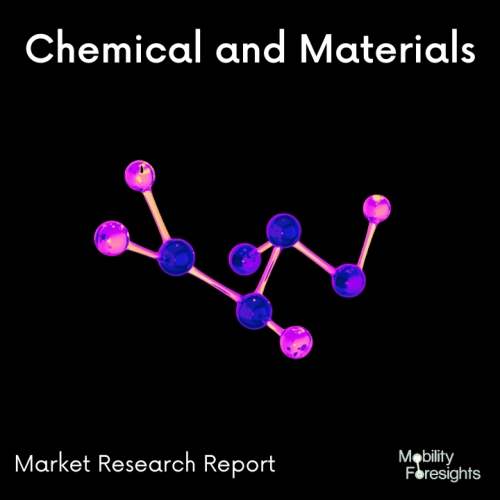
- Get in Touch with Us
Last Updated: Apr 25, 2025 | Study Period: 2024-2030
A molding process is used to make cell phone cases, which are precisely developed. During the injection molding process, molten plastic material is forced into a mold cavity located in the mold base using a ram or screw-type plunger. As a result, the mobile phone case's shape, which was molded to fit its contours, becomes more stable.
The plastic is injected under high pressure into the mold in order to form it into the desired shape. A manufacturing technique called injection molding uses material that is injected into a mold to create pieces.
The Global Phone Case Injection Molding Machine market accounted for $XX Billion in 2023 and is anticipated to reach $XX Billion by 2030, registering a CAGR of XX% from 2024 to 2030.
A set of mobile phone shells is developed through a variety of steps, including structural design, mold creation, injection molding production, spray printing, etc., all of which have an impact on the finished product's look. Polycarbonate or PC+ABS is typically used in the construction of cell phone casings.
Due to PC's poor fluidity, the filling process often uses high mold and material temperatures; the gates utilized are typically point gates. Graded injection molding must be used when filling.
Finding the gate's location and the V-P (injection-holding pressure) switch setting would be very helpful in resolving irregularities like gate gas markings and underfill flash.
Numerous elements, including the size of the injection molding machine, the screw arrangement, the design of the mold and the molded product, and the molding cycle length, all affect the ideal injection molding temperature setting.
A lower temperature is typically set in the rear section/feeding zone of the material pipe and a higher temperature is set in the front portion of the material pipe in order to gradually melt the plastic.
It is also possible to set the temperature in reverse, though, if the screw design is flawed or the L/D value is too small. Regarding mold temperature, high-temperature molds can produce molded goods that are thinner or longer and have better surface appearance, less residual stress, and are simpler to fill. The short injection molding cycle can be caused by the low mold temperature.
Sl no | Topic |
1 | Market Segmentation |
2 | Scope of the report |
3 | Abbreviations |
4 | Research Methodology |
5 | Executive Summary |
6 | Introduction |
7 | Insights from Industry stakeholders |
8 | Cost breakdown of Product by sub-components and average profit margin |
9 | Disruptive innovation in the Industry |
10 | Technology trends in the Industry |
11 | Consumer trends in the industry |
12 | Recent Production Milestones |
13 | Component Manufacturing in US, EU and China |
14 | COVID-19 impact on overall market |
15 | COVID-19 impact on Production of components |
16 | COVID-19 impact on Point of sale |
17 | Market Segmentation, Dynamics and Forecast by Geography, 2024-2030 |
18 | Market Segmentation, Dynamics and Forecast by Product Type, 2024-2030 |
19 | Market Segmentation, Dynamics and Forecast by Application, 2024-2030 |
20 | Market Segmentation, Dynamics and Forecast by End use, 2024-2030 |
21 | Product installation rate by OEM, 2023 |
22 | Incline/Decline in Average B-2-B selling price in past 5 years |
23 | Competition from substitute products |
24 | Gross margin and average profitability of suppliers |
25 | New product development in past 12 months |
26 | M&A in past 12 months |
27 | Growth strategy of leading players |
28 | Market share of vendors, 2023 |
29 | Company Profiles |
30 | Unmet needs and opportunity for new suppliers |
31 | Conclusion |
32 | Appendix |