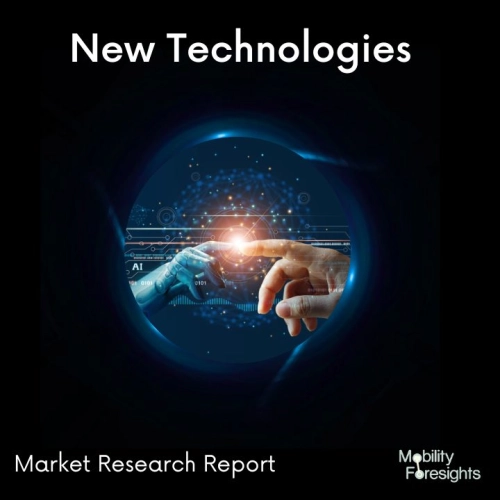
- Get in Touch with Us
Last Updated: Apr 25, 2025 | Study Period: 2024-2030
The Asia-Pacific region, particularly countries like China, Japan, South Korea, and Taiwan, is a major hub for semiconductor manufacturing. Hence, it tends to dominate the market in terms of demand for plasma abatement systems.
North America and Europe also have a significant presence in the market, with a focus on technological innovation and compliance with environmental regulations.
Environmental regulations regarding the emission of hazardous gases in manufacturing processes have become stricter. Plasma abatement systems play a key role in ensuring compliance with these regulations.
Ongoing advancements in semiconductor technology drive the need for more efficient plasma abatement systems with improved processing capabilities, reduced energy consumption, and better environmental performance.
The semiconductor industry is known for its rapid technological changes. Companies in this market need to adapt quickly to new manufacturing processes and materials.
There is a growing emphasis on green and sustainable manufacturing processes. Plasma abatement systems that offer eco-friendly and energy-efficient solutions are likely to find increased demand.
The market is expected to witness continued growth, driven by the expansion of the semiconductor industry, the need for environmental compliance, and technological advancements in plasma abatement systems.
Awareness of global warming is increasing, and the regulatory push to effect reduction is in full swing. Recognizing this, Applied Materials continues to search for proactive, cost-effective ways of reducing high global-warming potential (GWP) of the gaseous chemicals used, which includes perfluorocarbon compounds (PFCs), NF3and SF6.
The Applied Aeris-G system is a pre-pump plasma abatement solution that uses less energy by treating the actual process gas volumeâa smaller and more concentrated volume than what is treated by post-pump abatement units.
The plasma dissociation combined with the low volume of nitrogen in the Aeris-G chamber during abatement minimizes NOx emissions to near zero. The Aeris-G unit operates "on-demand," further reducing operating costs compared to energy-hungry, continuous operation post-pump abatement.
Plasma abatement systems use a small plasma source that effectively dissociates the F-GHG molecules that react with fragments of the additive gas (hydrogen, oxygen, water, or CH4 ) to produce low molecular weight by-products such as HF with little or no GWP. After disassociation, wet scrubbers can remove the molecules. The presence of additive gas is necessary to prevent later downstream reformation of F-GHG molecules
By treating the actual process gas volume a lower and more concentrated volume than what is treated by post-pump abatement units, plasma abatement utilizes less energy.
In the course of abatement, NOx emissions are reduced to almost nothing thanks to plasma dissociation and the small amount of nitrogen present in the Aeris-G chamber. By functioning âon-demand,â the Aeris-G unit lowers operating expenses compared to continuous, energy-guzzling operation after pump abatement.
The global warming gases CF4 and C4F8 can be effectively eliminated using the plasma abatement technology. In order to drastically reduce air pollution, it is essential to destroy greenhouse gases, notably perfluoro compounds, hydro fluoro compounds, chloro fluoro compounds, and SF6.
An abatement system for chemicals produced in semiconductor processes is one of the embodiments. A plasma source with a first plate and a second plate that are parallel to the first plate is part of the abatement system.
The first plurality of magnets is placed on the first plate of the plasma source, and a second plurality is placed on the second plate.The electric field formed between the electrode and the outside wall is essentially parallel to the magnetic field produced by the first and second pluralities of magnets. This arrangement results in the formation of dense plasma.
The Global Plasma abatement system market accounted for $XX Billion in 2023 and is anticipated to reach $XX Billion by 2030, registering a CAGR of XX% from 2024 to 2030.
