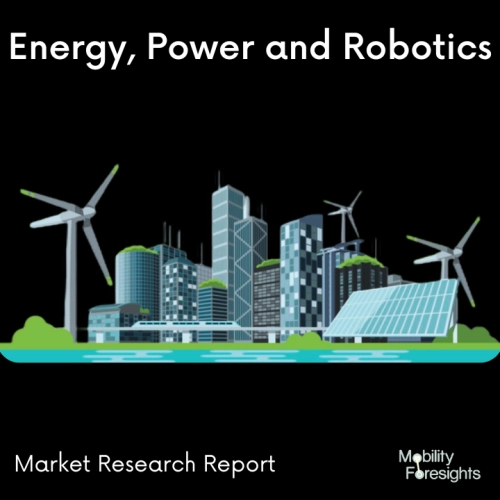
- Get in Touch with Us
Last Updated: Apr 25, 2025 | Study Period: 2023-2030
Heat-shrink tubing, also known as heat shrink or heatshrink, is a plastic tube that can be shrunk and is used to protect connections, joints, and terminals in electrical wiring by insulating stranded and solid wire conductors from abrasion and the elements.
Additionally, it may be used to make cable entrance seals that provide environmental sealing protection, to create bundles of wires or replace the insulation on wires, to shield wires or small parts from light abrasion, and more.
Typically composed of polyolefin, heat-shrink tubing shrinks radially (but not longitudinally) when heated, to a diameter of half to one-sixth of its original size.
Heat shrink tubing is a frequent component in most electrical setups because it protects electrical components from external influences such as moisture, dust, abrasion, and sharp objects, which may otherwise damage cables and electrical components. This form of degradation eventually leads to shorts and failures.
The Oman Heat shrink tubing market accounted for $XX Billion in 2022 and is anticipated to reach $XX Billion by 2030, registering a CAGR of XX% from 2023 to 2030.
Custom VCI Shrink Film Opens New Doors of Opportunity for Metals Packaging in Automated Heat Shrink Tunnels.Heavy duty packing of industrial equipment and assets being readied for transport or storage commonly uses VpCI-126 Shrink Film.
Phase of vapour Corrosion On metal surfaces inside the packaging, inhibitors in the film create a shielding molecular layer to prevent corrosion.
Standard VpCI-126 Shrink Film is made to withstand abrasion in layup or industrial export circumstances. As a result, it is heavy and needs to be applied by hand.
On the opposite end of the shrink film packaging range, consumer items that are automatically heated shrunk are often packed in very fragile films and don't typically need corrosion protection. Smaller metal industrial components that might benefit from automated packaging and corrosion prevention fall in between these two extremes.
Such was the situation when a business attempted to package oil filters for industrial equipment in their automated heat seal tunnel. The metal shell of the filters required corrosion protection, especially considering that some will be exported outside to Southeast Asia.
However, because it did not seal properly, the generic VCI (Vapour Corrosion Inhibitor) film they were employing was continuously generating issues. The client had to routinely run the filters through the heat seal tunnel again because the VCI bags were opening, creating a significant quantity of plastic waste.
Cortec created a special type of VpCI-126 Shrink Film tubing that was suitable with the mechanical machinery since standard VpCI-126 Shrink Film would have been too heavy to pass through the automated heat-seal line.
The test run worked well; the bags held their seals, and the customer didn't need to halt the packing machinery until there were no more oil filters to bag. The film sealed fast and easily, and shrink-wrapping was an alternative if preferred.
Following the trial's success, the client made the decision to use VpCI-126 Shrink Film for all of its VCI film packaging requirements.
Sl no | Topic |
1 | Market Segmentation |
2 | Scope of the report |
3 | Abbreviations |
4 | Research Methodology |
5 | Executive Summary |
6 | Introduction |
7 | Insights from Industry stakeholders |
8 | Cost breakdown of Product by sub-components and average profit margin |
9 | Disruptive innovation in the Industry |
10 | Technology trends in the Industry |
11 | Consumer trends in the industry |
12 | Recent Production Milestones |
13 | Component Manufacturing in US, EU and China |
14 | COVID-19 impact on overall market |
15 | COVID-19 impact on Production of components |
16 | COVID-19 impact on Point of sale |
17 | Market Segmentation, Dynamics and Forecast by Geography, 2023-2030 |
18 | Market Segmentation, Dynamics and Forecast by Product Type, 2023-2030 |
19 | Market Segmentation, Dynamics and Forecast by Application, 2023-2030 |
20 | Market Segmentation, Dynamics and Forecast by End use, 2023-2030 |
21 | Product installation rate by OEM, 2023 |
22 | Incline/Decline in Average B-2-B selling price in past 5 years |
23 | Competition from substitute products |
24 | Gross margin and average profitability of suppliers |
25 | New product development in past 12 months |
26 | M&A in past 12 months |
27 | Growth strategy of leading players |
28 | Market share of vendors, 2023 |
29 | Company Profiles |
30 | Unmet needs and opportunity for new suppliers |
31 | Conclusion |
32 | Appendix |