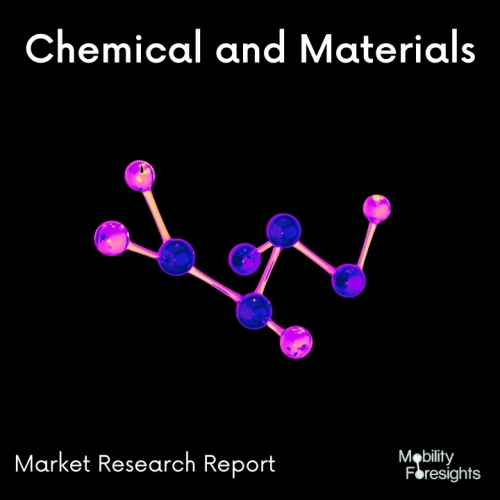
- Get in Touch with Us
Last Updated: Apr 26, 2025 | Study Period: 2024-2030
The xylene family of hydrocarbons includes the colorless, aromatic hydrocarbon known as paraxylene, commonly referred to as p-xylene. Along with o-xylene and m-xylene, it is one of the three isomers of xylene.
It is principally used to make dimethyl terephthalate (DMT) and terephthalic acid (TPA), two essential intermediates in the creation of polyethylene terephthalate (PET) plastics.
Commercial production of xylene involves a number of different procedures, the most popular of which is the catalytic reforming of petroleum naphtha. In this procedure, paraxylene and other xylenes are produced by subjecting naphtha, a light hydrocarbon fraction generated from crude oil, to high temperatures and pressure in the presence of a catalyst. T
hrough alternate methods like coal gasification or biomass gasification, xylene can also be generated from coal or biomass sources.With the majority of its global production going toward the creation of PET, propylene has a number of significant industrial uses.
Thermoplastic polyester known as PET is a versatile material that is frequently used in a variety of industries, including packaging, fabrics, fibers, films, and bottles. In order to create terephthalic acid or dimethyl terephthalate, which are both used as the building blocks for the PET polymerization process, paraxylene must first undergo oxidation.
To accommodate the various requirements of industries and customers, the resulting PET resin can be molded into varied forms and shapes.There are few other industries that employ paraxylene outside those that produce PET. The chemical industry occasionally uses it as a solvent because of its good solubility characteristics.
In the synthesis of other chemicals, such as phthalic anhydride, which is used to make plasticizers and colors, it is also employed as a feedstock. Paraxylene can also be oxidized to produce pure terephthalic acid (PTA), which is a crucial ingredient in the creation of polyester fibers for fabrics and carpets.
Nevertheless, while having a wide range of uses, paraxylene raises some health and environmental issues. It is classified as a volatile organic compound (VOC) and, when released into the atmosphere, can help produce smog and ground-level ozone. Long-term contact with high amounts of paraxylene vapor or liquid can also irritate the eyes, skin, and respiratory system.
As a result, during its production, handling, and storage, certain safety precautions and control measures are required.The research and development of environmentally acceptable and sustainable paraxylene substitutes have received increasing attention in recent years.
To lessen dependency on feedstocks derived from fossil fuels, numerous research projects are being conducted to investigate bio-based approaches for the manufacture of terephthalic acid and associated intermediates.
The requirement for new paraxylene production is also being decreased through recycling and circular economy activities that support the reuse and recycling of PET polymers.
In conclusion, paraxylene is an essential chemical utilized mostly in the manufacture of PET plastics, making it a key component of the petrochemical industry. It has numerous uses in the fields of packaging and textiles, and it is a vital part of the contemporary economy.
In an effort to reduce the environmental impact of the manufacture of paraxylene, efforts are being undertaken to investigate alternate feedstocks and recyclingtechniques.
The Global Paraxylene Market accounted for $XX Billion in 2023 and is anticipated to reach $XX Billion by 2030, registering a CAGR of XX% from 2024 to 2030.
A total of 10 million tones of new paraxylene production facilities are being built in China. Paraxylene is a chemical used to create synthetic bottles and textile fiber. Leading exporters in South Korea, Japan, and the Middle East may be forced to reduce production as early as the second quarter of the following year as a result of the new PX capacity.
China is the biggest consumer of paraxylene in the world, importing 60% of what it requires to meet its more than doubling demand for polyester. China imports more than half of its PX from South Korea and Japan.
With 10 million tones, that is three times as much as Japan and equal to South Korea's whole PX industry. China might increase its chemical production capacity by 14 million tones annually between 2020 and 2023, with the majority of its factories being connected with sizable crude oil refineries.
Reliance Industries Ltd. (RIL), an oil refiner, has announced the successful commissioning of the 2.2 million tonnes per year (MMTPA) first phase of the paraxylene (PX) plant at its Jamnagar petrochemicals complex in Gujarat. According to the firm, the plant uses cutting-edge crystallization technology from BP and is extremely energy and environmentally friendly.
A new paraxylene crystallization facility will be opened by Sonagraph in Northern Africa. A new paraxylene crystallization unit is almost finished at Sonagraph's integrated refinery/petrochemical site in Sikka, Algeria, which is recognized by Forbes as the world's 12th largest oil business.
The central processing units of the plant will use GT-Isomax and Crisp, both licensed from GTC Technology. While GT-Isomax isomerizes C8 aromatics into extra paraxylene using the ISOXYL catalyst from Clariant, Crisp recovers paraxylene from reformate feedstock.
The license also covers the extraction of aromatics and other aromatics processes, as well as naphtha hydrotreating and reforming. For the new facilities, Samsung Engineering Co., Ltd. offered EPC services. The paraxylene factory was formerly a part of Nitec, a Sonagraph petrochemical division.
The new units are part of Sonagraph's long-term expansion plans to increase the capacity of its facilities in Algeria for petrochemical and refining operations in order to fulfill the rising domestic demand for oil products.
Sl no | Topic |
1 | Market Segmentation |
2 | Scope of the report |
3 | Abbreviations |
4 | Research Methodology |
5 | Executive Summary |
6 | Introduction |
7 | Insights from Industry stakeholders |
8 | Cost breakdown of Product by sub-components and average profit margin |
9 | Disruptive innovation in the Industry |
10 | Technology trends in the Industry |
11 | Consumer trends in the industry |
12 | Recent Production Milestones |
13 | Component Manufacturing in US, EU and China |
14 | COVID-19 impact on overall market |
15 | COVID-19 impact on Production of components |
16 | COVID-19 impact on Point of sale |
17 | Market Segmentation, Dynamics and Forecast by Geography, 2024-2030 |
18 | Market Segmentation, Dynamics and Forecast by Product Type, 2024-2030 |
19 | Market Segmentation, Dynamics and Forecast by Application, 2024-2030 |
20 | Market Segmentation, Dynamics and Forecast by End use, 2024-2030 |
21 | Product installation rate by OEM, 2023 |
22 | Incline/Decline in Average B-2-B selling price in past 5 years |
23 | Competition from substitute products |
24 | Gross margin and average profitability of suppliers |
25 | New product development in past 12 months |
26 | M&A in past 12 months |
27 | Growth strategy of leading players |
28 | Market share of vendors, 2023 |
29 | Company Profiles |
30 | Unmet needs and opportunity for new suppliers |
31 | Conclusion |
32 | Appendix |