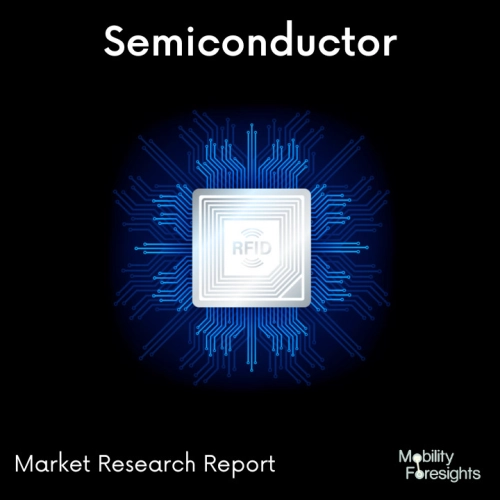
- Get in Touch with Us
Last Updated: Apr 25, 2025 | Study Period: 2024-2030
This translates into complete in-die measuring capacity for registration and crucial dimensions along with demanding standards for repeatability and accuracy in the context of photomask metrology. Particularly, overlay becomes increasingly important and must be guaranteed on every die.
An opaque plate having transparent regions that let light pass through in a certain pattern is referred to as a photomask.
In order to create a pattern on a tiny wafer of material for the fabrication of integrated circuits (ICs or "chips"), photomasks are frequently employed in photolithography (usually silicon).
Photomask metrology's image positioning is still a key component. Features for a single mask, which represents one layer in an entire semiconductor design, must also adhere to strict specifications regarding position accuracy. To create a gadget that works, the entire mask set for all layers must match.
The most challenging layers in terms of crucial dimensions now require the separation into independent layouts and overlaying of each other due to the emergence of multi-pattering schemes.
These tasks call for the use of registration metrology technologies with exceptional standards of reproducibility and accuracy for precise picture positioning measurements.
Global photomask registration metr accounted for $XX Billion in 2023 and is anticipated to reach $XX Billion by 2030, registering a CAGR of XX% from 2024 to 2030.
Zeiss' next-generation photomask registration and overlay metrology technology has reached a significant development milestone, according to a recent announcement from Sematech and the Semiconductor Metrology Systems (SMS) subsidiary of Carl Zeiss.
For the 32-nm node and lower, the jointly developed technology, dubbed Prove, displayed enhanced photomask measurement capability. The crucial requirementsâ0.5-nm repeatability and 1.0-nm accuracy in image positioning, registration, and overlay measurementâwere confirmed through a series of test runs.
The Carl Zeiss SMS and Sematech relationship for prior work on mask Aerial Image Metrology Systems (AIMS) tool platforms forms the foundation of the mask pattern placement metrology tool project.
A working metrology instrument that satisfies requirements for repeatability, reproducibility, and precision at the 32-nm half-pitch node is the product of the partnership.
The ITRS states that the requirements for advanced memory and double-exposure/double-patterning mask pattern placement and overlay that will aid in extending 193-nm lithography were the driving forces behind the tool's performance goals.
Sl no | Topic |
1 | Market Segmentation |
2 | Scope of the report |
3 | Abbreviations |
4 | Research Methodology |
5 | Executive Summary |
6 | Introduction |
7 | Insights from Industry stakeholders |
8 | Cost breakdown of Product by sub-components and average profit margin |
9 | Disruptive innovation in the Industry |
10 | Technology trends in the Industry |
11 | Consumer trends in the industry |
12 | Recent Production Milestones |
13 | Component Manufacturing in US, EU and China |
14 | COVID-19 impact on overall market |
15 | COVID-19 impact on Production of components |
16 | COVID-19 impact on Point of sale |
17 | Market Segmentation, Dynamics and Forecast by Geography, 2024-2030 |
18 | Market Segmentation, Dynamics and Forecast by Product Type, 2024-2030 |
19 | Market Segmentation, Dynamics and Forecast by Application, 2024-2030 |
20 | Market Segmentation, Dynamics and Forecast by End use, 2024-2030 |
21 | Product installation rate by OEM, 2023 |
22 | Incline/Decline in Average B-2-B selling price in past 5 years |
23 | Competition from substitute products |
24 | Gross margin and average profitability of suppliers |
25 | New product development in past 12 months |
26 | M&A in past 12 months |
27 | Growth strategy of leading players |
28 | Market share of vendors, 2023 |
29 | Company Profiles |
30 | Unmet needs and opportunity for new suppliers |
31 | Conclusion |
32 | Appendix |