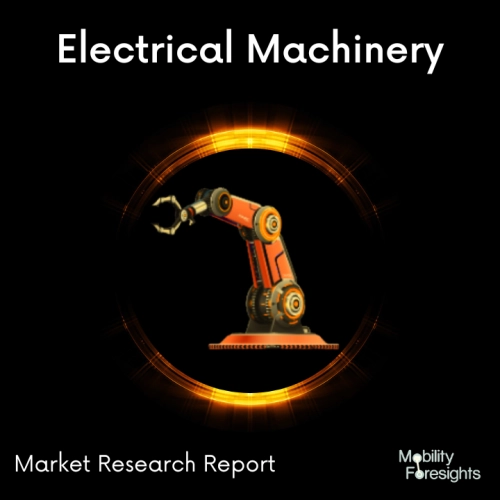
- Get in Touch with Us
Last Updated: Apr 25, 2025 | Study Period: 2024-2030
The purpose of the Pipe Cruise Robot is to check and measure pipes. It is possible to inspect any type of pipe with this robust and modular equipment.
A solid frame, additional dust sealing, waterproofing, and waterproofing allow for operation in both dry and dusty, wet or other liquid-filled environments.
A secret modification to a ship's oily water separator (OWS) or other waste-handling machinery is known as a "magic pipe," which permits waste liquids to be discharged in violation of maritime pollution standards.
Such equipment modifications may allow the untreated discharge of hundreds of thousands of gallons of contaminated water, severely polluting marine waters. On board a ship, the pipe might be made from existing hoses and pumps to release untreated wastewater into the water.
Due to deterioration over time, oil pipelines need to be periodically inspected. Such deterioration is caused by a wide range of reasons, including corrosion, leaks, and cracks, which can result in blowbacks and harm to the environment and operators.
As robotics technology develops, numerous mobile robots and systems are created to address this problem. By using these types of inspection robots, which can be deployed more quickly and safely than assigning human workers to dangerous situations, human workers can avoid the high-risk inspection task in oil pipelines.
The Global Pipe Cruise Robot market accountedfor $XX Billion in 2023 and is anticipated to reach $XX Billion by 2030, registering a CAGR of XX% from 2024 to 2030.
Due to consistent growth and promising future developments, the robotics market has stood out for a number of years. Industrial robots are a crucial component of contemporary production halls all over the world. They serve as the foundation for accuracy, consistency in quality, and quick processing times.
Electronics and mechanics must work safely together at the same time. The requirements for products destined for the robotics sector are specialised, and finding the necessary technical solutions is frequently fairly difficult.
Robotics-related products must adhere to the strictest mechanical, chemical, and thermal specifications. Rapid acceleration and deceleration, tensile, compressive, and torsion stress, as well as millions of bending cycles, must all be tolerated by the goods.
They must also withstand high temperatures, weld spatters, oil, and several other contaminants. With these systems, preserving system productivity comes first, which also ensures the dependability of the cables and system solutions.
Sl no | Topic |
1 | Market Segmentation |
2 | Scope of the report |
3 | Abbreviations |
4 | Research Methodology |
5 | Executive Summary |
6 | Introduction |
7 | Insights from Industry stakeholders |
8 | Cost breakdown of Product by sub-components and average profit margin |
9 | Disruptive innovation in the Industry |
10 | Technology trends in the Industry |
11 | Consumer trends in the industry |
12 | Recent Production Milestones |
13 | Component Manufacturing in US, EU and China |
14 | COVID-19 impact on overall market |
15 | COVID-19 impact on Production of components |
16 | COVID-19 impact on Point of sale |
17 | Market Segmentation, Dynamics and Forecast by Geography, 2024-2030 |
18 | Market Segmentation, Dynamics and Forecast by Product Type, 2024-2030 |
19 | Market Segmentation, Dynamics and Forecast by Application, 2024-2030 |
20 | Market Segmentation, Dynamics and Forecast by End use, 2024-2030 |
21 | Product installation rate by OEM, 2023 |
22 | Incline/Decline in Average B-2-B selling price in past 5 years |
23 | Competition from substitute products |
24 | Gross margin and average profitability of suppliers |
25 | New product development in past 12 months |
26 | M&A in past 12 months |
27 | Growth strategy of leading players |
28 | Market share of vendors, 2023 |
29 | Company Profiles |
30 | Unmet needs and opportunity for new suppliers |
31 | Conclusion |
32 | Appendix |