billion in 2023 and is projected to reach $XX Billion by 2030, reflecting a compound annual growth rate (CAGR) of XX% from 2024 to 2030.
Enhanced Barrier Properties: Innovations focus on improving barrier properties against oxygen, moisture, and other gasses to extend shelf life and preserve product quality in packaging applications.
Advanced Processing Techniques:Continued development of processing techniques such as co-extrusion, biaxial orientation, and nanotechnology to achieve thinner films with enhanced mechanical and barrier properties.
Bio-based and Sustainable Materials: Increasing demand for bio-based nylons and sustainable alternatives to conventional petroleum-based nylons, driven by environmental concerns and regulatory pressures.
Functional Additives: Integration of functional additives such as antimicrobial agents, UV stabilizers, and anti-static agents to enhance performance and meet specific application requirements.
NY-Clear
NYCOA had launched NY-Clear, an amorphous 6I/6T nylon, targeted for packaging and precision molded applications transparent nylon offered high clarity and strong permeation resistance with up to 30% higher resistance on oxygen, CO2, and water vapor transmission over competitive solutions in the market. They had exhibited higher temperature resistance, and lower moisture absorption, and had "better" retention of properties compared to nylon 6 and nylon 66. NY-Clear was also used in higher-temperature applications such as oven bags. Amorphous nylons were known for their dimensional stability, high Tg, heat deflection temperature (HDT), low creep at elevated temperatures, and good chemical resistance compared to many high-performance engineering plastics. NYCOAâs NY-Clear portfolio consisted of grades that were optimized for injection molding components with high dimensional stability and gloss as well as grades optimized for blown film and extrusion applications.
HiDura LUX
Ascend Performance Materials introduced HiDura LUX, an amorphous nylon aimed at flexible packaging films. HiDura Lux served as a specialty modifier blended with other polyamides to enhance various performance properties crucial for packaging: The product had enhanced thermoforming capabilities and improved orientation for optimized shrink performance. It had improved optical properties, including higher gloss and lower haze. HiDura LUX had provided increased organoleptic performance and acted as an effective oxygen barrier, extending product shelf-life and preventing food spoilage in applications such as shrink films for protein packaging, thermoforming films, and barrier layers for fiberboard packaging.
Ultimus
Merck had launched Ultimus Single-Use Process Container Film, aimed at providing exceptional durability and leak resistance for single-use assemblies used in bioprocessing liquid applications. The film was designed with a proprietary woven nylon structure to enhance bag strength, durability, and resilience, crucial for maintaining product quality and sterility in bioprocessing operations. Ultimus film had undergone rigorous testing, demonstrating superior performance compared to other single-use bioprocessing films. It offered 10 times greater abrasion resistance, 2.8 times greater tensile strength, and twice the puncture strength. The film also provided an animal origin-free contact resin with a low extractable profile, supporting healthy cell growth performance. This cutting-edge technology was made available in Merckâs Mobius 3D process containers, providing a robust and durable solution that enhanced operational efficiency and minimized disruptions in bioprocessing.
Sr.No | Topic |
1 | Market Segmentation |
2 | Scope of the report |
3 | Research Methodology |
4 | Executive Summary |
5 | Average B2B by price |
6 | Introduction |
7 | Insights from Industry stakeholders |
8 | Key Drivers forGlobal Nylon Film Market |
9 | Disruptive Innovation in the Industry |
10 | Overview of Global Nylon Film Market |
11 | Major impact on Technological advancements |
12 | Consumer trends in the industry |
13 | Recent technological trends in Tactical wideband High Frequency radio market |
14 | SWOT Analysis of Key Market Players |
15 | New product development in the past 12 months |
16 | Market Size, Dynamics, and Forecast by Geography , 2024-2030 |
17 | Market Size, Dynamics, and Forecast by Product Type , 2024-2030 |
18 | Market Size, Dynamics, and Forecast by Application, 2024-2030 |
19 | Market Size, Dynamics, and Forecast by End User, 2024-2030 |
20 | Competitive landscape |
21 | Gross margin and average profitability of suppliers |
22 | Merger and Acquisition in the past 12 months |
23 | Growth strategy of leading players |
24 | Market share of vendors, 2023 |
25 | Market Company Profiles |
26 | Unmet needs and opportunities for new suppliers |
27 | Conclusion |