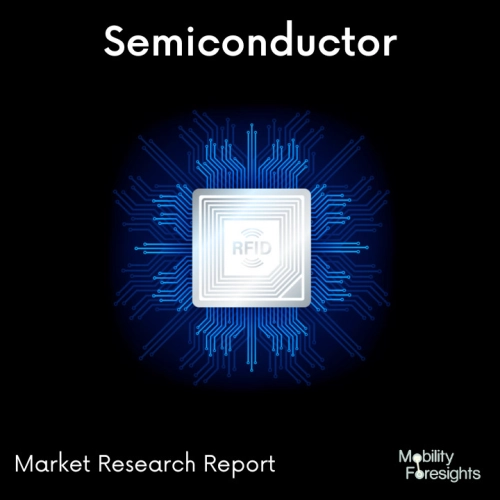
- Get in Touch with Us
Last Updated: Apr 25, 2025 | Study Period: 2023-2030
Due to the fact that they transmit the integrated circuit layouts to the wafers, photomasks are a crucial component in semiconductor fabrication.
It is crucial that the lithographic pattern on the photomask is accurately reproduced. A chrome metal pattern serves as the absorbing coating on translucent fused silica photomasks, which are the norm. However, photomasks have also been created for other wavelengths, including X-rays and the very-ultraviolet.
On its Mask Etcher Series platform, Plasma-Therm provides mask etch technology. Highly developed etching technologies have been made possible by the photomasks' extraordinarily low tolerance for pattern error. Plasma etching uniformity adjustments can be used to correct mistakes in the initial photomask lithography.
An opaque plate having transparent regions that let light pass through in a certain pattern is referred to as a photomask. In order to create a pattern on a tiny wafer of material for the fabrication of integrated circuits (ICs or "chips"), photomasks are frequently employed in photolithography (usually silicon).
Each mask is applied in turn, replicating a layer of the final design, and together they are referred to as a mask set.
The master image of one layer of the chip was created by manually peeling off the undesirable rubylith after the design of one layer had been cut into the rubylith, first by hand on a lit drafting table and then by machine plotter.
Larger and larger rubyliths were required for increasingly sophisticated and therefore larger chips, eventually filling an entire room wall.
As the size of the feature shrunk, the image could only be adequately focused by being brought into physical contact with the wafer.
It was necessary to clean or discard the photoresist that these contact aligners frequently lifted from the wafer and onto the photomask.
This prompted the usage of reverse master photomasks (see above), which were used to make the numerous actual working photomasks required through contact photolithography and etching.
Later, projection photo-lithography allowed for an infinite lifespan for the photomask. Even later, photomasks were no longer necessary because of direct-step-on-wafer stepper photo-lithography, which used reticles instead.
The Global Photomask Etch system market accountedfor $XX Billion in 2021 and is anticipated to reach $XX Billion by 2030, registering a CAGR of XX% from 2022 to 2030.
In order to etch the next-generation optical lithographic photomasks required by the industry to continue multiple patterning scaling to the node and beyond, Applied Materials today launched the Applied Centura Tetra Z Photomask Etch system.
By providing angstrom-level photomask accuracy for critical dimension (CD) characteristics necessary to achieve demanding patterning criteria for future logic and memory devices, the new tool expands the capabilities of Applied's market-leading Tetra platform.
For advanced chrome, MoSi, hard mask, and quartz etch applications needed to create advanced binary and phase-shift masks, Applied created the Tetra Z tool (PSMs).
The device extends immersion lithography for quadruple patterning and cutting-edge resolution improvement techniques, providing ongoing technical advances and exceptional CD performance.
Uniform, linear precision etching with almost negligible defectivity across all feature sizes and pattern densities is a crucial capability for maintaining pattern transfer integrity.
For sophisticated chromium, hard mask, molybdenum silicon oxynitride (MoSi), and quartz (fused silica) etch applications used to create advanced binary and phase-shift masks, Applied created the Tetra Z tool (PSMs).
The device extends immersion lithography for quadruple patterning and cutting-edge resolution improvement techniques, providing ongoing technical advances and exceptional CD performance.
Uniform, linear precision etching with almost negligible defectivity across all feature sizes and pattern densities is a crucial capability for maintaining pattern transfer integrity.
For smaller photomask CD patterns on crucial device layers, thinner resist films can be used thanks to excellent CD performance and strong etch selectivity.
Sl no | Topic |
1 | Market Segmentation |
2 | Scope of the report |
3 | Abbreviations |
4 | Research Methodology |
5 | Executive Summary |
6 | Introduction |
7 | Insights from Industry stakeholders |
8 | Cost breakdown of Product by sub-components and average profit margin |
9 | Disruptive innovation in the Industry |
10 | Technology trends in the Industry |
11 | Consumer trends in the industry |
12 | Recent Production Milestones |
13 | Component Manufacturing in US, EU and China |
14 | COVID-19 impact on overall market |
15 | COVID-19 impact on Production of components |
16 | COVID-19 impact on Point of sale |
17 | Market Segmentation, Dynamics and Forecast by Geography, 2023-2030 |
18 | Market Segmentation, Dynamics and Forecast by Product Type, 2023-2030 |
19 | Market Segmentation, Dynamics and Forecast by Application, 2023-2030 |
20 | Market Segmentation, Dynamics and Forecast by End use, 2023-2030 |
21 | Product installation rate by OEM, 2023 |
22 | Incline/Decline in Average B-2-B selling price in past 5 years |
23 | Competition from substitute products |
24 | Gross margin and average profitability of suppliers |
25 | New product development in past 12 months |
26 | M&A in past 12 months |
27 | Growth strategy of leading players |
28 | Market share of vendors, 2023 |
29 | Company Profiles |
30 | Unmet needs and opportunity for new suppliers |
31 | Conclusion |
32 | Appendix |