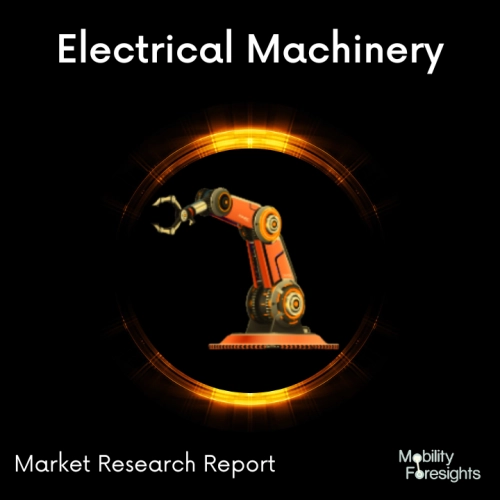
- Get in Touch with Us
Last Updated: Apr 25, 2025 | Study Period: 2024-2030
The blowing machine and plastic particles used in this procedure have an impact on the quality of the film material produced. A machine known as a "film blowing machine" warms and blows plastic particles into plastic film.
For the production of plastic film, plastic film blowing machines are frequently employed. From basic daily necessities to the healthcare sector and beyond, these things are used frequently in our daily lives.
A mechanical device that produces plastic film with high technique and precise setting is called a plastic film blowing machine.The film tube is pushed upward by nip rollers after leaving the die while still in a plastic condition. In order to create the correct film thickness and width, pressurized air is simultaneously blasted into the film tube.
The Global Plastic Film Blowing Machine Market accounted for $XX Billion in 2023 and is anticipated to reach $XX Billion by 2030, registering a CAGR of XX% from 2024 to 2030.
This spring, Eisenhauer introduced its Evolution five-layer blown film line for making form-fill-seal (FFS) film during an open house. The open house was hosted at KZPM, Eisenhauer's first client for the new line and a producer of polymeric films and flexible packaging in Kazan, Russia.
The production line is intended to provide film for heavy-duty shipping sacks for petrochemical packaging. It highlights our capacity to meet customer requests as a tailored solution for tubular heavy-duty shipping sacks (HDSS).
These FFS bags have historically always been produced as a three-layer product, especially for resin sacks. This is referred to as the Evolution 5L FFS line. Evolution Blown Film Die Heads generate accurate layer thicknesses and require brief start-up and change-over times, the business claimed.
Costs are decreased because the thinner outer layers require lower quantities of additives and resin, and makers can utilize less expensive, recycled resin in the core layer.
With five layers, center-holed internal bubble cooling, a 175mm diameter, and rates up to 480 kilograms (1,058 pounds) per hour, the die head is brand-new and made exclusively for this application. Producers can adjust their structure, recipes, etc. to take advantage of thinner skin layers because there are five layers as opposed to the traditional three layers.
Sl no | Topic |
1 | Market Segmentation |
2 | Scope of the report |
3 | Abbreviations |
4 | Research Methodology |
5 | Executive Summary |
6 | Introduction |
7 | Insights from Industry stakeholders |
8 | Cost breakdown of Product by sub-components and average profit margin |
9 | Disruptive innovation in the Industry |
10 | Technology trends in the Industry |
11 | Consumer trends in the industry |
12 | Recent Production Milestones |
13 | Component Manufacturing in US, EU and China |
14 | COVID-19 impact on overall market |
15 | COVID-19 impact on Production of components |
16 | COVID-19 impact on Point of sale |
17 | Market Segmentation, Dynamics and Forecast by Geography, 2024-2030 |
18 | Market Segmentation, Dynamics and Forecast by Product Type, 2024-2030 |
19 | Market Segmentation, Dynamics and Forecast by Application, 2024-2030 |
20 | Market Segmentation, Dynamics and Forecast by End use, 2024-2030 |
21 | Product installation rate by OEM, 2023 |
22 | Incline/Decline in Average B-2-B selling price in past 5 years |
23 | Competition from substitute products |
24 | Gross margin and average profitability of suppliers |
25 | New product development in past 12 months |
26 | M&A in past 12 months |
27 | Growth strategy of leading players |
28 | Market share of vendors, 2023 |
29 | Company Profiles |
30 | Unmet needs and opportunity for new suppliers |
31 | Conclusion |
32 | Appendix |