Ebara Corporation Announces New Plasma Abatement System for Semiconductor Manufacturing
Ebara Corporation, a leading provider of industrial machinery, has announced the launch of its new plasma abatement system specifically designed for the semiconductor manufacturing industry.The new system, called the Ebara Plasma Abatement System (EPAS), is said to offer significant advantages over existing technologies. EPAS is said to be able to remove up to 99.99% of hazardous gases from exhaust streams, compared to 95-98% for traditional systems.
Global Standard Technology (GST) Partners with CS Clean Solutions to Expand Plasma Abatement System Offering
Global Standard Technology (GST), a leading provider of plasma abatement systems, has announced a new partnership with CS Clean Solutions, a manufacturer of air pollution control equipment. The partnership will combine GST's expertise in plasma abatement technology with CS Clean Solutions' experience in air pollution control to offer a more comprehensive range of products and services to customers.The two companies will also collaborate on developing new plasma abatement technologies for emerging applications.This partnership is expected to further strengthen GST's position as a leader in the global plasma abatement systems market.
Environmental Compliance
Growing awareness and stricter environmental regulations contribute to the demand for plasma abatement systems that can effectively and efficiently remove hazardous gases generated during semiconductor manufacturing. Systems that offer better environmental performance and comply with global regulations gain prominence.
Increased Focus on Green Technologies
There is a heightened focus on sustainable and eco-friendly manufacturing practices. Plasma abatement systems that operate with reduced energy consumption, minimal environmental impact, and efficient gas abatement technologies are gaining traction.
Integration with Industry 4.0
Integration with Industry 4.0 principles, including IoT (Internet of Things) connectivity and data analytics, allows for real-time monitoring and predictive maintenance of plasma abatement systems. Smart, connected systems enhance efficiency and reduce downtime.
Busch Vacuum Solutions Launches New Dry-Type Plasma Abatement System:
Busch Vacuum Solutions, another major player in the vacuum technology market, has also recently launched a new plasma abatement system. The new system, called the Busch Dry-Type Plasma Abatement System (Dry-PAC), is designed to be a more cost-effective alternative to wet-type systems.It does not require the use of water or chemicals, which can help to reduce operating costs.Dry-PAC is more compact than wet-type systems, making it easier to install and maintain and does not generate any wastewater or hazardous waste, making it a more environmentally friendly option.
Ebara Corporation's EcoPlasma X:This revolutionary system boasts an impressive 99.999% removal rate of hazardous gases, alongside significant energy savings and a compact footprint. Its modular design and automation features further enhance its appeal. EcoPlasma X features a significantly smaller footprint than traditional systems, offering greater flexibility and ease of installation.It utilizes a closed-loop system, eliminating wastewater and hazardous waste generation, and minimizing its environmental footprint.
Global Standard Technology's (GST) PlasmaPRO 5.0:This advanced system features a next-generation plasma generator for even greater efficiency and reduced maintenance requirements. Additionally, its enhanced user interface simplifies operation and monitoring.
Sl no | Topic |
1 | Market Segmentation |
2 | Scope of the report |
3 | Research Methodology |
4 | Executive Summary |
5 | Average B2b Price, By Region |
6 | Potential Opportunities For Client |
7 | Introduction |
8 | Insights from Industry stakeholders |
9 | Disruptive innovation in the Industry |
10 | Technology trends in the Industry |
11 | Consumer trends in the industry |
12 | Recent Production Milestones |
13 | Specific challenges and considerations related to implementingGlobal Plasma Abatementsystems. |
14 | Advantages and obstacles associated with the use ofGlobal Plasma Abatementin healthcare. |
15 | The role ofGlobal Plasma Abatementin remote patient monitoring and telehealth initiatives. |
16 | New product development in past 12 months |
17 | Market Size, Dynamics and Forecast by Geography, 2024-2030 |
18 | Market Size, Dynamics and Forecast by Product Type, 2024-2030 |
19 | Market Size, Dynamics and Forecast by Application, 2024-2030 |
20 | Market Size, Dynamics and Forecast by End user, 2024-2030 |
21 | Competitive Landscape |
22 | M&A in past 12 months |
23 | Growth strategy of leading players |
24 | Market share of vendors, 2024 |
25 | Company Profiles |
26 | Unmet needs and opportunity for new suppliers |
27 | Conclusion |