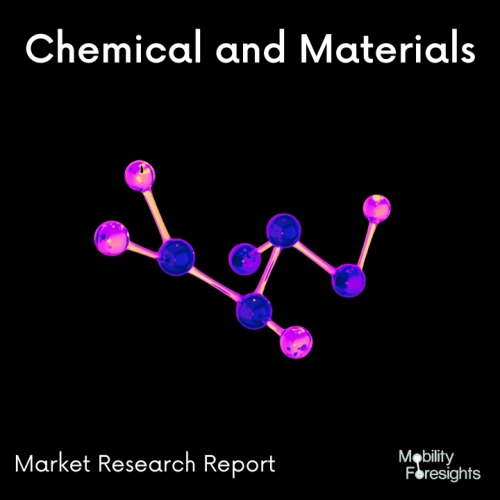
- Get in Touch with Us
Last Updated: Apr 25, 2025 | Study Period: 2023-2030
Polyamide compounding is the process of blending different additives, fillers, reinforcements, and modifiers with polyamide (PA) resins to improve the properties and performance of the final polymer compound.
A versatile and often used thermoplastic polymer with the trade name "nylon," polyamide is renowned for its superior mechanical characteristics, high strength, and durability.
Polyamide resins are often melted and blended with other materials using extrusion or melt-blending methods during the compounding process.
Depending on the particular needs, the additives, and modifiers can be added into the polyamide matrix in a variety of forms, including powders, pellets, or liquids.
The goal of polyamide compounding is to modify the underlying polymer's characteristics to suit a variety of application requirements. By including new ingredients, the compound can perform better in areas such as:
Reinforcement: To improve the strength, stiffness, and dimensional stability of polyamide compounds, a variety of fillers and reinforcements, such as glass fibers, mineral fillers, or carbon fibers, can be added. These reinforcements can enhance the compound's mechanical characteristics and enable use in demanding applications.
Flame retardancy: The polyamide compound can be given additives to increase its flame resistance and decrease its flammability. When it comes to applications where fire safety is an issue, this is especially crucial.
Heat resistance: By using specific additives, such as heat stabilizers or flame retardants, polyamide compounds can endure greater temperatures without losing their mechanical qualities.
Chemical resistance: Chemicals like oils, fuels, or solvents can be added to polyamide compounds' formulas to increase their resistance to these substances. This qualifies them for use when exposure to corrosive chemicals is anticipated.
UV stability: To prevent degradation brought on by prolonged exposure to sunlight or other UV sources, ultraviolet (UV) stabilizers can be added to polyamide compounds.
Electrical conductivity: Polyamide compounds can display electrical conductivity or static dissipation qualities by introducing conductive fillers or additives, making them appropriate for applications where electrostatic discharge (ESD) management is required.
In order to meet unique performance needs in sectors including automotive, electrical, and electronics, consumer products, and industrial applications, polyamide compounding enables the customization of polyamide-based materials. The resultant compounds may have a variety of qualities that make them suitable for use in a variety of challenging settings and applications.
The Polyamide Compounding Market In India accounted for $XX Billion in 2022 and is anticipated to reach $XX Billion by 2030, registering a CAGR of XX% from 2023 to 2030.
A number of novel long-chain polyamides and high-temperature polyamides will be released by Ascend Performance Materials. A new line of heat-stabilized polyamide 66 and copolymers called Vydyne XHT can endure extended exposure to temperatures of up to 230 °C.
While maintaining the processability, durability, and mechanical qualities for which PA66 is renowned, XHT products push the limits of temperature resistance by combining special polymer chemistries with a multi-stage heat stabilization technology.
For usage in demanding automotive applications including charge air coolers, integrated air intake manifolds, exhaust gas recirculation, and resonators, the Vydyne XHT range offers four glass-filled grades. All XHT grades have good flow characteristics, and as they can all be regained, excess material can be used again, increasing production effectiveness.
Sl no | Topic |
1 | Market Segmentation |
2 | Scope of the report |
3 | Abbreviations |
4 | Research Methodology |
5 | Executive Summary |
6 | Introduction |
7 | Insights from Industry stakeholders |
8 | Cost breakdown of Product by sub-components and average profit margin |
9 | Disruptive innovation in the Industry |
10 | Technology trends in the Industry |
11 | Consumer trends in the industry |
12 | Recent Production Milestones |
13 | Component Manufacturing in US, EU and China |
14 | COVID-19 impact on overall market |
15 | COVID-19 impact on Production of components |
16 | COVID-19 impact on Point of sale |
17 | Market Segmentation, Dynamics and Forecast by Geography, 2023-2030 |
18 | Market Segmentation, Dynamics and Forecast by Product Type, 2023-2030 |
19 | Market Segmentation, Dynamics and Forecast by Application, 2023-2030 |
20 | Market Segmentation, Dynamics and Forecast by End use, 2023-2030 |
21 | Product installation rate by OEM, 2023 |
22 | Incline/Decline in Average B-2-B selling price in past 5 years |
23 | Competition from substitute products |
24 | Gross margin and average profitability of suppliers |
25 | New product development in past 12 months |
26 | M&A in past 12 months |
27 | Growth strategy of leading players |
28 | Market share of vendors, 2023 |
29 | Company Profiles |
30 | Unmet needs and opportunity for new suppliers |
31 | Conclusion |
32 | Appendix |