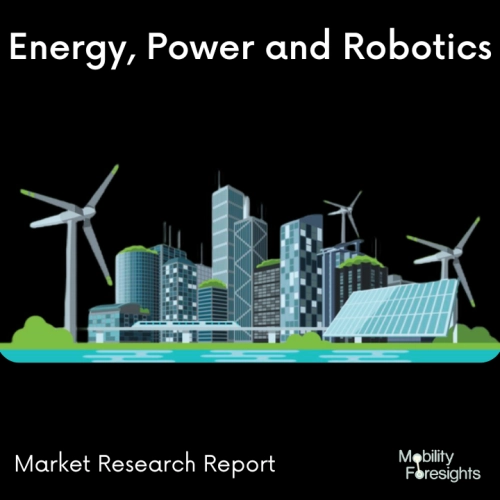
- Get in Touch with Us
Last Updated: Apr 25, 2025 | Study Period: 2023-2030
A tiny turbine with an organic Rankine cycle employs a low boiling point organic fluid as its working fluid rather of water or steam and has a design that is identical to that of a steam turbine. A condenser and a heat exchanger are included in a closed cycle system that houses the turbine.
An Organic Rankine Cycle (ORC) system is a closed thermodynamic cycle utilised for small-medium applications at any temperature level and power generation from low to medium-high temperature heat sources ranging from 80 to 400°C.
The organic Rankine cycle is comparable to the Rankine steam cycle but instead of using water as the working fluid, utilises an organic fluid such as refrigerants or hydrocarbons. In a typical Rankine cycle, thermal energy is used to turn water into steam, which then expands via a turbine to produce electricity.
The ORC can help many industrial processes meet their goals for reducing their carbon footprint (waste heat recovery, biomass). The Rankine architecture-based thermodynamic cycles can exploit low, medium, and high enthalpy fluxes from renewable resources (solar, geothermal, etc.), thanks to the ORC.
The following benefits are offered by the ORC file format: Effective compression: Data is compressed and stored in columns, which reduces the amount of disc reads. In Tez, vectorization optimizations work best in the columnar format.
The Global Organic Rankine Cycle Power System Market accounted for $XX Billion in 2022 and is anticipated to reach $XX Billion by 2030, registering a CAGR of XX% from 2023 to 2030.
DEmonstrator of Industrial CArbon-Free Power Generation from ORC-based Waste-Heat-to-Energy Systems is the "DECAGONE" project.The solution is based on the Organic Rankine Cycle (ORC) technology and was created by a group of 16 partners from 10 different European nations.
It will increase cost-effectiveness, allow for a wider range of input temperatures, and significantly reduce system size, enabling a wider adoption of heat recovery and its conversion to electricity from more industrial processes. It will also be scalable to greater power levels. A 2 MW installation at the TINECKÃ ELEZRNY steel mill in the Czech Republic will be used to demonstrate the solution.
The ORC-based system will make use of innovative turbomachinery and improved heat recovery solutions. The proposed turbine's ground-breaking architecture is designed to boost capacity, improve availability and safety, save costs, and require almost no maintenance.
Additionally, the consortium will enhance organic mixes or fluids for greater stability and better transferability to other sectors. With the help of cutting-edge probes, the Internet of Things (IoT), and machine learning algorithms, the project ensures an effective and clever integration of enhanced monitoring for improving efficiency in real-time.
In industrial facilities, the potential for self-consumption on a significant industrial scale will be completely realised.
Sl no | Topic |
1 | Market Segmentation |
2 | Scope of the report |
3 | Abbreviations |
4 | Research Methodology |
5 | Executive Summary |
6 | Introduction |
7 | Insights from Industry stakeholders |
8 | Cost breakdown of Product by sub-components and average profit margin |
9 | Disruptive innovation in the Industry |
10 | Technology trends in the Industry |
11 | Consumer trends in the industry |
12 | Recent Production Milestones |
13 | Component Manufacturing in US, EU and China |
14 | COVID-19 impact on overall market |
15 | COVID-19 impact on Production of components |
16 | COVID-19 impact on Point of sale |
17 | Market Segmentation, Dynamics and Forecast by Geography, 2023-2030 |
18 | Market Segmentation, Dynamics and Forecast by Product Type, 2023-2030 |
19 | Market Segmentation, Dynamics and Forecast by Application, 2023-2030 |
20 | Market Segmentation, Dynamics and Forecast by End use, 2023-2030 |
21 | Product installation rate by OEM, 2023 |
22 | Incline/Decline in Average B-2-B selling price in past 5 years |
23 | Competition from substitute products |
24 | Gross margin and average profitability of suppliers |
25 | New product development in past 12 months |
26 | M&A in past 12 months |
27 | Growth strategy of leading players |
28 | Market share of vendors, 2023 |
29 | Company Profiles |
30 | Unmet needs and opportunity for new suppliers |
31 | Conclusion |
32 | Appendix |