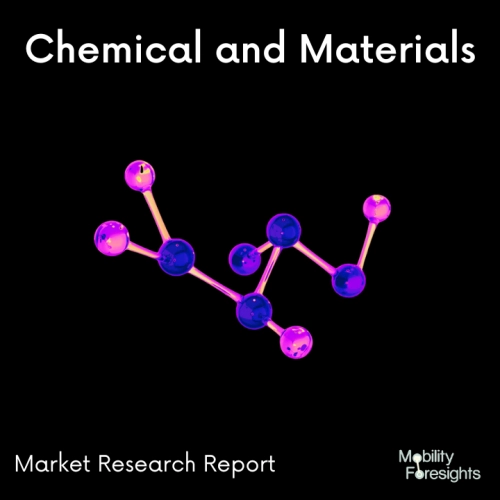
- Get in Touch with Us
Last Updated: Apr 25, 2025 | Study Period: 2024-2030
Two common techniques are used to make carbon fibre: utilising polyacrylonitrile and making it from pitch. Aromatic hydrocarbons make up pitch, a viscoelastic substance. Pitch is made by distilling carbon-based substances including plants, crude oil, and coal.
Aromatic hydrocarbons make up pitch, a viscoelastic substance. Pitch is made by distilling carbon-based substances including plants, coal, and crude oil.
Although pitch is isotropic, thermal treatments can turn it anisotropic. The ability to melt spin anisotropic mesophase pitch without filament breakage makes mesophase pitch the most significant in the manufacturing of carbon fibre.
Pitch may arrange and form linear chains without the aid of tension because the mesophase pitch creates a thermotropic crystal. By polymerizing isotropic pitch to a greater molecular weight, mesophase pitch is created.
These four key processes are responsible for the great strength of carbon fibre. The fibres can sustain high levels of stress because they have a high concentration of crystalline areas.
These crystals are stiff patches that do not deform when an external stress is applied, and they are created by the melt spinning process.
Global pitch-based carbon fiber market accounted for $XX Billion in 2023 and is anticipated to reach $XX Billion by 2030, registering a CAGR of XX% from 2024 to 2030.
A new grade of pitch-based carbon fibre is now fully produced, according to Mitsubishi Plastics.
The new product (DIALEAD K13312) has been developed with a tensile strength of 3,200 MPa (Mega Pascal), which is roughly 20% higher than the Company's conventional products.
It also has a very good tensile modulus (rigidity). K13312's workability has also increased (handling capability).
Carbon fibre is currently divided into two primary categories: pitch-based and polyacrylonitrile (PAN)-based. The excellent tensile modulus (rigidity) and heat conductivity of pitch-based carbon fibre make it possible to create carbon-fibre-reinforced polymers (CFRP) with almost little thermal expansion.
The Tokyo Metropolitan Expressway, where significant reinforcement work is being done, is now using this innovative product. Future application possibilities are anticipated to increase, including the strengthening of deteriorating bridges and structures.
Enhancing workability speeds up processing, decreases customer costs, and creates new applications for "DIALEAD K13312" that go beyond carbon fibre reinforcing sheets to include items in the energy and sporting goods industries.
Sl no | Topic |
1 | Market Segmentation |
2 | Scope of the report |
3 | Abbreviations |
4 | Research Methodology |
5 | Executive Summary |
6 | Introduction |
7 | Insights from Industry stakeholders |
8 | Cost breakdown of Product by sub-components and average profit margin |
9 | Disruptive innovation in the Industry |
10 | Technology trends in the Industry |
11 | Consumer trends in the industry |
12 | Recent Production Milestones |
13 | Component Manufacturing in US, EU and China |
14 | COVID-19 impact on overall market |
15 | COVID-19 impact on Production of components |
16 | COVID-19 impact on Point of sale |
17 | Market Segmentation, Dynamics and Forecast by Geography, 2024-2030 |
18 | Market Segmentation, Dynamics and Forecast by Product Type, 2024-2030 |
19 | Market Segmentation, Dynamics and Forecast by Application, 2024-2030 |
20 | Market Segmentation, Dynamics and Forecast by End use, 2024-2030 |
21 | Product installation rate by OEM, 2023 |
22 | Incline/Decline in Average B-2-B selling price in past 5 years |
23 | Competition from substitute products |
24 | Gross margin and average profitability of suppliers |
25 | New product development in past 12 months |
26 | M&A in past 12 months |
27 | Growth strategy of leading players |
28 | Market share of vendors, 2023 |
29 | Company Profiles |
30 | Unmet needs and opportunity for new suppliers |
31 | Conclusion |
32 | Appendix |