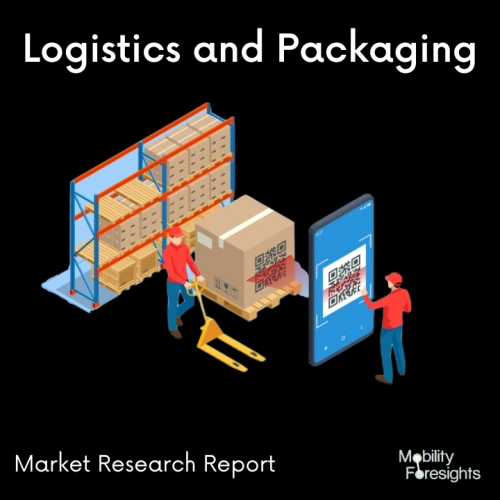
- Get in Touch with Us
Last Updated: Apr 25, 2025 | Study Period: 2023-2030
an excellent replacement for straws and disposable tableware used in the fast-food sector. potato-based bioplastic packaging is used that broke down in a few months. they heated potato husk with water for this purpose.
The solution thickened at each stage, and it was then added to the pattern to create spoons and other things. It is a particular type of thermoplastic that becomes soft at low temperatures yet hard at high temperatures. The same way that potatoes are prepped for plastic for the specialty food market, bags, cutlery, and straws can also be produced.
All bioplastics start with naturally occurring sugars or starches found in plants, with sugar cane or maize starches frequently chosen as the preferred feedstocks. However, potatoes, which, depending on their water level, can range in dry matter (starch) composition from 13% to as much as 23%, may be perfect for some polymers.
In an effort to develop new, more lucrative crops for Canada's potato farmers, food scientists, molecular biologists, and plant production experts across the country looked into potential functional food-ingredient and non-food applications.
The Global potato-based bioplastic packaging market accounted for $XX Billion in 2022 and is anticipated to reach $XX Billion by 2030, registering a CAGR of XX% from 2023 to 2030.
In their research Esen Gokce Ozdamara and Murat Ates investigated the production of potato-based bioplastic packaging from starch. This equation results in the formation of a straightforward bioplastic: Plasticizers, additional additives, and biopolymers together make up bioplastic. . It costs less than standard polymers and is environmentally beneficial.
they have created bioplastics from renewable sources. Because of burning plastic, toxic pollutants including carbon dioxide and methane are produced. The climate change is negatively impacted by these greenhouse gases (GHGs). Additionally, it is anticipated that the cost of fossil fuels would increase and their supply will become more unstable. An effort is undertaken to get the bioplastic material ready.
To extract starch, one to three uncooked potatoes were cut into small pieces and used. In order to remove the starch from the potatoes, a mortar and pestle were used. The potatoes were chopped, and tap water was added.
To allow the starch to sink to the bottom of the solution, it was left undisturbed for roughly an hour. To extract starch in its purest form, the supernatant was discarded, and distilled water was used to wash the results. Sun drying was used to dry the material. A starch was produced after 48 hours of sun drying.
Sl no | Topic |
1 | Market Segmentation |
2 | Scope of the report |
3 | Abbreviations |
4 | Research Methodology |
5 | Executive Summary |
6 | Introduction |
7 | Insights from Industry stakeholders |
8 | Cost breakdown of Product by sub-components and average profit margin |
9 | Disruptive innovation in the Industry |
10 | Technology trends in the Industry |
11 | Consumer trends in the industry |
12 | Recent Production Milestones |
13 | Component Manufacturing in US, EU and China |
14 | COVID-19 impact on overall market |
15 | COVID-19 impact on Production of components |
16 | COVID-19 impact on Point of sale |
17 | Market Segmentation, Dynamics and Forecast by Geography, 2023-2030 |
18 | Market Segmentation, Dynamics and Forecast by Product Type, 2023-2030 |
19 | Market Segmentation, Dynamics and Forecast by Application, 2023-2030 |
20 | Market Segmentation, Dynamics and Forecast by End use, 2023-2030 |
21 | Product installation rate by OEM, 2023 |
22 | Incline/Decline in Average B-2-B selling price in past 5 years |
23 | Competition from substitute products |
24 | Gross margin and average profitability of suppliers |
25 | New product development in past 12 months |
26 | M&A in past 12 months |
27 | Growth strategy of leading players |
28 | Market share of vendors, 2023 |
29 | Company Profiles |
30 | Unmet needs and opportunity for new suppliers |
31 | Conclusion |
32 | Appendix |