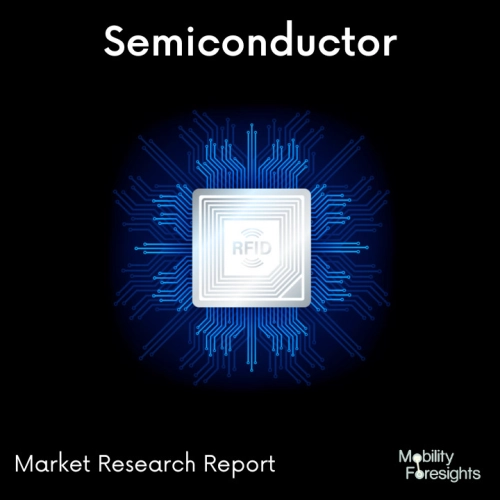
- Get in Touch with Us
Last Updated: Apr 26, 2025 | Study Period: 2023-2030
Patterned wafer inspection system can therefore detect defects by comparing the pattern images of adjacent chips (also called dies) and obtaining the difference. The pattern on the wafer is captured along the die array by electron beam or light.
patterned silicon wafer is produced using a process called photolithography. A puddle is a shaped silicon puddle. This puddle is etched using a chemical called a chemical etching solution.
It is made by removing a layer of crystalline silicon. In this way, the amorphous puddle is a patterned sludge.The progression to ever smaller wafer feature sizes produces lower and lower tolerance to defects in both starting materials and finished devices.
Not only are we approaching near zero tolerances to known defect types (particles, crystal defects, etc.), but manufacturers continue to discover device sensitivities to entirely new types of defects as manufacturing progresses into the deep nano-scale.
Global patterned wafer inspection system market accounted for $XX Billion in 2022 and is anticipated to reach $XX Billion by 2030, registering a CAGR of XX% from 2023 to 2030.
Hitachi High-Tech Launches Dark Field Wafer Defect Inspection System DI2800, Achieving High-Sensitivity 100% Inspection for Semiconductor Devices in the IoT and Automotive Fields.
Hitachi High-Tech Corporation ("Hitachi High-Tech") today announced the launch of the Hitachi Dark Field Wafer Defect Inspection System DI2800, a critical component in any semiconductor manufacturerâs metrology capabilities.
The DI2800 is a high-speed metrology system designed to identify defects and particles on patterned wafers up to 8 inches (200 mm) in diameter.
With its high throughput and performance, the DI2800 can help ensure device reliability and safety, particularly for highly sensitive applications such as Internet of Things (IoT) and automotive fields where 100% inspection is required.
Hitachi High-Tech has developed Dark Field Wafer Defect Inspection System DI2800 to respond to these market needs.
This product uses scattering-intensity simulation technology to optimize the illumination and detection optics, enabling highly sensitive inspection of patterned-wafer defects developed during the manufacturing process. It has a detection sensitivity of 0.1-μm standard particle size on mirrored wafers.
This performance is even possible on devices as small as 0.3-mm square, which has previously proved challenging due to sensitivity and data processing limitations. With a highly optimised inspection sequence, the DI2800 is capable of throughputs of over 40 200-mm wafers per hour
Sl no | Topic |
1 | Market Segmentation |
2 | Scope of the report |
3 | Abbreviations |
4 | Research Methodology |
5 | Executive Summary |
6 | Introduction |
7 | Insights from Industry stakeholders |
8 | Cost breakdown of Product by sub-components and average profit margin |
9 | Disruptive innovation in the Industry |
10 | Technology trends in the Industry |
11 | Consumer trends in the industry |
12 | Recent Production Milestones |
13 | Component Manufacturing in US, EU and China |
14 | COVID-19 impact on overall market |
15 | COVID-19 impact on Production of components |
16 | COVID-19 impact on Point of sale |
17 | Market Segmentation, Dynamics and Forecast by Geography, 2023-2030 |
18 | Market Segmentation, Dynamics and Forecast by Product Type, 2023-2030 |
19 | Market Segmentation, Dynamics and Forecast by Application, 2023-2030 |
20 | Market Segmentation, Dynamics and Forecast by End use, 2023-2030 |
21 | Product installation rate by OEM, 2023 |
22 | Incline/Decline in Average B-2-B selling price in past 5 years |
23 | Competition from substitute products |
24 | Gross margin and average profitability of suppliers |
25 | New product development in past 12 months |
26 | M&A in past 12 months |
27 | Growth strategy of leading players |
28 | Market share of vendors, 2023 |
29 | Company Profiles |
30 | Unmet needs and opportunity for new suppliers |
31 | Conclusion |
32 | Appendix |